液氨检测的重要性与核心关注点
液氨作为广泛应用于制冷工业、化工生产等领域的重要化工原料,其高毒性与易燃易爆特性使安全检测成为重中之重。当液氨浓度超过50ppm时,人体会出现呼吸道刺激症状;达到500ppm时可引发肺水肿;若达到1500ppm以上则具有致命风险。因此建立系统化的液氨检测体系,既是保障生产安全的必要措施,也是环境保护的重要防线。
液氨检测五大核心项目解析
1. 储罐区浓度实时监测
采用固定式氨气探测器对储罐区进行24小时连续监测,重点检测阀门法兰、泵体密封等易泄漏部位。监测系统需具备声光报警功能,设定一级报警值(通常为25ppm)和二级报警值(100ppm),同时联动通风系统启动。
2. 生产装置泄漏扫描检测
使用红外成像仪对反应釜、换热器等高温高压设备进行热成像检测,通过氨气对特定红外波段的吸收特性定位微小泄漏。便携式检测仪(PID检测器)可精准测量0.1-2000ppm浓度范围,检测精度达±3%F.S。
3. 作业环境空气质量检测
按照GBZ2.1标准,在工作区域布设网格化监测点,重点监测压缩机房、充装台等高风险区域。检测项目包括:时间加权平均浓度(TWA,限值20ppm)、短期接触浓度(STEL,限值35ppm)及峰值浓度控制。
4. 排污口废气专项检测
通过在线质谱分析系统对尾气处理装置出口进行连续监测,检测氨逃逸浓度(标准限值10mg/m³)。同时定期采用化学吸收法(靛酚蓝分光光度法)进行实验室比对分析,确保检测数据可靠性。
5. 应急检测与溯源分析
配置配备FID检测器的移动监测车,可在事故现场快速建立三维浓度分布图。气相色谱-质谱联用仪(GC-MS)用于事故后污染物溯源分析,检测灵敏度可达ppb级,准确识别泄漏源。
创新检测技术应用趋势
新型半导体式氨传感器采用纳米氧化锌复合材料,响应时间缩短至3秒,使用寿命延长至5年。物联网技术的应用实现了检测数据的云端存储与智能预警,通过机器学习算法可预测设备失效概率,将事故防范从被动检测转向主动预防。
液氨检测体系的构建需要综合运用固定监测与移动检测、在线监测与实验室分析、常规检测与智能预警等多种手段。通过严格执行检测标准(如AQ3046-2013),定期进行设备校准(建议每季度进行1次标准气体标定),方能筑牢安全生产的多重防线,实现风险的全过程管控。
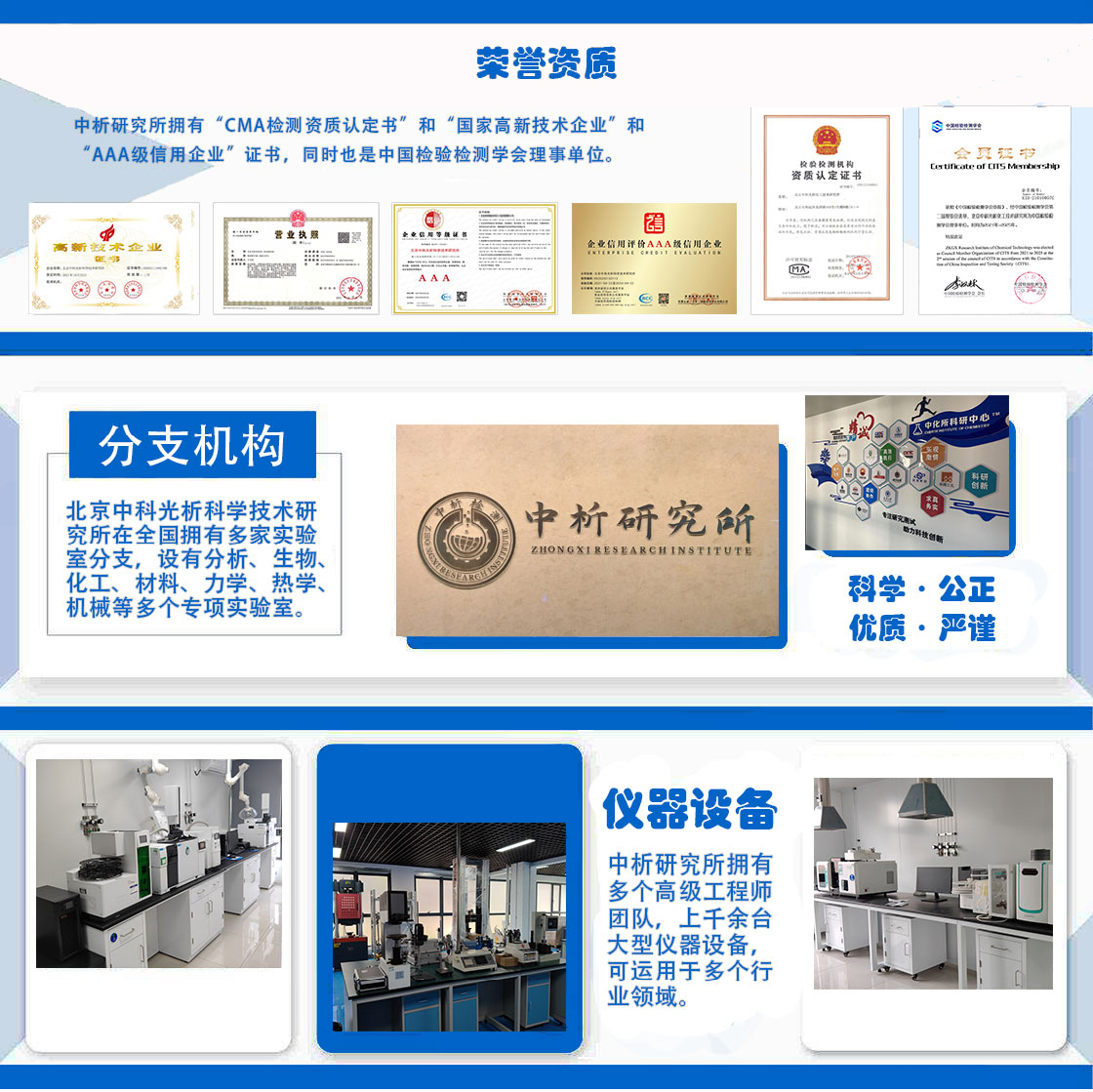
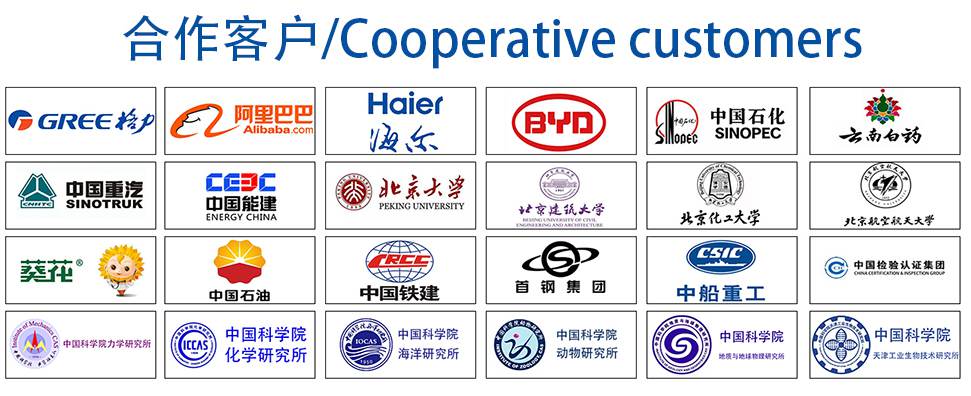