蒸汽加热性能测试检测:工业能效优化的关键技术路径
在碳中和目标驱动下,工业领域热力系统能效管理已成为性课题。据中国能效管理研究院2024年数据显示,我国工业蒸汽系统平均能效转换率仅68.3%,低于发达国家8-12个百分点,每年导致能源浪费达2400万吨标煤。蒸汽加热性能测试检测作为热力系统优化的核心手段,通过量化评估蒸汽设备的热传导效率、温度均匀性及能源利用率,为工艺流程改进提供数据支撑。该检测项目不仅可降低企业5-15%的能源成本,更通过预防性维护减少设备故障率30%以上,在食品杀菌、化工反应釜温控等场景中展现突出价值,被列入《国家工业节能技术装备推荐目录(2025年版)》重点推广技术。
热力学耦合分析的技术原理
蒸汽加热性能测试基于热力学第一定律和第二定律构建能量平衡模型,采用分布式温度传感网络实时采集蒸汽流量、压力、干度等12项关键参数。通过计算有效热传递系数(ETC)和熵产率,可精准识别系统薄弱环节。例如在乳制品UHT杀菌工艺中,设备表面热损失每降低1%可提升0.8%的能源利用率。业内领先的"工业蒸汽系统能效优化方案"已实现±0.5℃的温度控制精度,满足FDA对热敏性物料加工的温度波动要求。
全流程标准化实施体系
测试流程涵盖三个阶段:预处理阶段完成设备气密性检测与传感器布点,采用激光多普勒测速仪验证蒸汽流速分布;实测阶段通过多工况模拟获取动态传热曲线,结合ASTM E457标准进行冷凝水回收率测算;数据分析阶段运用机器学习算法建立设备能效数字孪生模型。某石化企业应用该体系后,成功将重整装置加热器效率从71%提升至83%,年节约蒸汽费用超1200万元。
多行业应用实证
在制药行业冻干机验证中,蒸汽加热性能测试帮助某生物制药企业将箱体温度均匀性从±2.5℃优化至±0.8℃,产品含水率合格率提升12%。国家工业节能中心案例库显示,采用"蒸汽加热设备热传导效率分析"技术的食品企业,灭菌能耗降低20%的同时,生产效率提高15%。更值得关注的是,某造纸厂通过检测发现疏水阀故障导致的年蒸汽浪费达4800吨,经改造后实现能源成本骤降18%。
三层质量保障机制
检测体系建立ISO/IEC 17025质量管理系统,核心设备每季度进行NIST溯源校准。现场测试采用冗余传感器布置方案,关键数据采集实现三重校验。人员资质方面要求检测工程师同时具备ASME PTC 4.1认证和压力容器操作资格。某第三方检测机构统计表明,该机制使测试报告数据置信度达99.7%,重复测试偏差控制在1.2%以内。
展望未来,建议行业建立蒸汽加热系统动态能效数据库,开发基于数字孪生的预测性维护平台。据国家智能制造推进联盟预测,融合5G传输和AI诊断的智能检测系统,可使设备能效管理响应速度提升40%。企业应重点关注蒸汽余热梯级利用技术,探索将检测数据与碳核算体系对接,为构建零碳工厂提供技术支点。
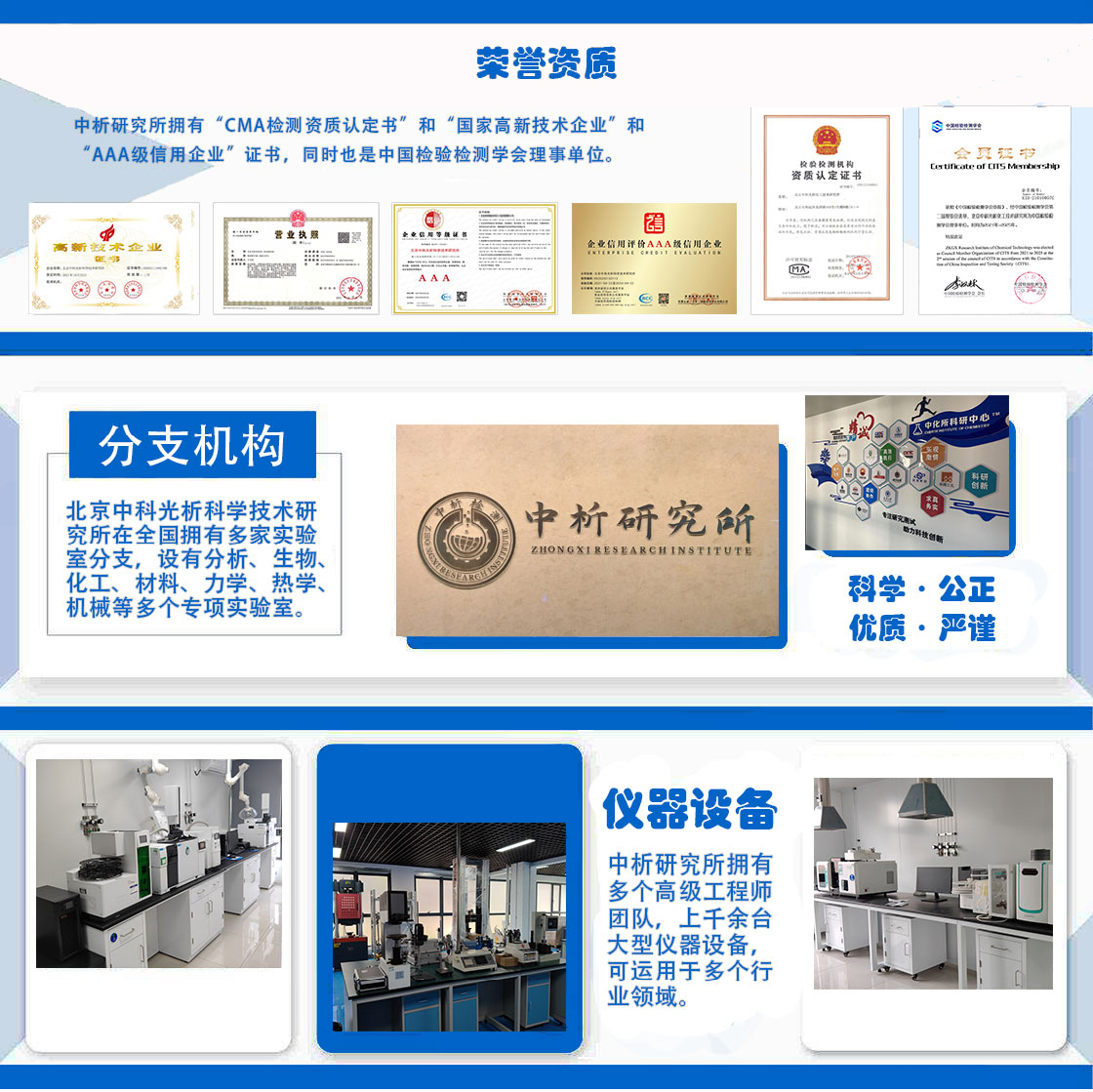
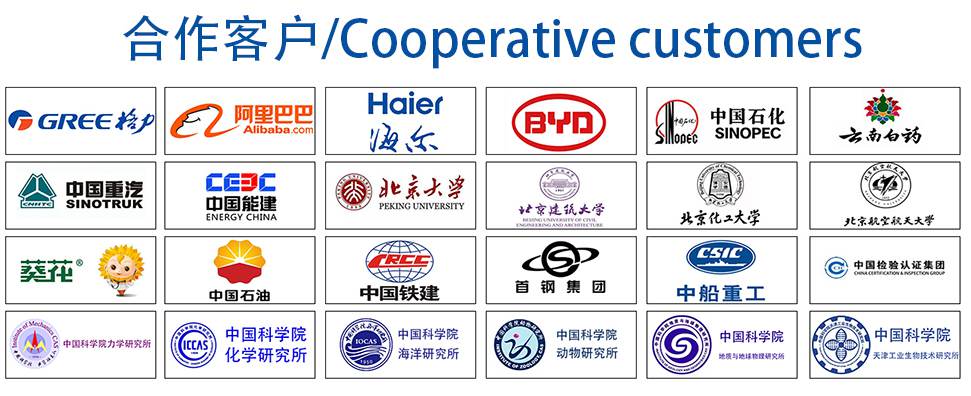