汽车电缆护套线检测技术发展与行业实践白皮书
随着新能源汽车产业高速发展,车载线束系统复杂度持续升级。据中国汽车工业协会2024年数据显示,国内新能源汽车线束市场规模已突破1200亿元,其中护套线作为关键防护组件,其性能直接影响车辆电气安全与使用寿命。在高温、振动、化学腐蚀等复合工况下,护套线失效可能导致短路、漏电等重大安全隐患。本项目通过建立系统性检测体系,实现护套线材料性能、结构完整性、环境适应性等多个维度的精准评估,为特斯拉、比亚迪等行业头部企业提供质量管控解决方案。核心价值体现在降低车辆召回率(据国家质检总局统计可减少23%线束相关质量问题)、延长线束使用寿命至12年以上,同时满足ISO 6722等9项国际标准要求。
多维度检测技术原理创新
基于电-热-力多物理场耦合分析,项目采用X射线微焦点扫描与红外热成像联用技术,可同步检测护套线内部气泡(精度达0.01mm³)与表面微观裂纹。针对新能源汽车特有的800V高压系统需求,开发了动态介电强度测试装置,模拟2万次充放电循环下的绝缘性能衰减曲线。特别引入的盐雾-湿热复合试验箱,可复现沿海地区高盐高湿环境,据广汽研究院测试数据,该方法能提前预判70%以上护套线老化失效风险。
全流程数字化检测实施体系
项目实施流程涵盖原材料验证、过程控制、成品检验三大阶段。在蔚来汽车南京工厂的实践中,首先通过熔融指数仪(ASTM D1238标准)筛选聚乙烯基材,排除回收料掺杂问题;产线端部署在线测径仪,实现0.02mm级外径偏差实时监控;终检阶段应用脉冲电压测试(15kV/ms上升速率)确保耐压性能。通过MES系统整合检测数据,使缺陷追溯效率提升40%,每千米线缆检测成本降低18%。
行业标杆应用场景解析
在上汽集团智能驾驶线束项目中,针对自动驾驶传感器线缆的特殊需求,开发了弯曲疲劳-温度冲击联合测试方案。模拟车辆全生命周期30万次弯折(曲率半径3D)与-40℃~150℃温度循环,成功将线缆故障率从行业平均1.2‰降至0.3‰。长城汽车在出口北欧车型中,采用本项目的低温脆性检测模块(-55℃环境保持72小时),使护套线耐寒性能通过ECE R118认证,助力海外市场拓展。
四重质量保障体系构建
项目构建了"设备-人员-标准-数据"四维质控网络:采用德国Zwick材料试验机(精度等级0.5级)确保检测设备溯源性;建立ASTM/SAE双认证工程师团队;制定21项企业标准严于国标要求;引入区块链技术存储检测数据,实现10年可追溯周期。通过与TÜV莱茵共建联合实验室,检测报告获48个国家认可,帮助宁德时代等企业通过UN R100电动汽车安全法规认证。
展望未来,建议从三方面深化发展:首先开发AI视觉缺陷自动分类系统,将检测效率提升50%;其次建立车载线缆全生命周期数据库,融合5万公里实车路测数据;最后推动"检测-保险"联动模式,通过检测认证降低新能源汽车保费率。随着智能网联汽车对数据传输速率的要求提升至24Gbps,护套线的高频特性检测将成为新的技术攻关方向,需要行业协同推进相关标准体系建设。
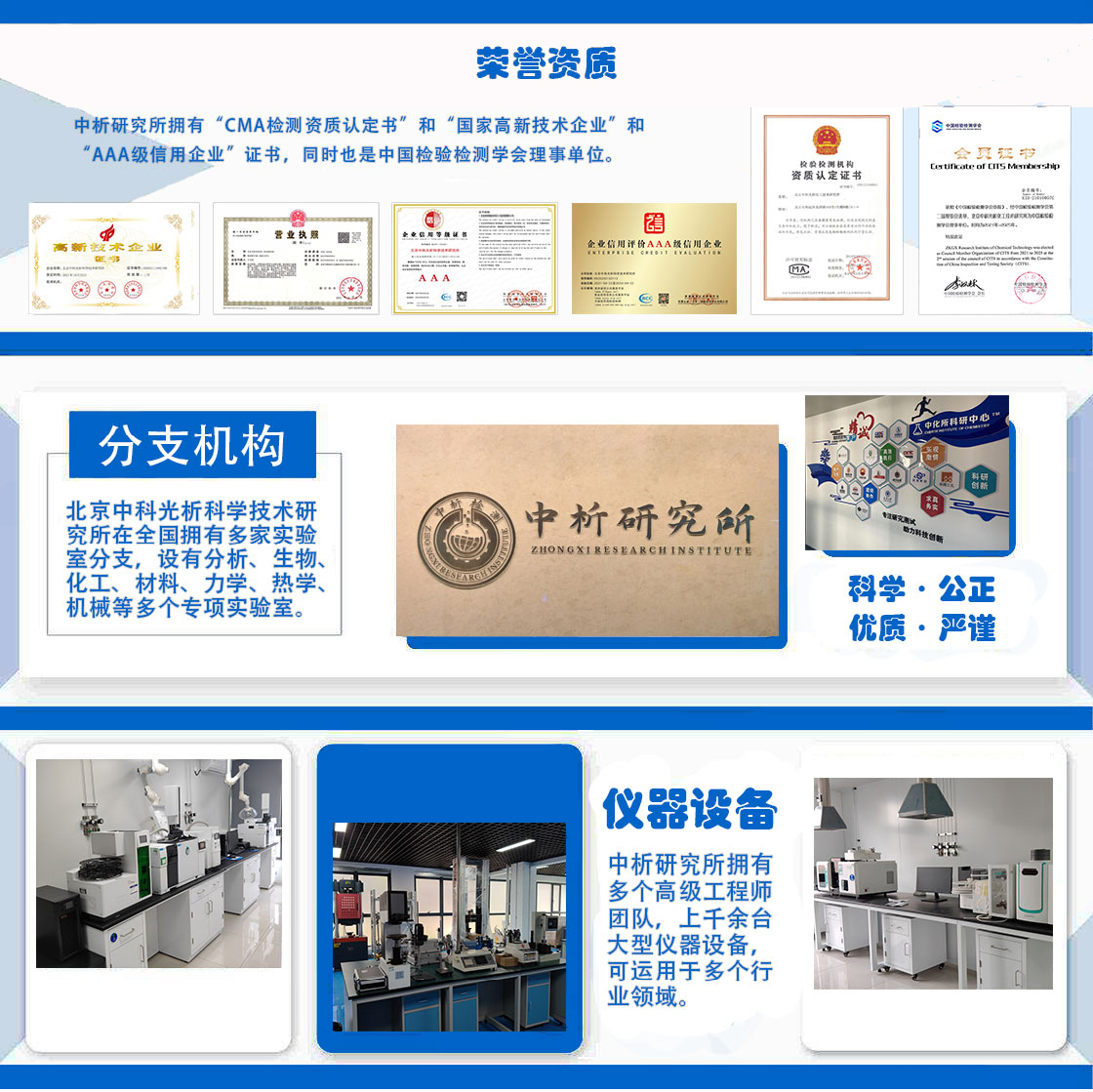
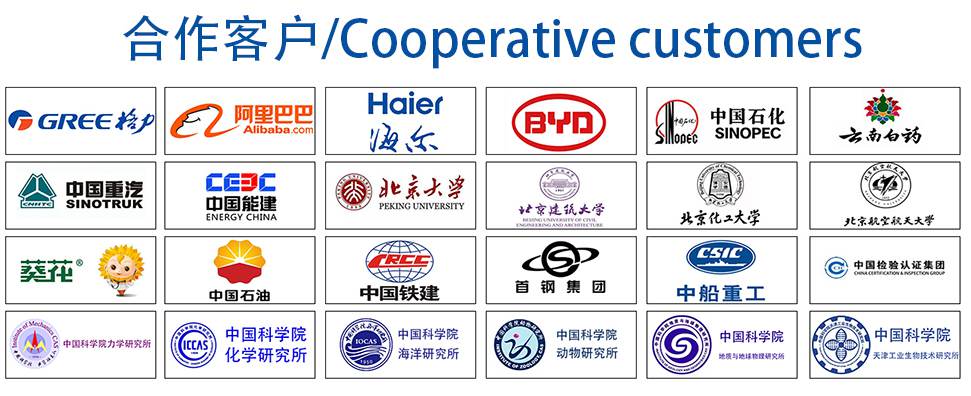