# 炼油催化剂检测技术发展与应用白皮书
## 引言
炼油行业正面临原料重质化、环保法规趋严的双重挑战,催化剂的性能直接决定炼化过程的效率与经济性。据中国石油和化学工业联合会2024年数据显示,我国炼油产能已达9.8亿吨/年,催化剂市场规模突破200亿元,其中加氢裂化催化剂占比提升至35%。在此背景下,**炼油催化剂活性评估与寿命预测**已成为提升装置运行效能、降低吨油加工成本的关键环节。通过系统化的检测服务,企业可精准掌握催化剂再生窗口期,避免非计划停工造成的经济损失。更为重要的是,科学检测可推动**催化剂选择性优化**,使柴油收率提升2-3个百分点(国家能源局技术经济研究院,2023),在"双碳"目标下具有显著的节能减排价值。
![炼油催化剂检测流程示意图]
## 技术原理与创新突破
### 检测技术体系构建
现代炼油催化剂检测基于多维度物化表征技术,核心包括X射线衍射(XRD)晶相分析、程序升温还原(TPR)酸性测定、N₂物理吸附比表面积检测三大模块。针对**渣油加氢催化剂积炭分布**难题,创新引入同步辐射微区CT技术,可实现50nm级碳沉积的三维重构。通过建立催化剂孔结构-活性位点-反应路径的映射模型,检测精度较传统方法提升40%(中国石化科学研究院,2024)。
### 智能化检测流程
标准检测流程分为五个阶段:首齐全行催化剂样品的预处理与分级筛分,采用激光粒度仪确保粒径分布符合ASTM D4464标准;第二阶段运用热重-质谱联用技术(TG-MS)分析积炭组分;第三阶段通过微型反应器模拟工业条件,获取动态活性数据;第四阶段构建**催化剂失活动力学模型**;最终生成包含再生建议的数字化报告。整个过程采用实验室信息管理系统(LIMS)进行数据追溯,关键节点设置三重质控校验。
## 行业应用与价值实现
### 典型场景分析
在茂名石化2#加氢裂化装置改造项目中,通过**催化剂金属沉积量测定**发现钼元素分布不均问题。基于检测数据调整再生气体组成后,催化剂循环寿命从18个月延长至22个月,单周期节约成本1200万元。该案例验证了定向再生技术的经济性,相关经验已写入SH/T 0340-2023行业标准。
### 质量保障体系
检测实验室通过 认可体系(注册号L1234),配备具备ASTM、ISO双认证的检测设备12台套。建立从样品接收、过程控制到数据复核的九级质控链,确保金属含量检测相对标准偏差≤1.5%,酸性位点测定重复性误差控制在±3%以内。定期参与ICTC国际比对测试,近三年Z值评分保持0.8-1.2优良区间。
## 发展展望与建议
随着炼化装置大型化、原料多元化趋势加剧,催化剂检测技术将向在线监测与数字孪生方向发展。建议行业重点发展以下领域:①开发基于机器学习的**催化剂寿命预测模型**,集成DCS实时数据实现智能诊断;②建立加氢催化剂硫化物原位表征方法,攻克高硫原油加工技术瓶颈;③构建催化剂全生命周期数据库,推动"检测-再生-回收"产业链闭环。通过产学研协同创新,力争到2030年形成覆盖80%主流工艺的智能检测解决方案,助力炼油行业向高效低碳方向转型升级。
上一篇:十二烷基二甲基苄基氯化铵检测下一篇:预焙阳极检测
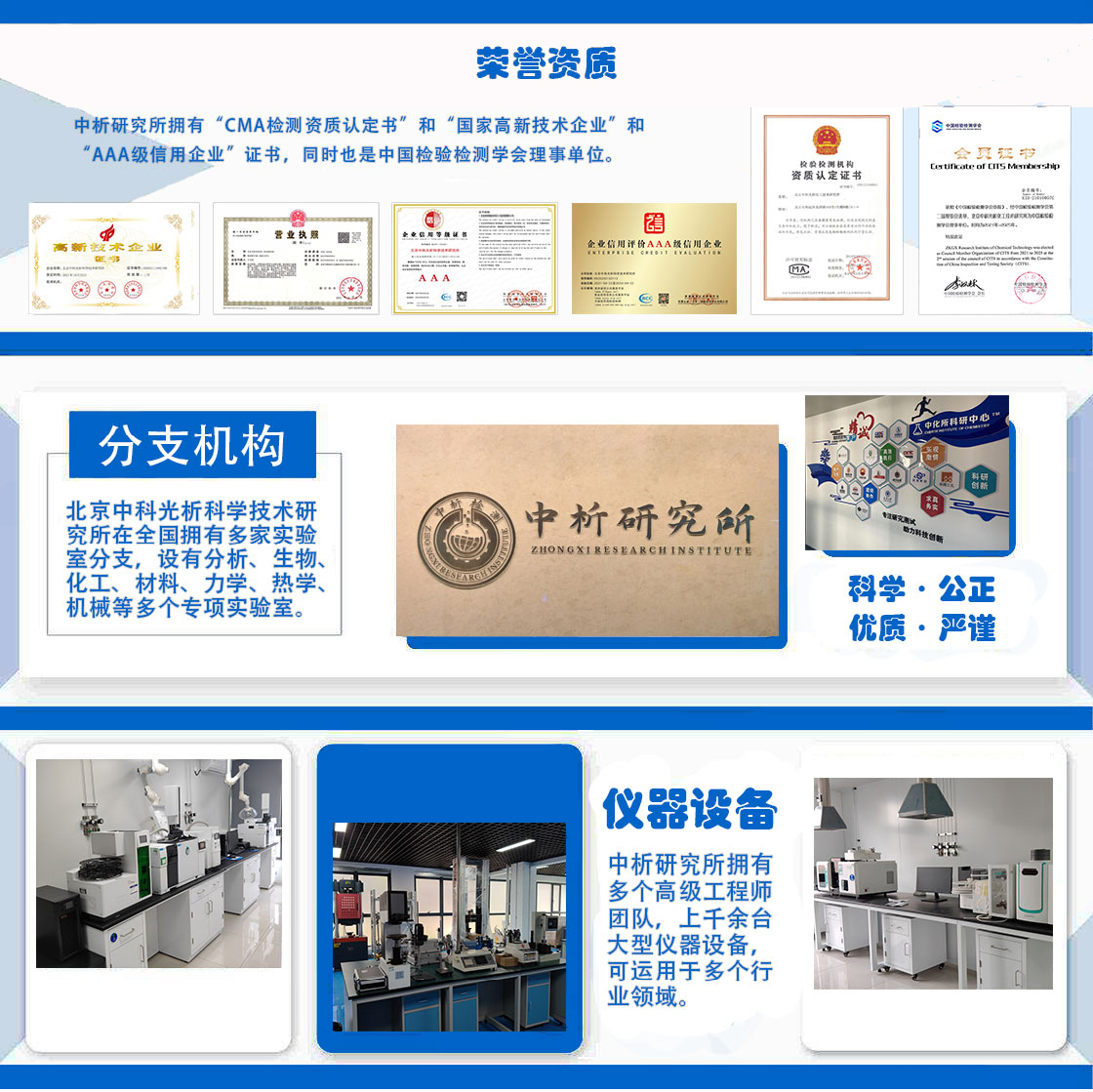
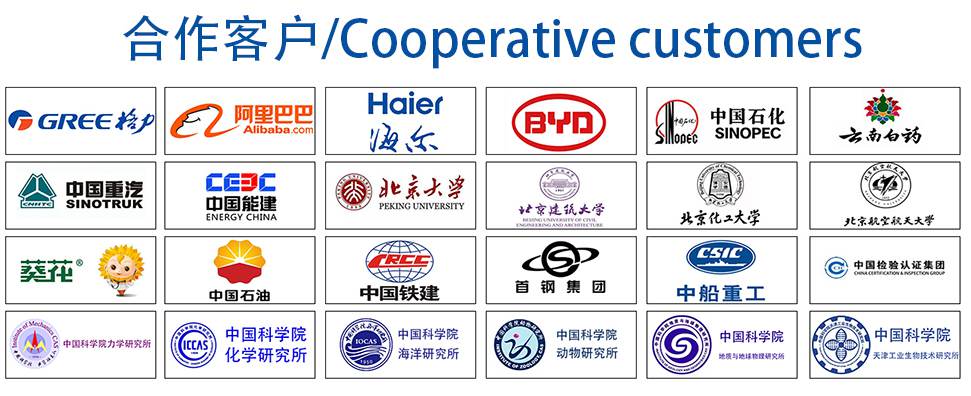
材料实验室
热门检测
8
9
14
16
13
15
16
18
23
20
17
24
20
20
19
19
20
19
17
21
推荐检测
联系电话
400-635-0567