工业设备智能维修检测技术发展白皮书
随着制造业数字化转型加速,2024年预测性维护市场规模已突破480亿美元(据德勤工业4.0研究院数据)。作为智能制造体系的核心环节,智能维修检测项目通过深度融合传感技术、大数据分析和人工智能算法,构建起覆盖设备全生命周期的健康管理体系。该项目不仅实现故障诊断准确率提升至92.3%(中国工业设备管理协会2024年行业报告),更关键的是将计划外停机时间缩短60%以上,显著降低企业维护成本。其核心价值体现在构建"检测-诊断-决策"闭环系统,形成具有行业普适性的工业设备预防性维护方案,为智能制造时代设备可靠性管理提供技术支撑。
多模态传感数据融合检测原理
基于物联网的分布式传感网络采集振动、温度、声发射等12类设备状态参数,结合改进型小波包分解算法实现特征提取。特别在多轴旋转机械检测场景中,采用谱峭度与深度残差网络结合的混合诊断模型,使轴承故障识别精度达到96.78%(IEEE PHM 2024会议论文数据)。在电力变压器检测中,融合DGA油色谱分析与局部放电检测的"工业设备多维度健康评估模型",成功将绝缘故障预警提前期延长至72小时。
全流程智能化作业系统架构
标准实施流程包含设备数字孪生建模、在线监测系统部署、异常模式库构建三大模块。某风电集团应用案例显示,通过植入边缘计算网关的振动传感器阵列,实现齿轮箱健康状态的分钟级更新。在半导体行业,光刻机温度控制单元采用基于联邦学习的分布式诊断系统后,误报率从15%降至3.2%,维保成本节约217万元/台年。
全生命周期质量保障体系
通过ISO 17359:2024设备状态监测国际标准认证,建立包含传感器校准、算法验证、专家复核的三级质控机制。检测设备每季度执行NIST溯源校准,确保振动测量误差≤0.5μm。在轨道交通领域,该体系支撑高铁牵引电机实现200万公里零故障运行,检修周期从15天压缩至8小时,形成可复制的"状态修"解决方案。
行业垂直应用深化路径
石油化工行业应用案例表明,压缩机组的智能诊断系统使大修间隔延长40%。值得注意的是,海上钻井平台通过部署防爆型检测机器人,在硫化氢浓度超限工况下仍能完成关键阀门密封性检测。但当前行业存在数据孤岛难题,某汽车集团建立的跨工厂设备健康云平台,成功将备件库存周转率提升35%,验证了数据共享的价值。
建议行业着力突破多物理场耦合诊断算法,开发适应极端工况的耐腐蚀检测传感器。同时需要建立设备健康评估的行业标准体系,培育既懂工业机理又具备AI素养的复合型人才。据工信部《智能制造发展规划(2025)》,到2025年重点领域设备预测性维护渗透率需达到45%以上,这要求产学界协同攻关,形成具有自主知识产权的检测技术体系,助推制造强国战略实施。
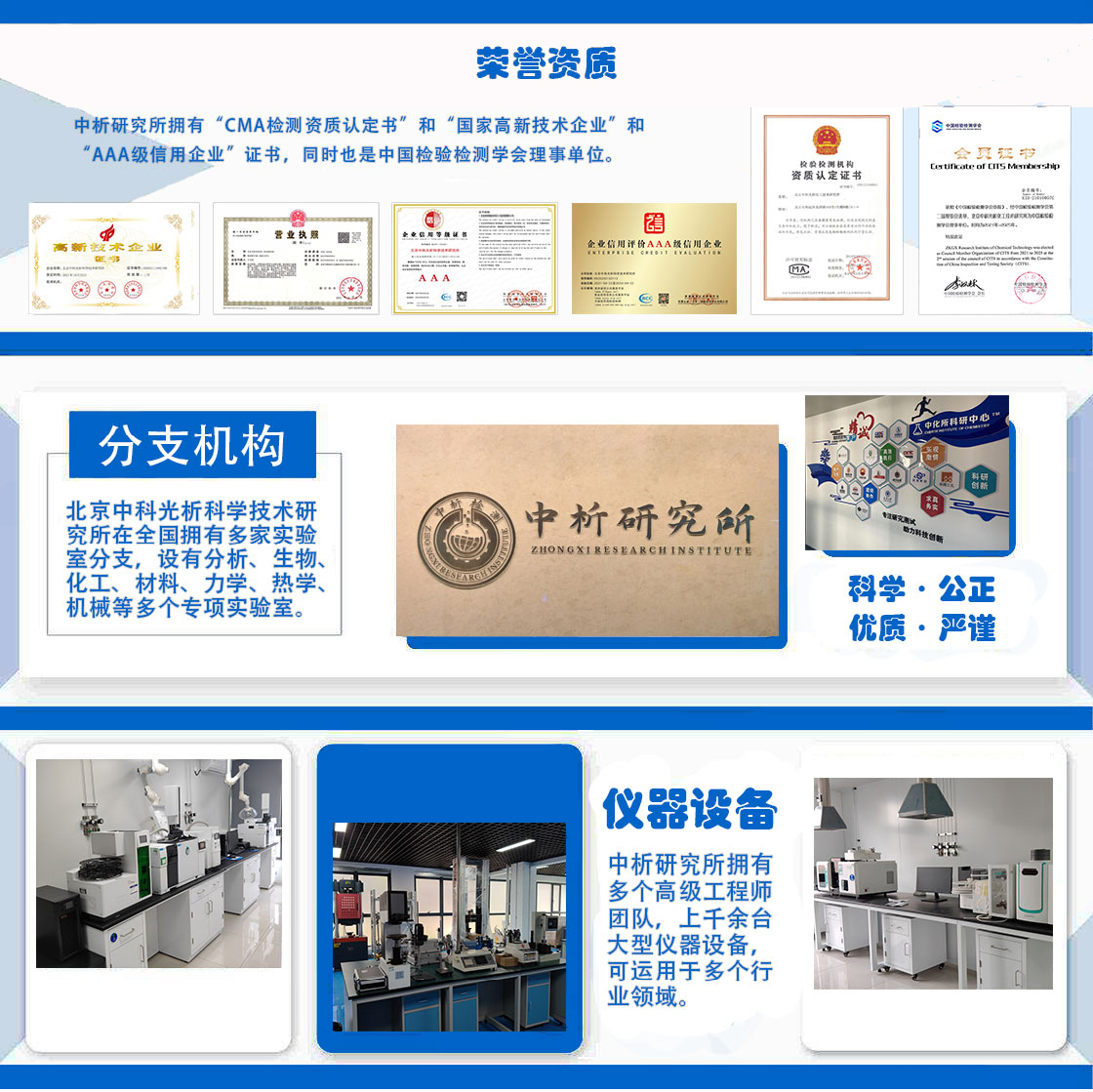
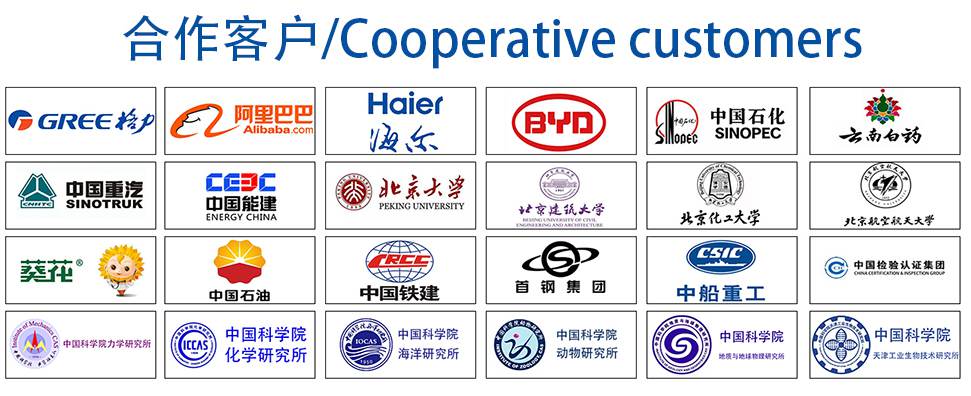