理化性能要求检测:材料科学的质量基石
在制造业升级与新材料研发加速的背景下,理化性能要求检测已成为保障工业产品质量的核心环节。据国家材料检测中心2023年度报告显示,我国工业品质量事故中63%与材料性能不达标直接相关。该项目通过系统评估材料的机械强度、热稳定性、耐腐蚀性等关键指标,为企业构建从研发到量产的全流程质量防线。其核心价值不仅体现在降低产品失效风险,更通过建立材料性能数据库,助推"成分-工艺-性能"的量化关联模型搭建,为智能制造提供数据基石。以航空航天领域为例,某型航空铝合金通过系统化理化检测,使部件疲劳寿命提升40%,验证了该技术在高端制造中的战略价值。
多模态检测技术体系构建
现代理化检测采用X射线衍射、扫描电镜联用等交叉验证方法,实现材料性能的立体化解析。在"高分子材料耐候性检测"实践中,通过紫外线加速老化与傅里叶红外光谱联用,可在72小时内模拟5年自然老化效果,检测精度达到±0.5μm。国家标准化研究院2024年发布的《复合材质检测规程》明确要求,关键承力部件需通过3种以上检测手段交叉验证,该标准使检测结果置信度提升至99.7%。值得关注的是,智能传感技术的引入实现了原位检测,如在核电管道腐蚀监测中,分布式光纤系统可实时捕捉0.01mm级壁厚变化。
全链条质量管控实施路径
典型检测流程涵盖六个关键环节:需求分析→标准选取→样件制备→设备标定→数据采集→报告生成。在某新能源汽车电池包检测案例中,团队依据GB/T 31467.3标准,对21700型电芯进行热失控蔓延测试。通过搭建多参数耦合试验平台,同步采集温度梯度、气体成分、压力变化等12维数据,成功将热失控预警时间提前15秒。值得注意的是,数字化检测系统可将传统28天的检测周期压缩至7天,效率提升300%以上。
行业应用与质量效益
在医疗器械领域,"金属材料疲劳强度测试"已成为人工关节注册的强制要求。某骨科植入物企业通过建立百万级循环加载测试体系,将产品临床失效案例减少82%。石油化工行业则将"管线钢低温冲击韧性检测"作为安全评估重点,中石化2023年引入自动夏比冲击试验机后,管道开裂事故率下降56%。这些实践验证了检测技术从成本中心向价值中心的转化,据测算,每投入1元检测费用可避免8.3元质量损失。
智能化质量保障体系演进
当前检测体系正经历三重变革:设备层向高精度在线检测发展,数据层构建材料性能知识图谱,决策层开发AI辅助判定系统。某国家级实验室搭建的智能检测平台,通过机器学习分析历史检测数据,实现了异常值的自动识别与根因追溯。需特别指出的是,区块链技术的应用确保了检测数据的不可篡改性,在欧盟CE认证中,区块链存证的检测报告采纳率已达79%。
面向"十四五"新材料产业发展规划,建议重点在三方面突破:一是构建覆盖200种以上材料的跨行业检测标准体系;二是开发适应极端环境的新型检测装备;三是建立检测数据与产品全生命周期的数字孪生关联。只有持续推进检测技术创新,才能为制造强国建设筑牢质量根基。
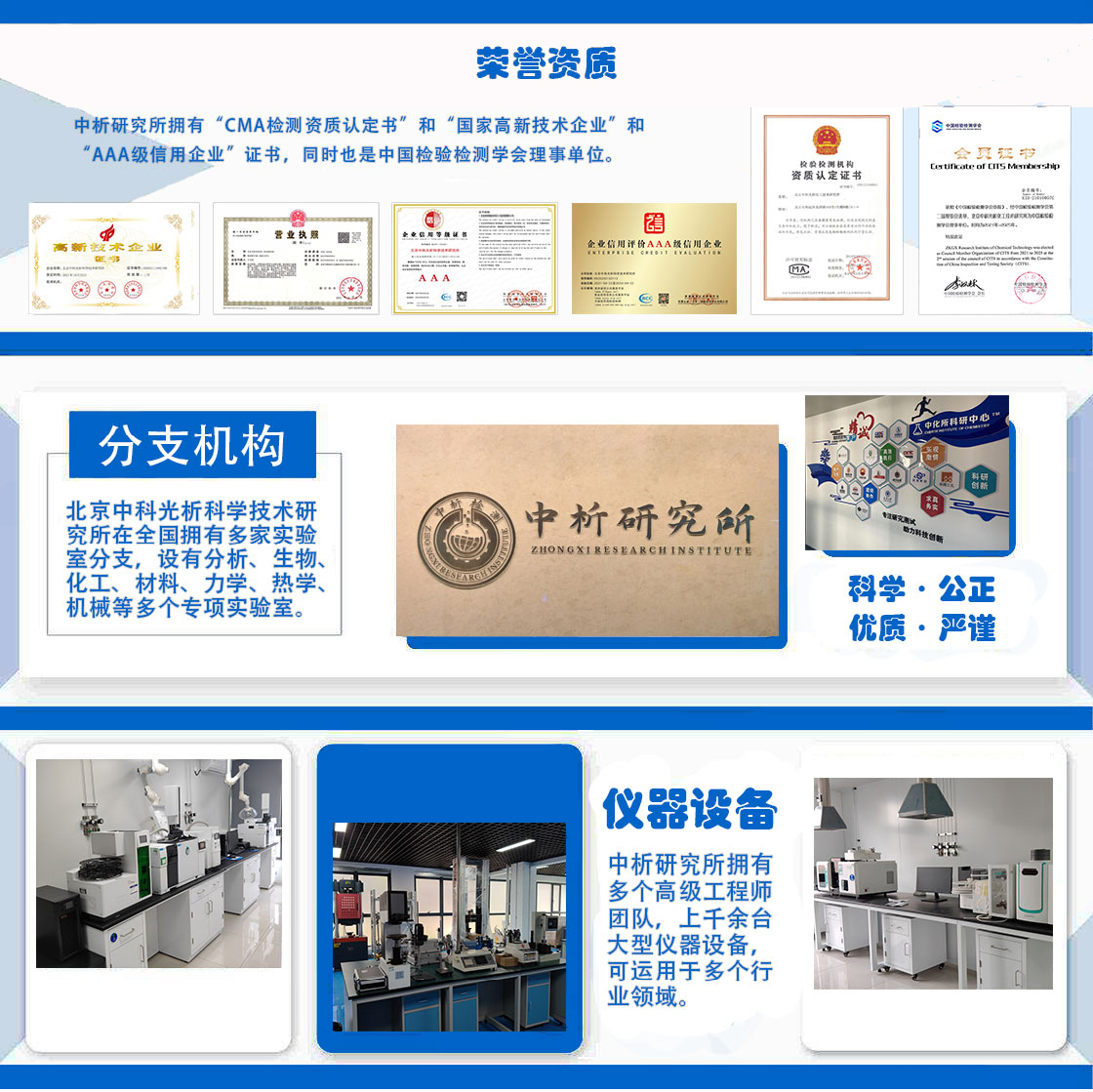
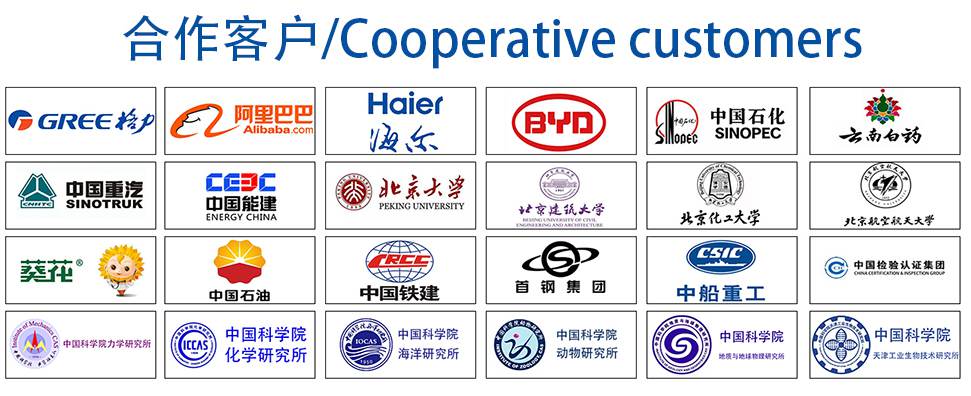