汽车电子及零部件、电工电子产品检测白皮书
汽车产业正加速向电动化、智能化方向转型,汽车电子系统在整车成本中的占比已从2010年的20%攀升至2023年的45%(据罗兰贝格《汽车电子产业报告》)。在此背景下,汽车电子及零部件、电工电子产品的检测认证成为保障产业安全与技术迭代的核心环节。以新能源汽车为例,其高压电控系统、智能驾驶模块等关键部件的可靠性直接关系到驾乘人员安全与品牌市场信任度。通过构建覆盖产品全生命周期的检测体系,企业可有效识别潜在失效模式,降低因电子系统故障导致的召回风险(2024年SGS质量报告显示:实施预防性检测可减少38%的售后质量问题)。该领域检测服务不仅满足强制性法规要求,更为企业提供技术优化数据支持,推动行业向高可靠性、高安全性方向发展。
多维融合的检测技术原理
现代汽车电子检测采用物理-化学-数字三重验证体系,重点攻克电磁兼容性(EMC)、环境应力筛选(ESS)等核心技术难点。以域控制器为例,需通过ISO 11452-2标准规定的辐射抗扰度测试,在80MHz-2GHz频段内承受100V/m场强干扰。同时引入HALT(高加速寿命试验)方法,通过阶梯式施加温循、振动复合应力,快速暴露设计缺陷。针对智能网联设备,检测机构正部署V2X场景模拟平台,可复现复杂交通环境下的通信时延与数据丢包问题。值得关注的是,新能源汽车高压部件检测认证已形成独立技术矩阵,涵盖绝缘电阻(>500MΩ)、局部放电(<5pC)等关键指标。
全链条标准化实施流程
典型检测项目遵循PDCA循环管理模式,划分为需求分析、方案设计、现场测试、数据分析四大阶段。某国际检测机构的智能座舱系统电磁兼容性评估项目显示:从样机准备到报告出具需经过21道标准化工序,其中多径衰落场景模拟耗时占比达35%。在电工电子产品检测领域,IEC 62133标准要求电池系统需完成过充、短路、挤压等7类机械滥用测试,每项测试需采集电压、温度等12项实时参数。实践表明,采用自动化测试设备(ATE)可使检测效率提升40%,人工判读误差降低至0.3%以下。
跨行业应用场景解析
在华东某新能源汽车生产基地,检测机构通过部署多轴振动台与三综合试验箱,成功将电驱动系统的故障检出率从78%提升至96%。某德系车企在智能驾驶域控制器开发中,通过车规级芯片加速寿命试验,提前识别出温升导致的时钟漂移问题。值得关注的是,充电桩安全认证领域正形成新的检测范式,广东质检院的案例显示:对液冷超充桩实施IP68防水测试时,采用氦质谱检漏技术可将微孔渗漏检测精度提升至10^-7 Pa·m³/s量级。
立体化质量保障体系
行业领先机构已构建 、CMA、IATF 16949三重认证体系,检测数据可追溯性达到单个测试工步级别。上海某国家检测中心通过搭建区块链存证平台,实现检测报告哈希值实时上链,数据篡改风险降低99.7%。在人员能力建设方面,要求电磁兼容工程师至少完成200小时场景模拟实操,并通过ISTA认证考核。设备管理严格执行MSA(测量系统分析),确保振动台控制精度误差≤0.05g。
展望未来,建议行业重点攻关三项能力建设:一是建立车规芯片与AI算法的协同检测模型,应对自动驾驶系统复杂度指数级增长;二是推动检测标准与UN R155网络安全法规的深度融合,构建车云一体化验证体系;三是开发基于数字孪生的虚拟检测平台,将实车路试比例从当前的60%降至30%以内。只有持续强化检测技术创新,才能为汽车电子产业的万亿级市场提供坚实质量基石。
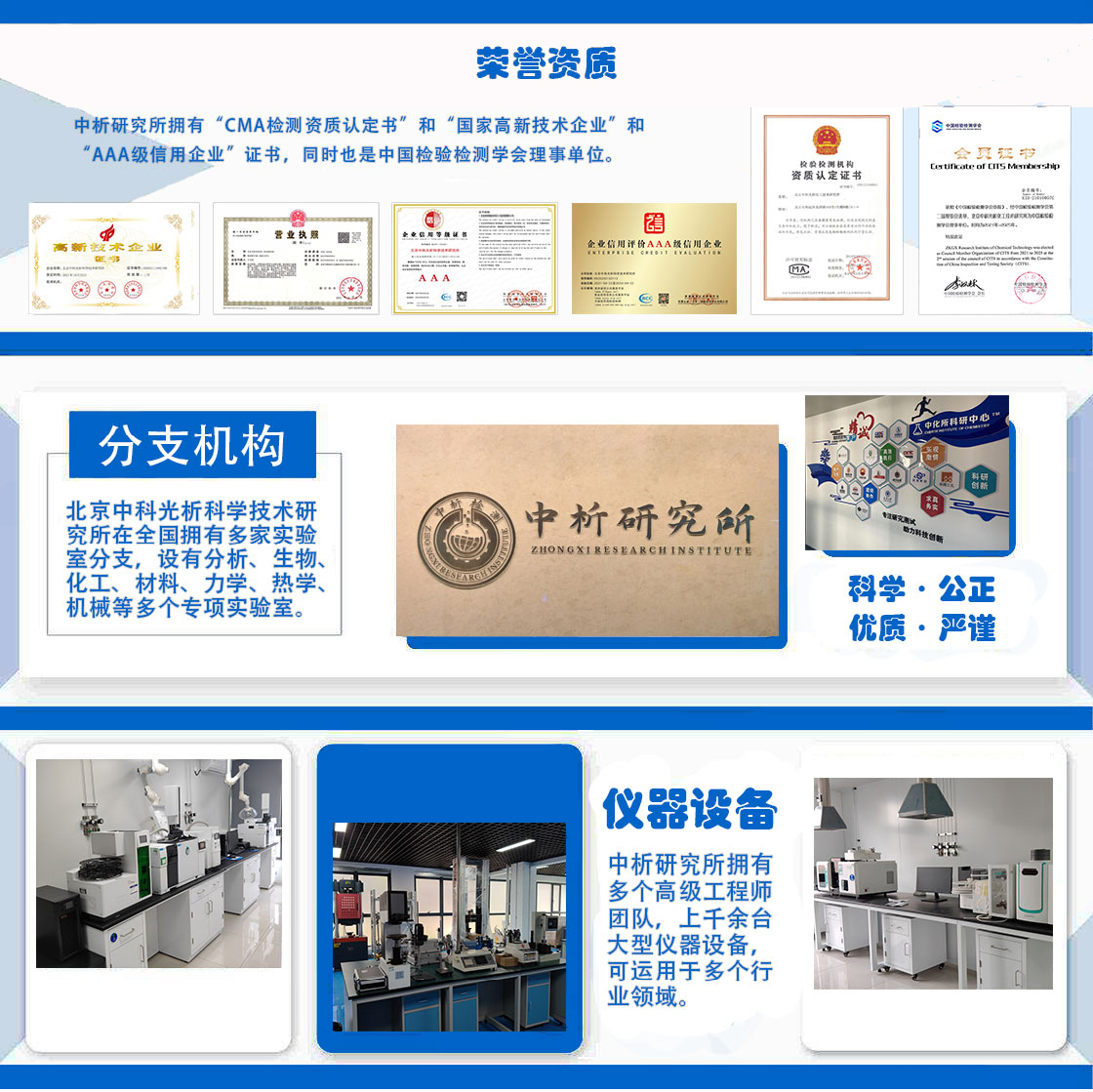
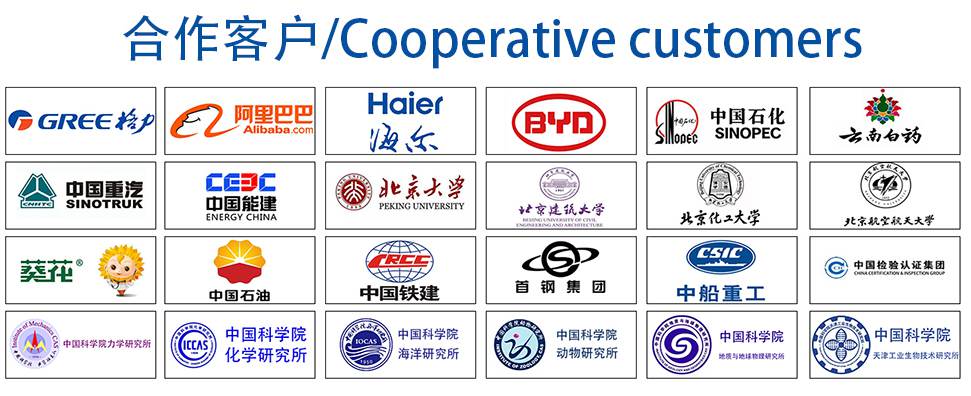