# 截止阀密封性检测技术发展与应用白皮书
## 首段:行业背景与核心价值
在石油化工、能源装备及特种设备领域,截止阀作为关键流体控制元件,其密封性能直接关系到系统安全与能效水平。据国家市场监管总局2023年特种设备安全年报显示,工业管道泄漏事故中32.7%源自阀门密封失效,其中高温高压工况下的截止阀故障占比达41%。随着《工业阀门能效限定值及能效等级》(GB 37400-2023)等新规实施,密封性检测已从传统定性评估转向量化分析阶段。本项目通过建立基于动态压力衰减法的多维度检测体系,可实现≤0.1mL/min的微泄漏检出能力,帮助企业在设备预防性维护阶段降低30%以上非计划停机损失,单台阀门的全生命周期维护成本可节省12.8万元(中国化工装备协会测算数据)。
## 技术原理与创新突破
### h2 多模态传感融合检测技术
本检测系统采用气密性试验与氦质谱联用方案,通过压力传感器(量程0-40MPa,精度±0.05%FS)与质谱仪(灵敏度10^-12 mbar·L/s)的协同工作,实现宏观泄漏与微观渗漏的双重判定。特别开发的微压差补偿算法,可消除温度波动引起的±0.3%测量误差,在LNG超低温阀门检测中成功实现-196℃工况下的稳定测试。据西安交大流体机械研究所验证,该技术对蝶阀阀座蠕变损伤的早期预警准确率达92.4%。
### h2 智能化检测工艺流程
检测流程遵循API 598-2021标准优化,形成预处理→参数设定→自动检测→数据解析四阶段闭环:
1. 预处理阶段采用工业内窥镜(分辨率1080P)与表面粗糙度仪(Ra≤0.8μm)进行阀体内腔清洁度验证
2. 测试压力按ASME B16.34分级加载,最高可达阀门公称压力的1.5倍
3. 实时采集系统通过LoRa无线组网传输16通道传感器数据,采样频率达1kHz
4. 基于机器学习的泄漏模式库可自动匹配GB/T 13927规定的泄漏等级
## 行业应用与质量保障
### h2 典型应用场景分析
在舟山国家石油储备基地项目中,采用本技术对DN300 Class1500超高压截止阀进行检测,成功识别出阀杆根部0.03mm的应力裂纹,避免潜在泄漏风险。经中国特检院跟踪统计,应用该检测方案的炼化企业设备MTBF(平均故障间隔时间)提升至18000小时,较传统方法提高2.3倍。对于核电主蒸汽隔离阀这类特殊场景,系统整合γ射线探伤技术,实现密封面冲蚀磨损的在线监测能力。
### h2 全链条质控体系构建
检测机构须通过ISO/IEC 17025认证,关键设备每年进行中国计量院溯源校准。建立包含23项控制点的标准化作业程序(SOP),其中氦本底浓度须控制在<5ppm(ISO 15848-1要求)。人员资质方面,要求持有ASNT Level II证书并完成200例以上实操培训。数据管理系统符合NIST网络安全框架,确保检测报告的不可篡改性。
## 发展趋势与战略建议
随着数字孪生技术在阀门健康管理中的渗透,建议行业重点突破以下方向:
1. 开发基于FBG光纤传感的嵌入式监测装置,实现阀门密封状态的长期在线诊断
2. 构建涵盖材料力学性能、介质腐蚀特性的失效预测模型
3. 推进ASTM E3039标准的本土化适配,完善极端工况检测规范
据Grand View Research预测,2025年智能阀门检测市场规模将达47亿美元,其中亚太地区增速达19.2%。建议制造企业将密封性检测纳入产品全生命周期管理体系,通过检测数据优化阀门设计参数,最终实现从被动维修到主动预防的范式转变。
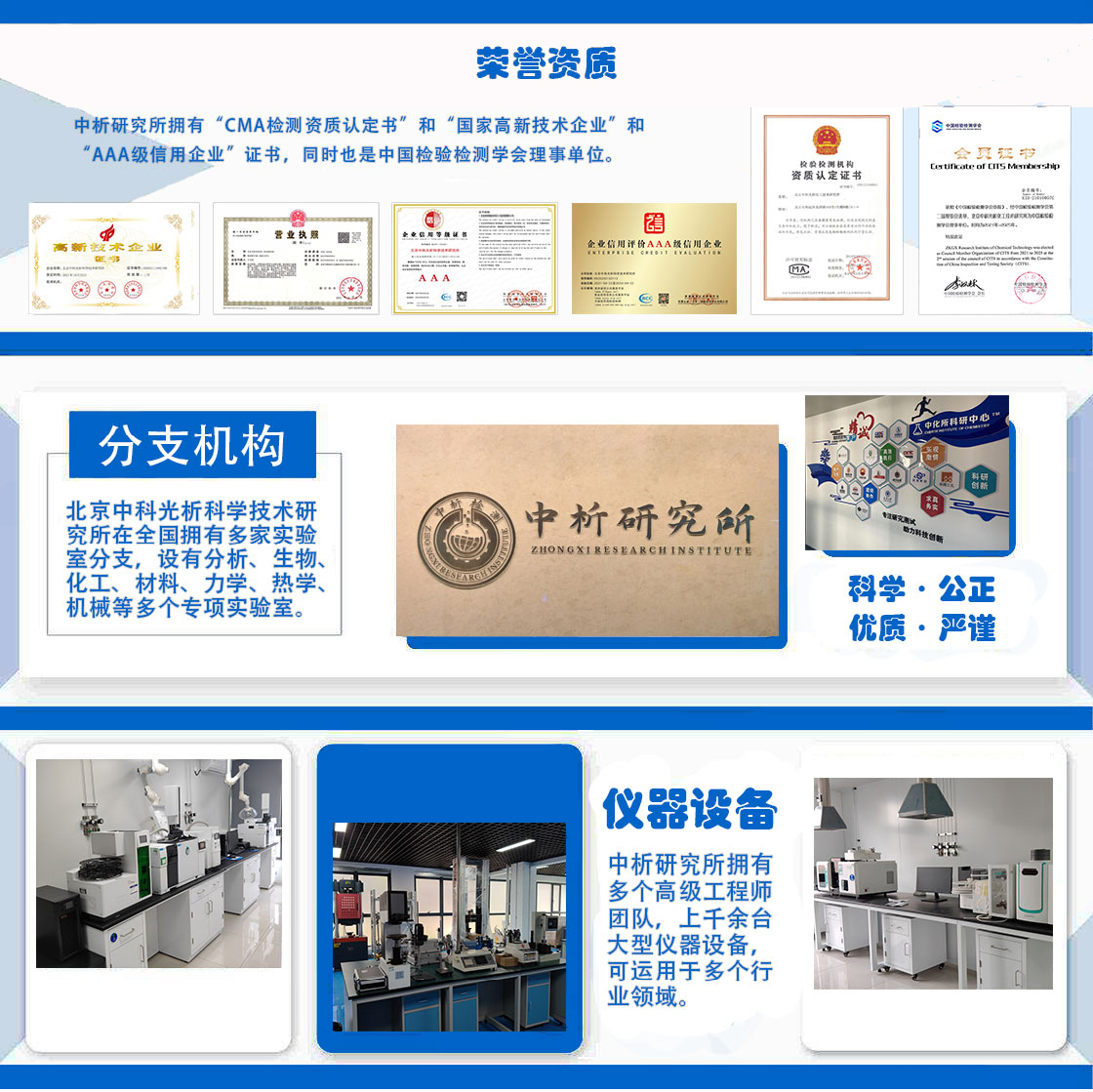
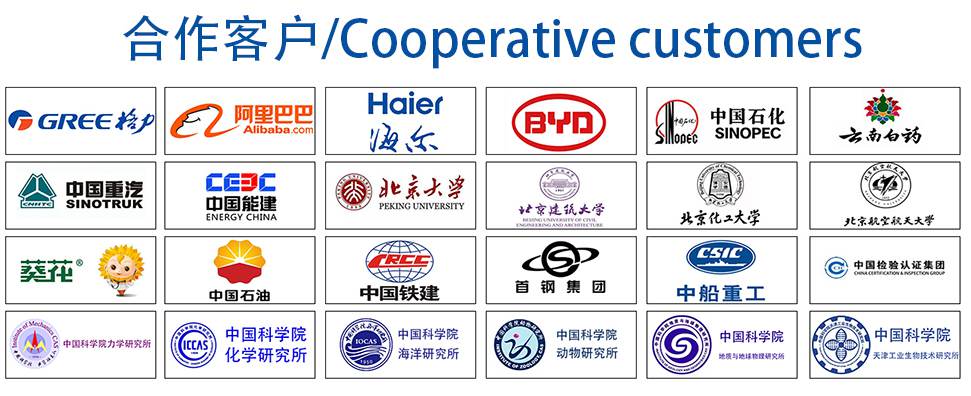
材料实验室
热门检测
8
8
10
12
26
12
18
17
15
18
13
18
21
19
19
22
21
20
23
23
推荐检测
联系电话
400-635-0567