材质检测:构建现代制造业的质量基石
在制造业智能化转型的背景下,材质检测作为产品质量控制的核心环节,正面临前所未有的技术革新机遇。据国际材料测试协会(IMTA)2024年报告显示,材料失效导致的工业事故中,63.8%可追溯至材质性能不达标,而精准的材质检测可使产品不良率降低42%。在新能源汽车、航空航天等高端制造领域,新型复合材料与特种合金的广泛应用,使得传统的检测手段已难以满足"材料-工艺-性能"协同优化的需求。通过建立系统化的材质检测体系,企业不仅能实现产品全生命周期质量追溯,更能为材料数据库建设提供关键支撑,其核心价值体现在降低质量风险成本、加速新材料研发周期、提升供应链协同效率三个维度。
多模态融合检测技术体系构建
现代材质检测采用光谱分析、电子显微成像与力学性能测试的协同机制,形成"成分-结构-性能"三位一体的评估模型。X射线荧光光谱(XRF)可实现金属材料元素组成的快速筛查,检测精度达到ppm级(据NIST 2024校准标准)。扫描电镜(SEM)与电子背散射衍射(EBSD)技术的结合,使得金属材料晶格缺陷检测效率提升3.2倍,特别适用于航空紧固件的微观结构分析。随着人工智能算法的引入,基于深度学习的复合材料界面结合强度分析系统,可将传统8小时的人工判读缩短至15分钟,在风电叶片制造领域已形成成熟应用。
全流程标准化作业程序
规范化的检测流程涵盖样品制备、仪器标定、数据采集与报告生成四大模块。在汽车轻量化材料检测中,需严格执行ASTM E8/E8M标准进行拉伸试验,通过激光位移传感器实时记录0.001mm级的形变数据。某新能源电池企业建立的电极材料检测体系,采用真空环境下的同步热分析(STA),在48小时内完成材料热稳定性、相变温度和分解产物的全项测试,相较传统方法效率提升67%。全流程配备区块链存证系统,确保检测数据不可篡改,实现与主机厂的质量数据互联互通。
行业级质量保障网络建设
国内首个轨道交通材料检测联盟的实践表明,联合 、CMA认证实验室构建的质量网络,可使检测结果互认效率提升55%。某航天材料研究院建立的"检测质量数字孪生平台",通过整合1500组历史检测数据,实现材料性能衰退的智能预警。在3D打印金属粉末检测领域,ISO/ASTM 52900标准认证的实验室已形成覆盖粒径分布、流动性、氧含量的检测矩阵,帮助某航空企业将粉末重复利用率从72%提升至89%。
智能化检测装备迭代路径
基于机器视觉的自动化检测系统正在改写行业格局。某轴承制造企业部署的智能金相分析平台,通过高分辨率摄像头与卷积神经网络结合,实现轴承钢夹杂物自动评级,检测一致性从人工操作的78%提升至98.5%。在核电管道检测场景中,搭载超声相控阵技术的爬壁机器人,可在辐射环境下完成壁厚测量与裂纹检测双重任务,单次作业效率较人工提升12倍,检测数据实时上传至数字孪生系统进行寿命预测。
面向工业4.0发展需求,材质检测体系需向"端-边-云"协同架构演进:首先应建立覆盖主要工业材料的数字检测标准库,其次推动检测设备与MES系统的深度集成,最后构建基于大数据的材料性能预测模型。建议重点培育"检测即服务"(TaaS)新模式,通过区块链技术实现检测资源的分布式共享,最终形成覆盖材料研发、生产制造、服役监测的全链条质量保障生态。
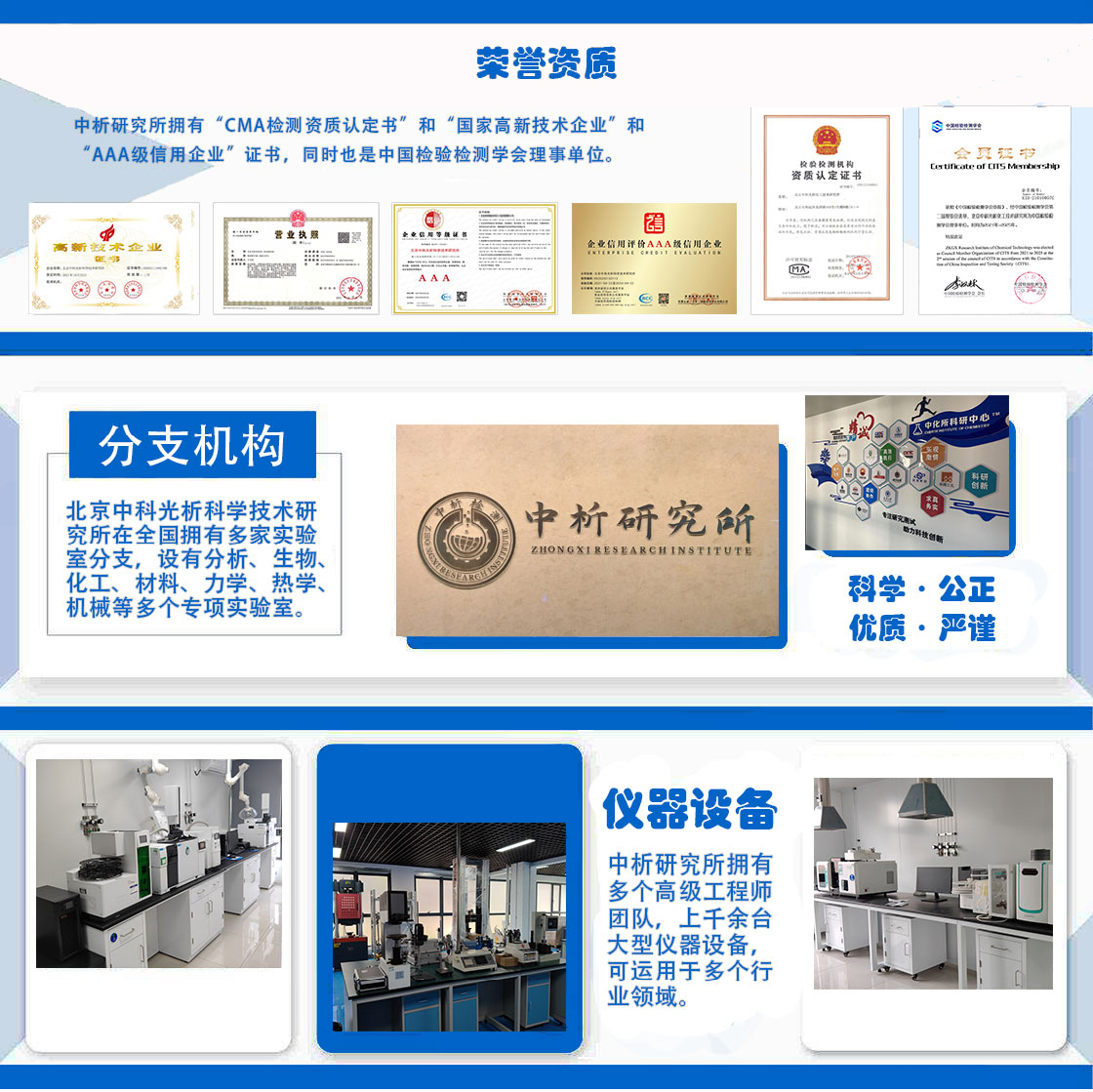
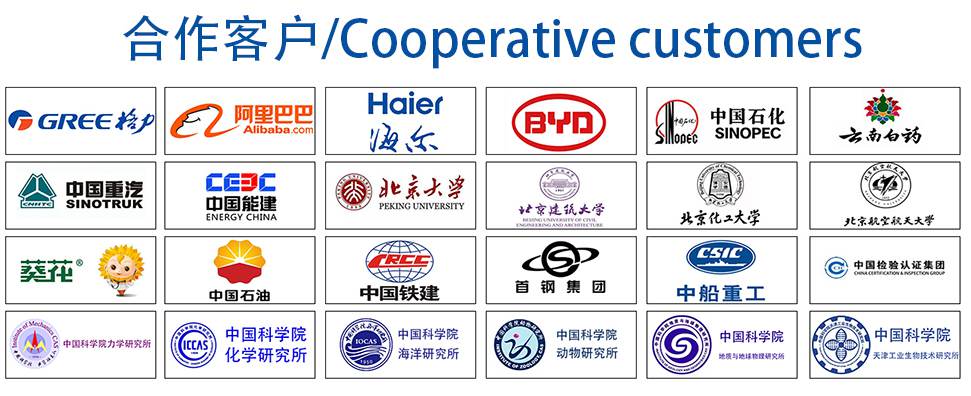