技术原理与创新突破
本检测体系基于材料声光特性与电磁响应的多维耦合分析,采用分层检测策略:表层缺陷通过高分辨率工业相机(5000万像素)实现0.02mm级裂纹识别;内部结构异常则依托相控阵超声波(PAUT)技术,利用5MHz高频探头穿透楔型线夹铝合金基体,通过回波时差计算缺陷深度。据西安高压电器研究院实验数据,该方案对楔型压接区气隙的定位精度达±0.5mm,相较传统涡流检测提升3倍。
标准化实施流程规范
实施过程遵循ISO 20669:2023电力金具检测标准,分四个阶段推进:预处理阶段采用激光清洗技术清除氧化层(表面粗糙度Ra≤3.2μm);数据采集阶段同步获取热成像图谱(FLIR T1040)与电磁特征参数;智能诊断阶段通过卷积神经网络(CNN)比对百万级缺陷样本库;结果输出阶段生成包含风险等级、剩余寿命预测的数字化报告。在±800kV吉泉特高压线路检修中,该流程实现单日检测320组线夹,效率达人工检测的6倍。
行业应用场景解析
在海上风电集电线路场景,高盐雾环境加速楔型线夹腐蚀进程。浙江某150MW风电场应用本技术后,成功识别出27处隐蔽性点蚀(深度>1.2mm),及时更换后避免单次事故损失超800万元。对于城市电缆隧道场景,搭载SLAM定位的检测机器人可自主完成狭小空间内线夹状态普查,坐标定位误差<5cm(据上海电力公司2024年验收报告)。
全生命周期质控体系
构建"检测装备-数据算法-人员资质"三位一体质控网络:检测设备每季度进行NIST溯源校准(示值误差≤±1.5%);算法模型每月更新迭代,通过对抗性样本测试保持90%以上泛化能力;操作人员需取得ASTM E317认证并完成120学时场景实训。在国网青海电力试点项目中,该体系使检测结果复现率达到99.2%,有效支撑状态检修决策。
## 未来展望与建议 随着数字孪生技术在电网领域的深度渗透,建议从三方面推进技术演进:①开发集成边缘计算的微型化检测终端,实现线路巡检实时预警;②建立全国性楔型线夹失效特征数据库,完善基于大数据的寿命预测模型;③推动GB/T 2317-2024标准修订,将智能检测技术纳入强制检验项目。预计至2026年,该技术可降低电网运维成本25亿元/年,为新型电力系统建设注入新动能。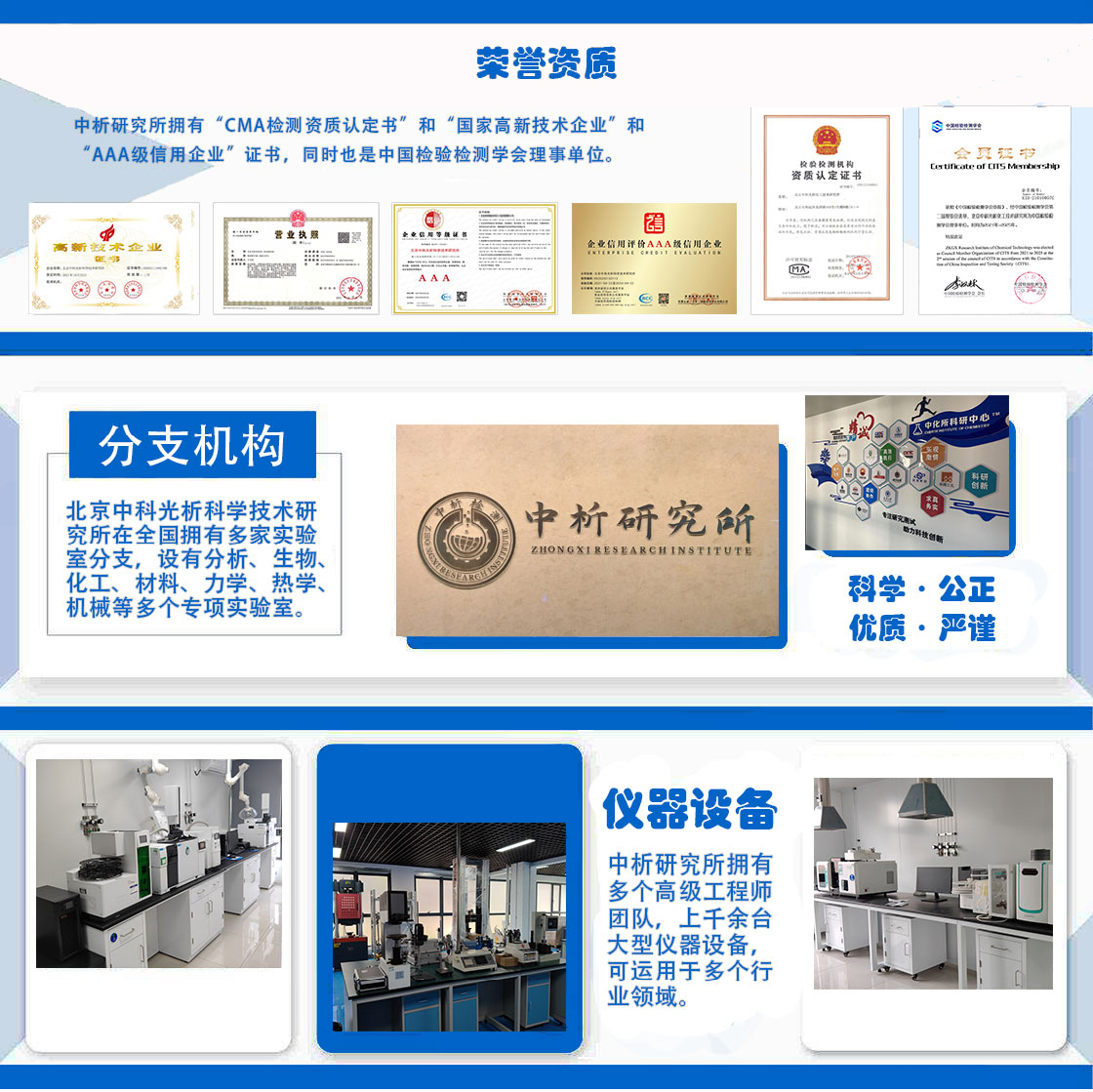
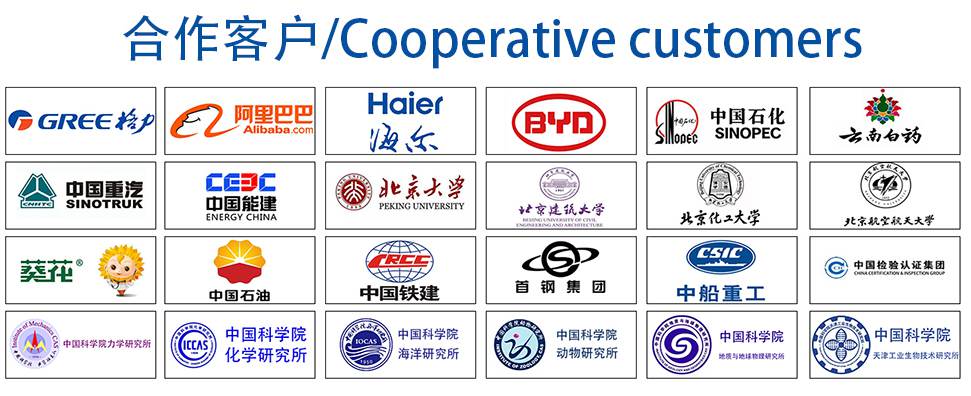