尾管悬挂器及尾管回接装置复合胶塞正向承压能力试验检测
尾管悬挂器及尾管回接装置复合胶塞的作用与重要性
在深井和超深井的开发中,尾管悬挂器及尾管回接装置是确保钻井安全与效率的重要设备。其核心任务是提升尾管的稳定性,防止意外的脱落或位移。而复合胶塞作为关键的承压元件,必须具备出色的正向承压能力,以应对地层复杂的压力环境。那么,为何正向承压能力如此重要?这直接关系到井下作业的安全性和生产效率。
测试正向承压能力的意义
尾管悬挂器及尾管回接装置的复合胶塞通常位于钻井系统的底部,承受着上层地层的巨大承压。这些装备需要在严苛的条件下保持稳定,即便面对极高的地层压力,复合胶塞也必须确保不泄漏、不松动。因此,进行正向承压能力的试验检测,不仅关系到设备本身的性能验收,更直接影响到整个钻井系统的安全性和长效性。
检测前的准备工作
在进行复合胶塞的正向承压能力检测前,首先需要进行充分的准备。包括选定合适的测试平台和检测设备、确认胶塞的规格与型号以及制定详细的测试方案。根据各地标高不同和地层结构的多样性,可通过数据模拟来设定不同的测试压力值,以保证测试结果的全面性和可靠性。
检测步骤与方法
具体的检测一般分为多个步骤进行。首先,将尾管悬挂器及复合胶塞安装到测试井中,然后逐步施加压力,模拟实际工况。在施加压力的过程中,需注意观察设备的密封性、稳定性以及是否有异常变形等情况。通过压力表与监测仪器的双重监控,实时记录测试中的关键参数,确保每一次数据采集的精确性。
考试参数与标准评估
在测试过程中,针对复合胶塞的不同型号和材质,设立一系列标准化的测试参数,如耐压能力、变形率及密封性能。根据国际及地区相关标准,如《石油天然气工业井下设备规范》,制定判断指标。若测试结果符合既定标准,即可判定为合格;若存在偏差,则需分析原因并进行设备的改进和优化。
面对挑战与解决方案
在检测过程中常遇到的挑战包括设备的老化、复合材料失效以及特殊地层引起的压力异常变化。解决这些问题常需要与多领域专家协作,包括材料科学家、工程师及地质专家,通过多领域知识的结合提供全面的解决方案。例如,在设备老化问题上,采用新型复合材料或技术进行更新升级;针对异常地层压力,则可以通过模拟软件进行压力变化推测,以提前做好应对方案。
检测后的调整与优化
经过正向承压能力的检测,若发现设备性能不符合标准,则需进行调整与优化。包括系统的重新设计、材料的选择改进以及安装调整等手段。持续的后期检测与改进可以保证设备在实际应用中稳健可靠,故而对于尾管悬挂器及尾管回接装置的正向承压能力的检测,应被视为一项长期策略采取。
检测对未来钻井产业的推动
随着科学技术的发展及油气资源的不断开采,深井和超深井的开发变得频繁,因此对尾管悬挂器及尾管回接装置的性能要求逐渐加高。通过严格的正向承压能力试验检测,不仅推动了设备性能的革新,也为未来复杂钻井技术的发展奠定了坚实的基础。这种实践和革新不仅使得产业链上的每一个环节受益,同时也促使相关标准和技术规范更趋完善。
总的来说,尾管悬挂器及尾管回接装置复合胶塞的正向承压能力试验检测是保障钻井安全与效率的必然手段。持续的试验、检测和改进,使得钻井工程在深井及更多极端工况下成为可能,并确保每一口井的开发和生产安全、可控。
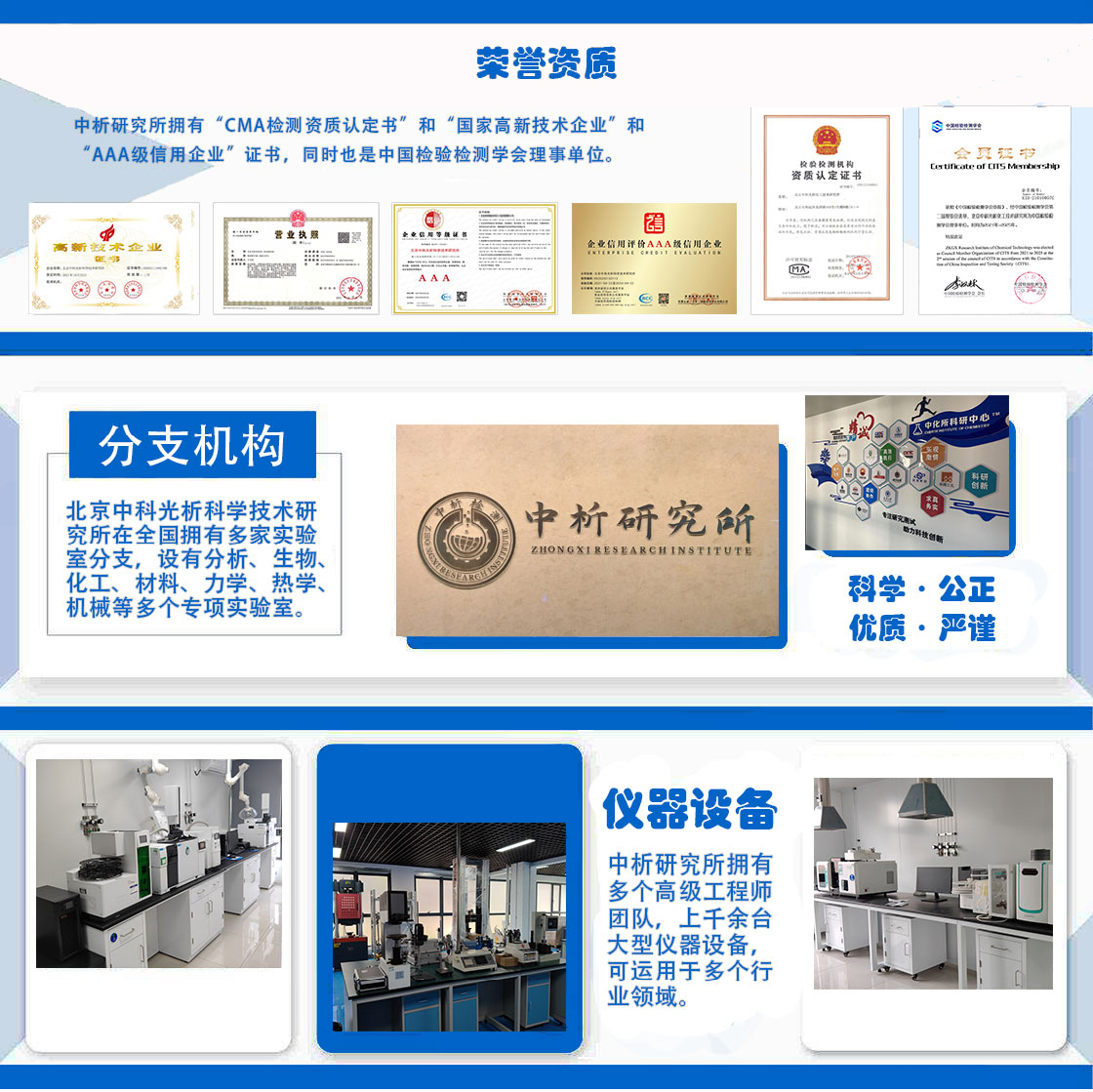
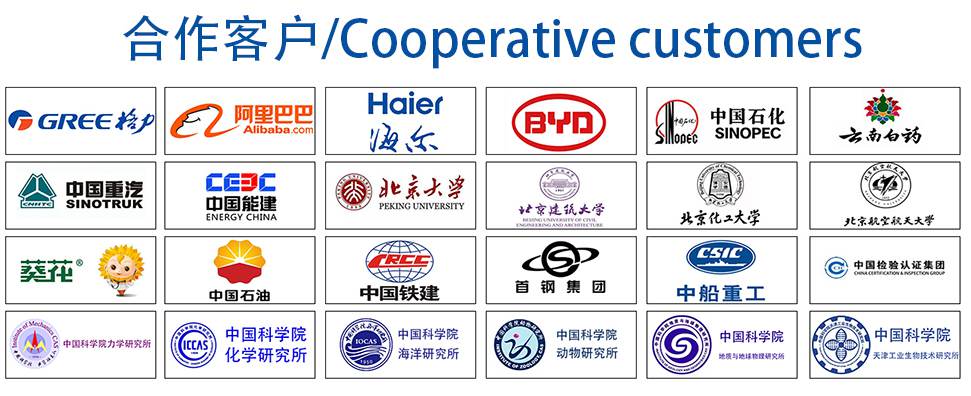