飞机刹车装置耐久性试验检测
飞机刹车装置耐久性试验检测
随着航空技术的快速发展,飞机作为现代交通运输最重要的工具之一,其安全性要求空前严格。而其中,飞机刹车装置不仅在着陆阶段中起到至关重要的作用,还直接关系到飞行安全、效率以及人员财产的保护。因此,对飞机刹车装置耐久性进行试验检测,是保证航空工业质量安全的重要环节之一。本文将详细探讨飞机刹车装置的耐久性试验检测的必要性、方法以及技术难点,并对未来的发展趋势进行展望。
刹车装置耐久性试验检测的必要性
飞机刹车系统是航空器制动系统中的关键技术之一,主要用于在飞机着陆后迅速降低速度,或者在滑行过程中避免越线、冲出跑道等危险情况。此外,在紧急情况下,该系统还肩负着使飞机迅速停止的职责,由此可见其在飞行安全体系中的重要地位。
刹车装置不仅需要承受频繁的启动停止,它还必须在极端环境下正常运作,如高温、低温、高湿或者砂石等恶劣污染条件。不仅如此,大型民航客机和高性能战斗机由于较高的着陆速度和重量,对于刹车系统的设计耐久性提出了更高的要求。因此,通过耐久性试验检测可以模拟实际工况,评估刹车装置的寿命和稳定性,确保其在整个设计周期内都能安全无误地运作。
耐久性试验检测的核心目标
刹车装置耐久性试验的目标主要包括以下几方面:
- 磨损评估:刹车系统主要部件如刹车片、盘刹等在长时间使用后会产生不同程度的磨损,耐久性试验需要模拟长期的使用状况评估其老化和失效风险。
- 热稳定性检测:着陆阶段的刹车会产生大量热能,试验需要测试刹车装置在高温状态下的表现,验证其热疲劳性能。
- 动态性能测试:在不同负载、不同速度下,刹车装置的制动力、反应速度和结构完整性是否能够保持稳定是测试的关键内容。
- 环境适应能力:试验还需要模拟高湿度、高温、低温、盐雾等恶劣环境,检测刹车装置能否应对不同飞行区域的多变气候。
耐久性试验的主要检测方法
1. 物理仿真试验
物理仿真试验是当前刹车装置耐久性检测中必不可缺的重要方法之一,试验装置模拟真实飞行中的着陆环节,包括降低速度、急停甚至冲击情况,利用测试平台对刹车系统的关键部件进行评估。
例如,通过高频刹车与放置休息的循环,让刹车片经历“冷启动”和“热循环”测试,观察其性能波动。此外,测试时还可以人为增加载荷或速度,来拓展部件的设计应用极限,找到性能下降的临界点。
2. 热语言监测测试
刹车过程中产生的热量是影响耐久性的一个重要因素,因此在试验中常采用热语言监测装置记录刹车盘表面的温度变化。这种监测技术允许工程师在实时测试中观察其热变化模式,并通过数据分析进一步揭示热疲劳对系统的影响。
3. 模拟环境实验
模拟环境测试室是检测刹车系统进行耐久性评价的重要工具。通过可控的室内环境再现飞机运行可能遭遇的极端情况,例如盐雾、高湿、极寒、沙土或者腐蚀等恶劣条件。通过长时间的系统运作来验证刹车装置是否在这些条件下保持稳定。
4. 软件仿真和电子监控
除物理实验外,现代航空技术也借助数字化手段对刹车装置进行模拟仿真。通过有限元分析(FEA)等仿真工具,可以快速建立并预测刹车装置在各种复杂工况下的使用寿命和故障发生模式。数据结合耐久性检测系统的传感器信息,还能方便地实现动态监控。
耐久性试验检测的挑战
尽管耐久性试验检测在航空工业中具备重大意义,但实际操作中也面临多重挑战:
首先,由于飞机使用的刹车装置多次经历巨大的动态负载,任何一个非预期因素都可能导致无法预测的结果。例如,在高温高压环境中,刹车系统材料可能出现裂纹,这种断裂特征在维护中可能不易发现,但一旦累积造成结构失效,会引发严重后果。
其次,试验环境要求极高,其耗费的时间长、精力多,甚至需要耗费整套飞机刹车成本来完成一个耐久性检测,长期累积的费用也是行业发展过程中需要克服的重要问题。
未来的发展方向
随着智能技术的推广与应用,飞机刹车装置耐久性试验检测也将步入新的发展阶段。未来可能实现试验时间的缩短和检测精度的大幅提升。例如,通过AI(人工智能)分析试验数据,快速标记潜在风险点;利用物联网技术实现试验联网共享,丰富各机构的研究资料库。
其次,新型材料的大量应用,也会为刹车装置提升耐久性提供更多选择。例如,由碳纤维增强复合材料制成的刹车片在强度、耐热性和摩擦性能方面远超传统金属材质,这将显著降低系统维护频率并延长使用寿命。
刹车装置的耐久性试验检测直接关系到飞机的安全性、效率以及使用寿命。通过科学合理的耐久性测试方法,可以全面评估其性能在不同飞行工况下的表现,从而为航空安全提供强有力的保障。尽管目前试验检测仍然面临诸多挑战,但随着技术的发展和新型材料的引入,未来刹车装置的耐久性检测技术将更加可靠,为航空器的安全飞行保驾护航。
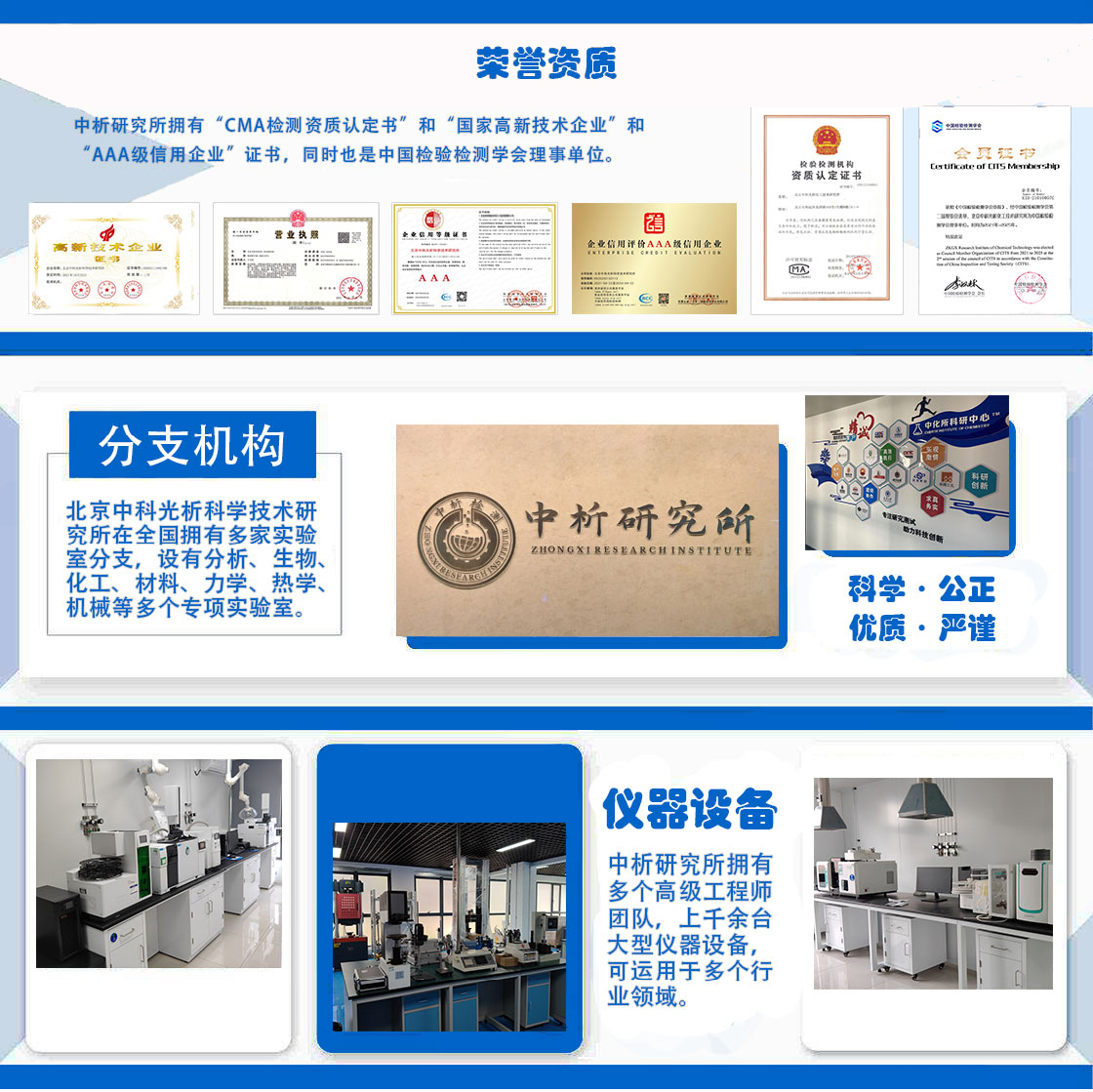
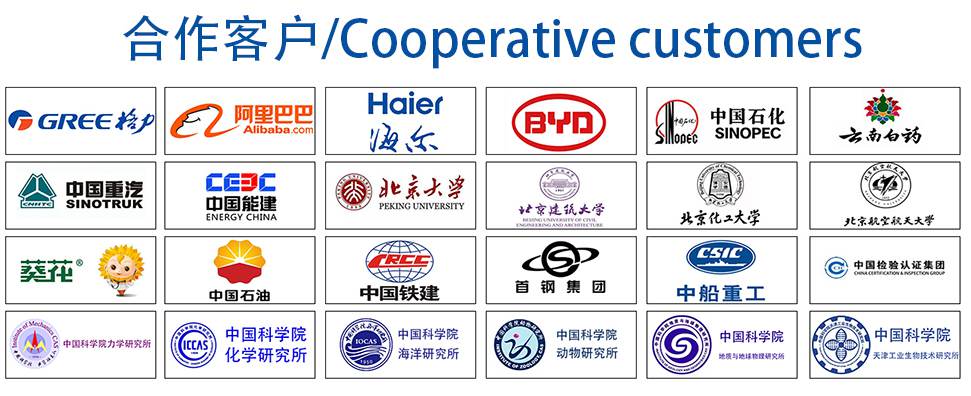