飞机刹车装置活塞止动机构的耐压试验检测
引言
飞机是一种复杂的航空器,其安全性直接关系到乘客和机组人员的生命安全。其中,刹车系统作为飞机至关重要的组成部分,负责控制飞机的滑行速度,特别是在着陆时起到关键作用。在刹车系统中,活塞止动机构作为核心组件之一,其性能的稳定性对于整个刹车系统的可靠性至关重要。因此,耐压试验检测成为评估飞机刹车装置活塞止动机构性能的重要环节。
活塞止动机构的功能与重要性
飞机刹车装置主要由多个部件组成,活塞止动机构在其中起到了限制和控制刹车活塞活动范围的作用。在刹车过程中,刹车活塞承受着巨大的压力,精准的定位和移动是确保刹车系统可靠运行的前提。止动机构的设计不仅要能够承受高压,还要具备耐腐蚀、耐磨损等特性,以确保长时间使用后的稳定性和安全性。因此,对止动机构进行耐压试验检测是确保其承受极端工况下正常运作的有效手段。
耐压试验检测的流程与方法
耐压试验检测旨在确定活塞止动机构在极端条件下的应力行为和耐受能力。常规的耐压试验检测方法包括静态压力试验、动态压力试验和疲劳试验等。其中,每种试验都有其独特的意义和目的。
静态压力试验
静态压力试验主要用于测试活塞止动机构在长时间静止状态下承受极限压力的情况。在进行静态压力试验时,采用专用测试设备对活塞止动机构逐步施加压力,直到达到预定的测试压力水平。通过监测活塞止动机构在不同压力条件下的变形量和应力分布,评估止动机构的结构完整性和材料性能。
动态压力试验
动态压力试验则模拟了活塞止动机构在实际工作环境下所承受的反复变化的压力负荷。通过施加周期性的压力波动,观察止动机构在长时间高频率负载下的响应能力,尤其是其疲劳强度和抗冲击性能。在动态试验中,止动机构需承受多次快速压力变化,而不会出现失效或变形。
疲劳试验
疲劳试验主要针对降解行为的检测,通过对活塞止动机构进行长期周期性压力施加,模仿其在实际运行中的工作条件,以评估其长久耐用性能。对于刹车系统这样的重要安全装置,了解其疲劳寿命至关重要,可有效预对潜在故障进行预判和防范。
影响耐压试验结果的因素
影响活塞止动机构耐压性能的因素有很多,其中材料、设计、加工工艺和维护保养等都发挥着重要作用。
材料选择
活塞止动机构的制造材料直接影响其耐压性能。耐磨损、耐腐蚀和高强度的材料能显著提升止动机构在极端压力下的表现。因此,在材料选择上需尤为慎重,通常选用合金钢、高强度铝合金或复合材料,以确保其适应航空器领域的严苛要求。
设计结构
止动机构的设计也对其耐压性能产生重大影响。良好的设计不仅需考虑到止动机构的功能适用性,还需确保其有足够的安全裕度来应对不同工况下的应力变化。设计中应充分考虑流体力学和结构力学因素,以优化受力和减少应力集中。
加工工艺
齐全的加工工艺是确保活塞止动机构高精度和高可靠性的基础。采用高难度精密加工技术,能够提高组件的整体性能,使其在耐压试验中表现出更优异的抗压能力及耐久性。
维护保养
定期维护保养可以有效延长活塞止动机构的使用寿命。在服役过程中,应常规检查止动机构是否存在磨损、腐蚀等异常情况,及时进行部件更换和维修,以避免因为疏忽而导致的重大安全隐患。
飞机刹车装置活塞止动机构的耐压试验检测是一项不可或缺的工作,通过全面的实验检测,可以有效发现其在高压条件下的弱点和潜在的故障隐患,进而提高飞机刹车系统的安全性能。未来,随着科技的发展,更齐全的材料和检测技术将被应用于耐压试验之中,以期进一步提升航空器的安全性能,实现更高效的空中交通管理和保证乘客的出行安全。
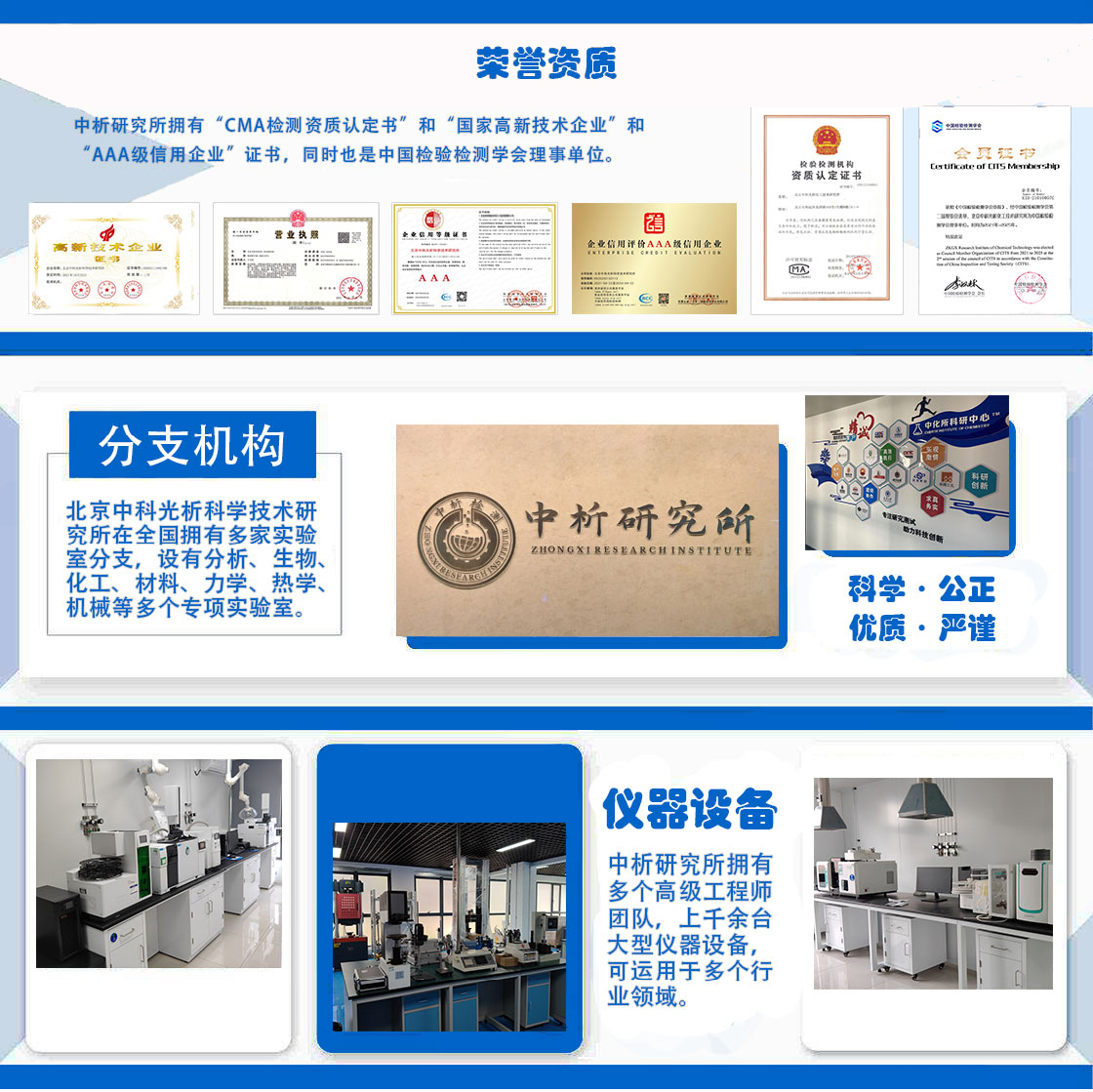
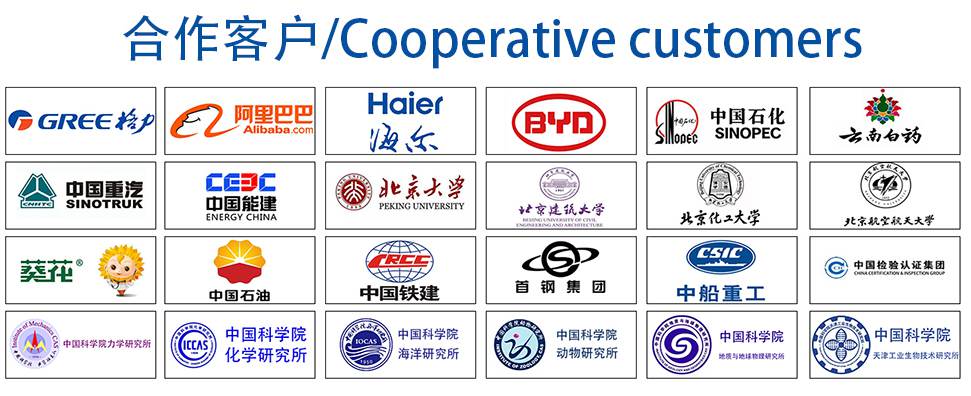