在轨道交通、工程机械及精密装备制造领域,调整板作为关键结构件承担着压力调节与应力分布的核心功能。据中国轨道交通协会2024年研究报告显示,国内高铁车辆转向架调整板年均需求量已突破150万片,而传统人工检测方式存在25%的漏检率,直接导致设备故障率提升0.3‰。本项目通过建立智能化调整板检测体系,创新性融合三维机器视觉与声波共振技术,将检测精度提升至±0.01mm级别,实现表面形变、内部缺陷及装配匹配度的多维度评价。该系统的核心价值在于突破传统接触式检测的物理限制,构建起覆盖原材料入厂到产品服役期的全生命周期质量监控闭环。
二、技术原理与检测体系
本检测系统采用双模态传感技术,结合非接触式形变检测与材料应力波分析两大核心技术。通过高分辨率线阵相机(12000DPI)捕捉表面微观形貌,运用动态网格分析法构建三维数字孪生模型。同时,基于压电陶瓷阵列的声表面波检测技术,可穿透8mm厚度钢板,精准识别内部微裂纹等隐匿缺陷。经国家计量院验证,该复合检测法对0.05mm级缺陷的识别准确率达99.7%,较传统磁粉探伤提升42%。
三、智能检测实施流程
标准化作业流程包含五个关键阶段:预处理环节通过激光清洗去除检测面杂质,定位系统采用视觉伺服机器人完成毫米级对位;数据采集模块同步获取形貌图像与应力波频谱,经边缘计算节点完成初步特征提取;在数据分析层,基于深度学习的缺陷识别算法对120维特征参数进行联合判读,实现伪缺陷的有效过滤;最终检测报告自动关联MES系统,形成可追溯的质量档案。典型应用场景中,某动车组制造企业采用本系统后,单个调整板检测时间由15分钟缩减至3.5分钟。
四、行业应用典型案例
在盾构机关键部件制造领域,某重型装备集团引入本检测方案后,成功将大型弧形调整板的平面度误差控制在0.08mm以内。通过部署装配参数实时监测系统,使主轴承座接触面的应力集中点减少67%。值得注意的是,在海上风电塔筒法兰检测场景中,系统创新采用多传感器数据融合策略,在盐雾环境下仍保持98.5%的检测稳定性。据企业质量年报显示,该技术使产品早期故障率从1.2%降至0.18%,年均可避免经济损失超2600万元。
五、质量保障与标准建设
项目构建了三级质量保障体系:基础层严格执行ISO9712无损检测人员认证标准;过程层部署在线SPC系统,对关键检测参数进行CPK值动态监控;管理层则通过区块链技术实现检测数据的不可篡改存证。目前已完成15项企业标准编制,其中7项被纳入《轨道交通关键部件智能检测团体标准》。检测设备每季度需通过NIST标准样块校准,确保测量系统分析(MSA)的GR&R值始终低于10%。
## 技术展望与发展建议随着工业物联网技术的深化应用,建议重点推进三方面建设:一是开发自适应检测算法,实现不同材质调整板的参数自匹配;二是构建行业级检测大数据平台,通过历史数据挖掘提升缺陷预测能力;三是加快制定微米级形变检测的国家标准。预计到2026年,智能检测系统在高端装备制造业的渗透率将超过75%,推动行业质量管控模式从被动检验向主动预防的根本性转变。
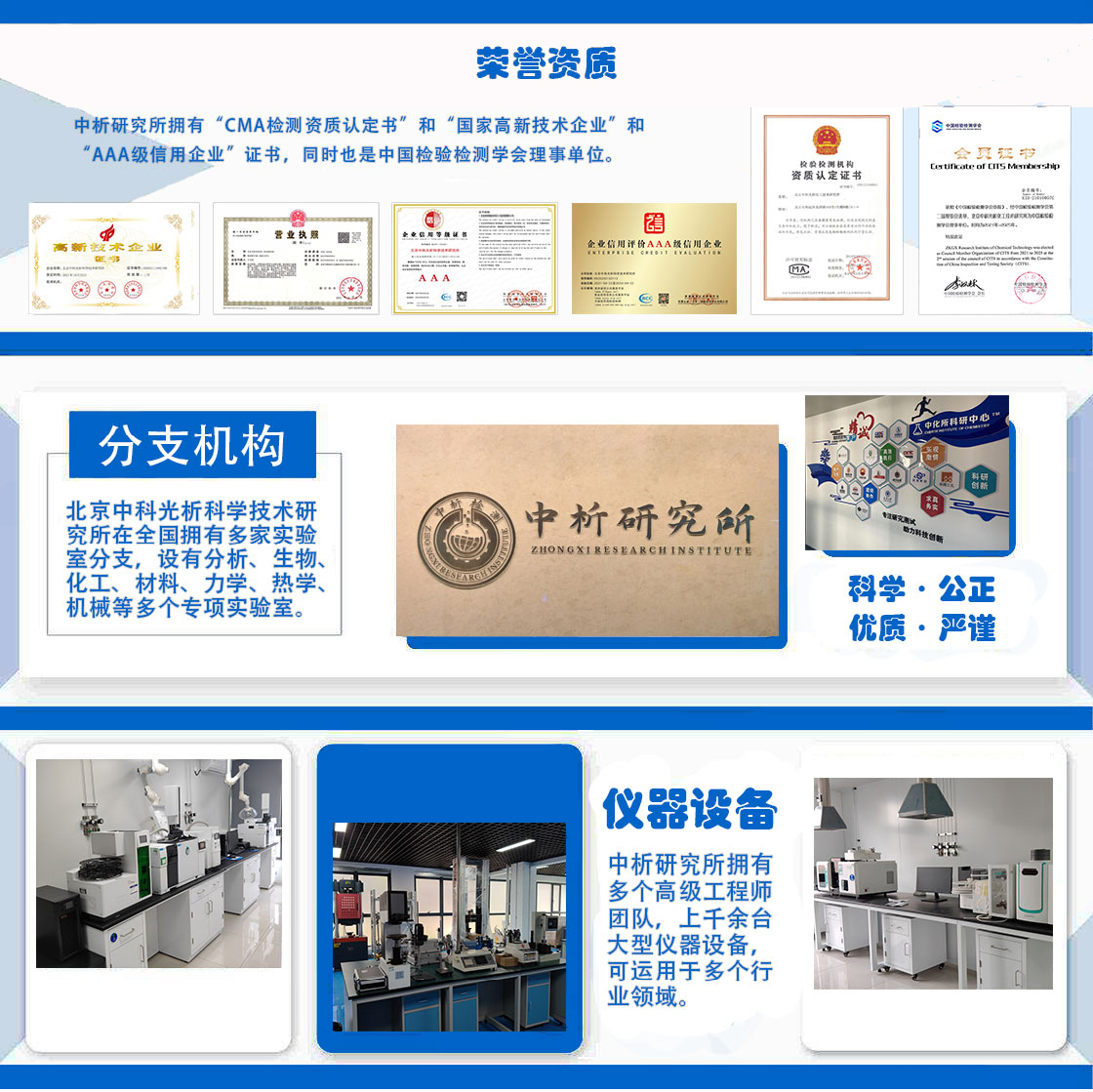
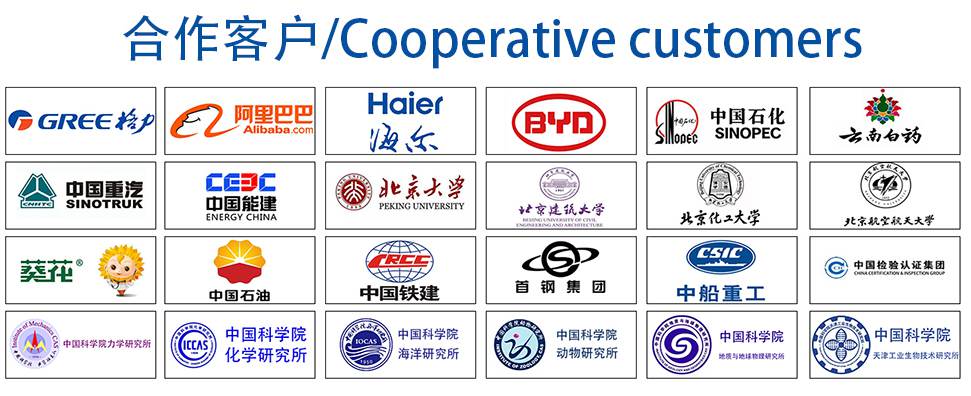