小型气体容器检测的重要性与核心项目
小型气体容器作为工业、医疗、消防等领域中广泛使用的压力装置,其安全性与可靠性直接关系到人员生命财产安全和环境保护。根据国际标准化组织(ISO)及各国特种设备安全法规要求,此类容器需定期进行系统性检测,以评估其材质完整性、密封性能及承压能力。由于容器内部通常存储易燃、易爆或高压气体,任何微小的缺陷都可能引发泄漏、爆炸等严重事故,因此检测流程需覆盖物理状态、功能性指标及合规性验证三大维度。
核心检测项目分类
1. 外观与结构完整性检查
通过目视检验和仪器测量,排查容器表面是否存在腐蚀、凹陷、裂纹或焊接缺陷。重点检测颈口、焊缝区域及底座连接处,使用超声波测厚仪验证壁厚是否符合安全冗余标准。同时核对容器铭牌信息与登记档案的一致性。
2. 气密性测试
采用惰性气体(如氮气)加压至1.25倍工作压力,通过保压试验检测泄漏情况。结合气泡法或红外检漏仪对阀门、接口等关键部位进行精细化排查,确保无微泄漏风险。
3. 阀门与安全装置功能性检测
验证泄压阀、压力表的动作精度及响应速度,检查防爆片的完整性。通过模拟超压场景测试安全阀开启压力值,确保其符合GB/T 12241标准要求。
4. 材料性能评估
利用磁粉探伤(MPI)或渗透检测(PT)等无损检测技术,识别金属疲劳、晶间腐蚀等微观缺陷。对使用年限超标的容器需进行金相分析,评估材料延展性和抗脆裂性能的退化程度。
5. 残余气体处理与内部清洁度检测
在开罐检验前需彻底置换残留气体,使用气体检测仪确认氧气含量达到19.5%-23.5%的安全范围。通过内窥镜检查容器内壁是否存在污染物或化学反应沉积物。
6. 压力循环测试
模拟实际使用工况,对容器进行至少500次充放循环测试,观察是否存在塑性变形或疲劳失效迹象。该测试尤其适用于可重复充装的液化石油气(LPG)钢瓶。
7. 合规性文件审核
核查制造许可证、产品合格证、定期检验报告等文件,确认容器符合TSG 21-2016《固定式压力容器安全技术监察规程》等强制性标准,并验证二维码/电子标签等追溯系统的有效性。
通过上述系统性检测,可准确评估小型气体容器的安全状态,有效预防事故风险。检测机构需配备经 认证的检测设备,并由持有特种设备检验资质的人员操作,确保检测结果的权威性和法律效力。
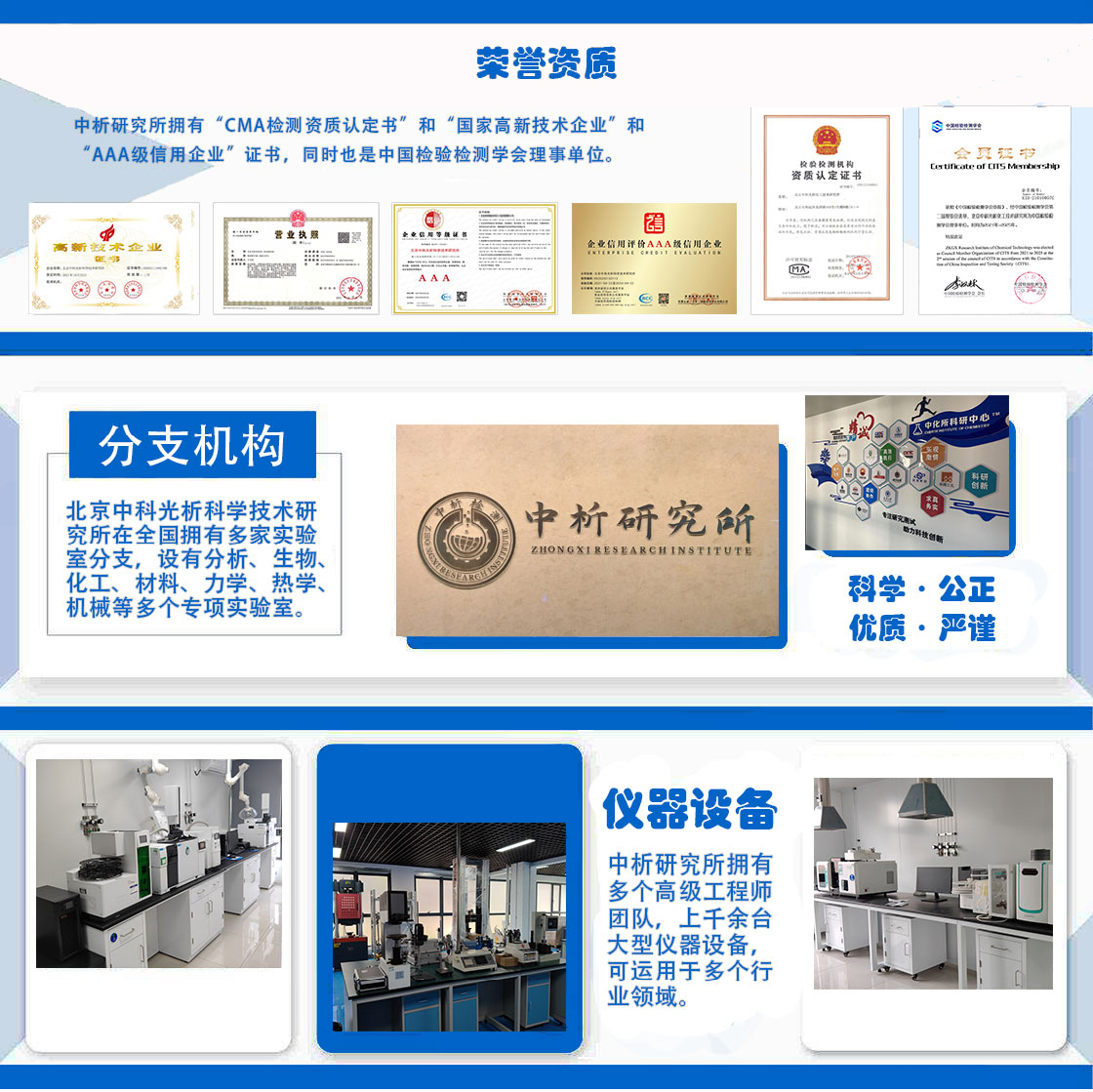
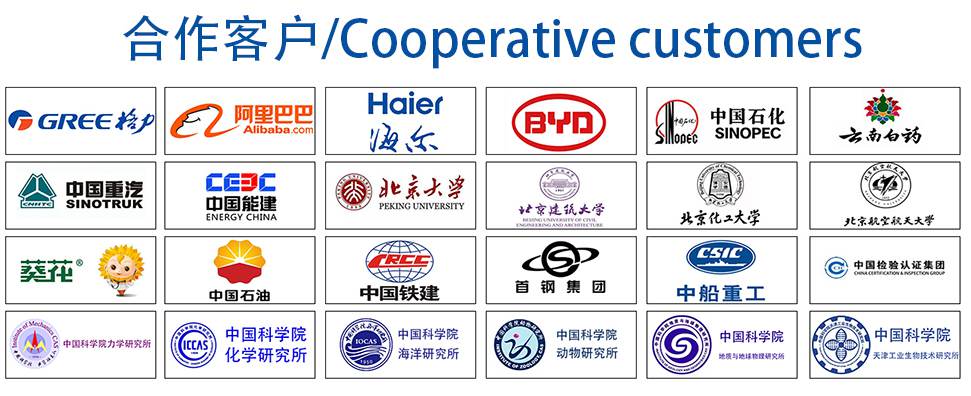