铁路混凝土检测
实验室拥有众多大型仪器及各类分析检测设备,研究所长期与各大企业、高校和科研院所保持合作伙伴关系,始终以科学研究为首任,以客户为中心,不断提高自身综合检测能力和水平,致力于成为全国科学材料研发领域服务平台。
立即咨询铁路混凝土检测:保障轨道工程质量的基石
在铁路工程建设领域,混凝土作为轨道板、桥梁墩台、轨枕等关键部位的主要建筑材料,其质量直接关系到铁路运营安全和使用寿命。随着我国高速铁路网不断延伸,混凝土结构面临的动荷载、环境侵蚀等挑战日益严峻,这使得铁路混凝土检测工作成为保障工程质量的重要防线。根据《铁路混凝土结构耐久性设计规范》(TB 10005)要求,从原材料进场到施工过程监控,再到竣工验收维护,整个生命周期都需要实施严格的检测程序。
一、核心检测项目体系
现代铁路混凝土检测涵盖三大维度指标,构成严密的质量控制网络:
1. 物理力学性能检测
抗压强度检测:采用标准立方体试件(150×150×150mm)进行压力测试,执行GB/T 50081标准,高速铁路轨道板要求28天强度不低于C60。
弹性模量测定:通过静态压缩试验获取应力-应变曲线,控制值为33-35GPa,确保结构刚度符合设计要求。
抗折强度验证:针对轨枕等受弯构件,按TB/T 2190标准执行三点弯曲试验,指标值≥6.5MPa。
2. 耐久性专项检测
冻融循环测试:模拟严寒环境进行300次快速冻融,质量损失率需<5%,相对动弹性模量保持率>60%。
氯离子渗透试验:采用RCM法测定扩散系数,沿海地区要求≤3.0×10⁻¹²m²/s。
碳化深度检测:使用酚酞试剂法测量,年平均碳化速度控制在0.5mm/年以内。
3. 施工质量监控指标
坍落度动态监测:采用全自动坍落度仪每2小时检测一次,高速铁路现浇梁控制值180±20mm。
含气量测定:气压法检测保证4-6%含气量,提升抗冻性能。
保护层厚度扫描:使用电磁感应仪全断面检测,允许偏差±3mm。
二、前沿检测技术创新
智能检测技术正在重塑行业标准:
三维超声成像技术:可探测0.1mm级微裂缝,定位精度达±5mm
光纤光栅传感系统:植入式传感器实现混凝土应力应变实时监测
微波湿度检测仪:非接触式测定养护期间含水率变化
AI图像识别系统:通过卷积神经网络自动判定表面缺陷类型
三、全生命周期质量管理
完善的检测体系贯穿工程各阶段:
材料进场阶段:水泥氯离子含量、骨料碱活性等18项指标筛查
拌和生产阶段:计量系统误差<1%,温度监控±2℃精度
浇筑养护阶段:红外热成像监控温度梯度,确保不超过25℃/m
运营维护阶段:车载探地雷达每年进行结构层完整性普查
通过构建"原材料-生产过程-实体质量-服役状态"的闭环检测体系,我国铁路混凝土结构平均使用寿命已从30年提升至100年,重大质量事故率下降至0.02‰以下。随着智能传感、大数据分析等技术的深度融合,铁路混凝土检测正朝着无人化、实时化、预测性方向发展,为交通强国建设提供坚实保障。
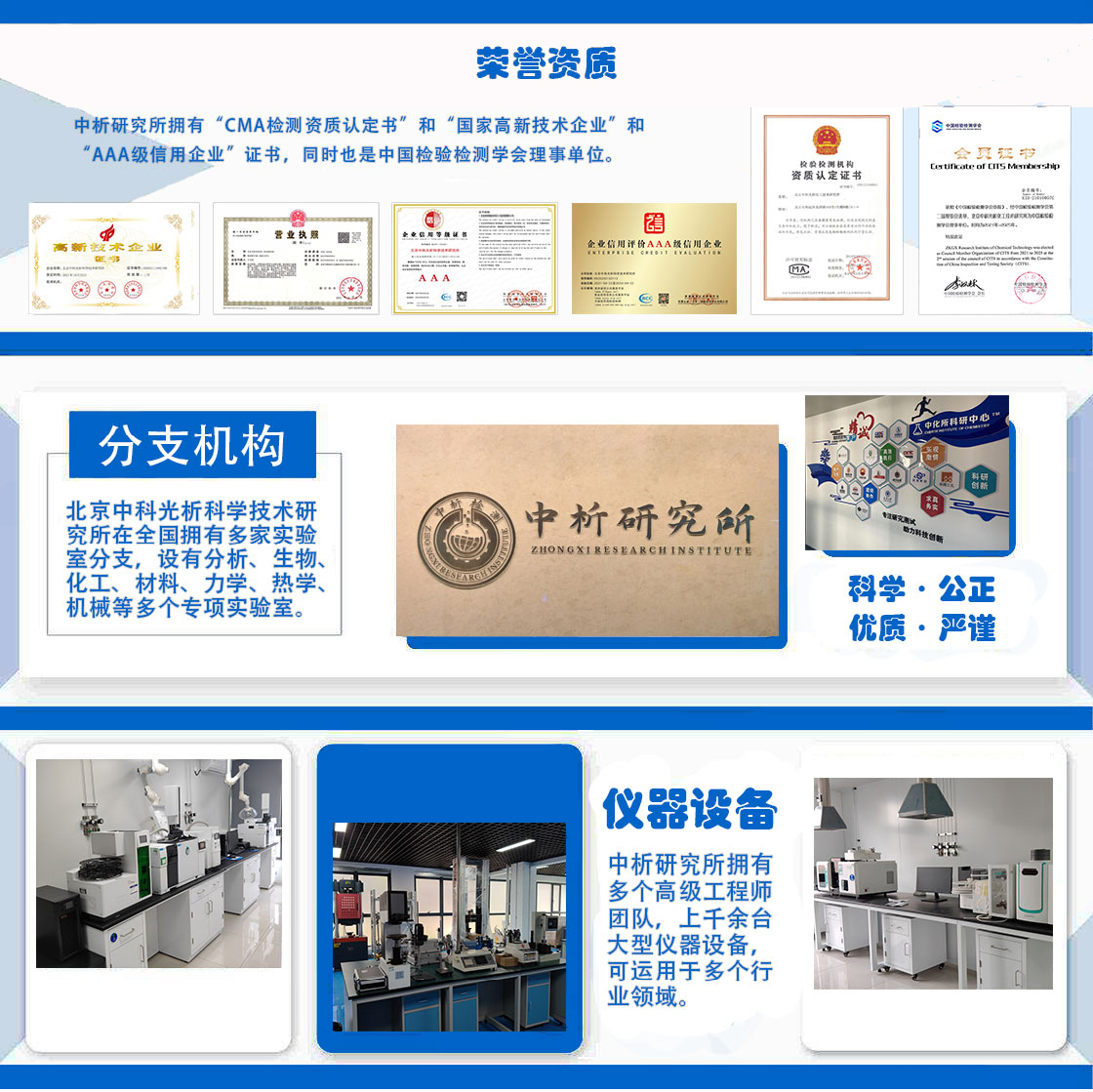
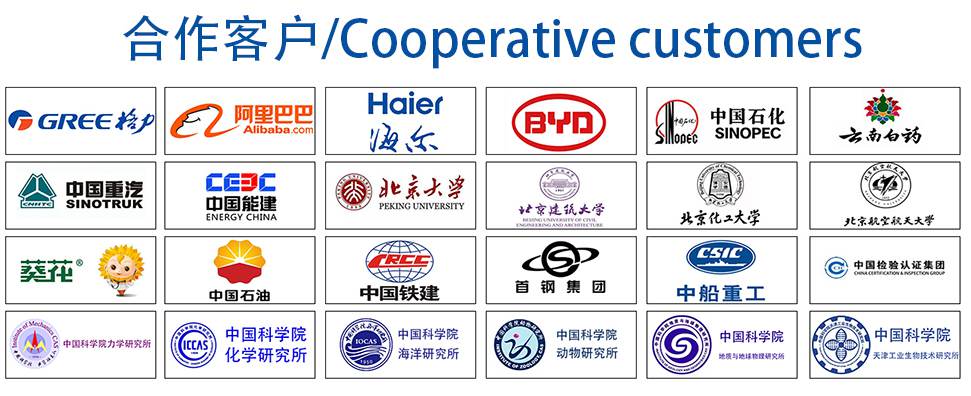