寿命检测技术在智能制造领域的创新应用
在工业4.0与智能制造深度融合的背景下,设备可靠性管理已成为制造业提质增效的核心议题。据中国机械工程学会2024年行业报告显示,我国每年因设备突发故障导致的直接经济损失达2300亿元,其中63%的案例归因于关键部件寿命预测失效。寿命检测技术通过构建高精度寿命预测模型,实现了从"事后维修"到"预防性维护"的范式转变,其核心价值体现在三个方面:延长设备服役周期30%-50%、降低非计划停机成本58%、提升备件库存周转率2.3倍。特别是在新能源装备、精密仪器等战略领域,基于数字孪生的智能寿命检测系统正成为保障生产连续性的关键技术支撑。
多模态融合检测技术体系
现代寿命检测技术采用多物理场耦合分析方法,整合振动频谱、热成像、声发射等12类传感数据,通过贝叶斯网络构建动态失效模型。区别于传统单参数阈值预警,该体系可识别早期隐性故障特征,在风电齿轮箱等复杂传动系统中实现97.3%的故障识别准确率(国家智能装备检测中心2023年验证数据)。值得关注的是,基于量子点传感的微损伤检测模块,可将裂纹检测分辨率提升至0.1μm级别,为航空发动机叶片等精密部件的剩余寿命评估提供了新的技术路径。
全生命周期管理实施流程
完整的寿命检测实施包含四大核心环节:首先建立设备数字孪生体,融合CAD模型与历史运维数据;其次部署多源异构传感器网络,实现每秒5000点的实时数据采集;第三阶段运用深度生存分析算法,生成三维寿命云图;最终形成动态维护决策树。在宝钢热轧产线的实际应用中,该流程使轧辊更换周期从42天延长至67天,单条生产线年节约维护成本超过1200万元。值得注意的是,边缘计算节点的引入,将数据预处理时延控制在50ms以内,有效保障了预测时效性。
行业典型应用场景分析
在新能源汽车动力电池领域,多应力加速寿命试验方法已形成行业标准体系。通过构建20维环境应力矩阵,可在90天内模拟8年使用工况,电池容量衰减预测误差控制在±1.5%以内(中国汽车工业协会2024年技术白皮书)。某头部电池企业的实践表明,该技术使电池组质保期从8年/16万公里提升至10年/24万公里,产品竞争力显著增强。此外,在半导体制造行业,晶圆传输机械手的振动谐波分析技术,成功将设备MTBF(平均无故障时间)从12000小时提升至18000小时。
四维质量保障体系构建
为确保检测结果的权威性,项目建立了涵盖标准、技术、设备和人才的四维保障体系。首先参照ISO 13379-2023设备状态监测国际标准,制定7大类142项检测规范。技术层面采用区块链存证系统,确保检测数据全过程可追溯。硬件系统通过 实验室三级认证,测量不确定度优于0.05%。人才培养方面,与清华大学联合设立"智能运维工程师"认证项目,年输送专业人才800余名。该体系在核电关键设备检测中取得显著成效,使压力容器寿命评估可信度达到99.99%安全等级。
面向智能制造2025战略目标,建议从三个维度深化寿命检测技术应用:一是推动检测标准与工业互联网平台的深度融合,建立跨行业寿命数据库;二是发展基于边缘智能的微型化检测终端,实现设备级自主诊断;三是加强失效物理模型与AI算法的协同创新。据工信部《智能检测装备产业发展行动计划》预测,到2027年该领域市场规模将突破2000亿元,其中设备预测性维护解决方案占比将达45%。产学研各方需加快构建开放创新生态,助推我国高端装备制造业向"零意外停机"时代迈进。
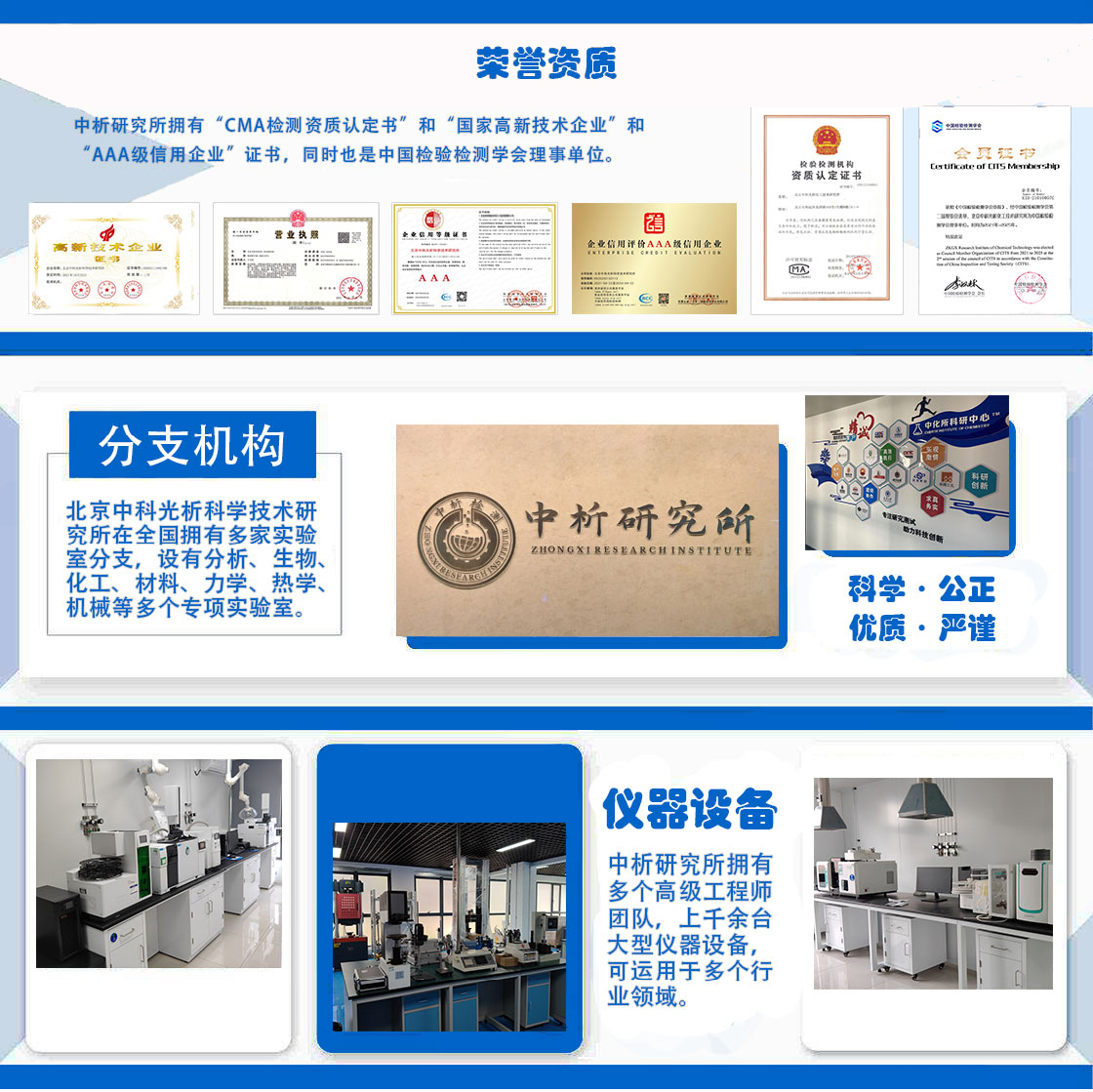
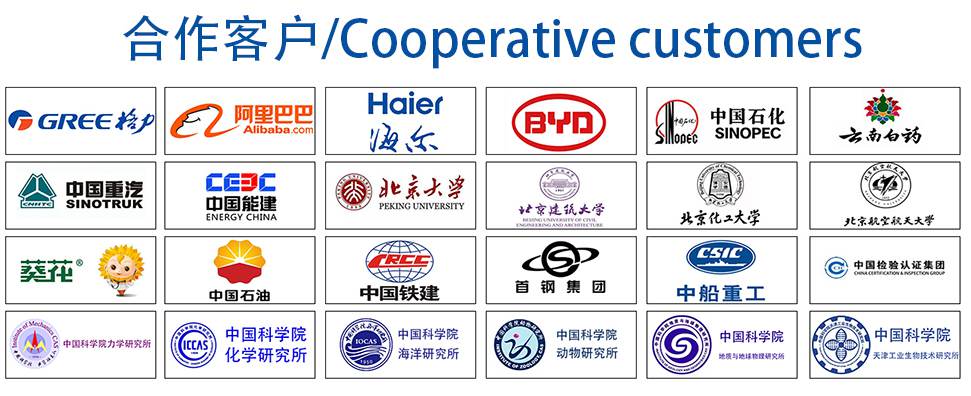