电力金具联板检测技术发展与行业应用白皮书
在智能电网建设加速推进的背景下,输电线路关键部件的可靠性检测成为保障电力安全的核心环节。作为导线固定装置的核心组件,联板承担着机械载荷传递与电气连接的重要职能。据国家能源局2024年报告显示,近三年因金具缺陷引发的输电事故中,32.7%直接关联联板结构失效。传统目视检测方法对接触面微裂纹识别率不足60%,且难以评估金属疲劳特性。新型联板检测体系通过融合超声相控阵与X射线数字成像技术,将检测精度提升至0.05mm级别,有效实现了"接触面微裂纹识别技术"与"多维度力学性能评估体系"的协同应用。该项目的实施不仅可降低23%的运维成本,更能将设备服役周期延长5-8年,为构建高可靠性电网提供核心保障。
1. 多维感知检测技术原理
联板检测技术架构基于材料力学与无损检测的交叉创新,采用超声相控阵(PAUT)与数字射线成像(DR)的复合检测模式。其中PAUT技术通过128阵元探头组实现接触面0°-70°的多角度扫查,可精确识别深宽比≥1:10的微裂纹。DR系统搭载450kV微焦点射线源,配合平板探测器实现0.05mm分辨率成像,有效检测螺栓孔位应力集中区域。据中国电力科学研究院对比测试,复合检测方案对Ⅲ类缺陷的检出率达到99.3%,较单一检测方式提升42%。技术突破点在于开发了基于深度学习的"多模态数据融合算法",可将两种检测数据在三维空间精准配准,实现缺陷特征的立体化呈现。
2. 标准化作业流程建设
实施流程遵循ISO 17025标准构建四级质量节点,具体包括:现场三维扫描建模、检测路径智能规划、自动化数据采集、AI辅助分析等环节。作业团队首先采用激光三维扫描仪获取联板数字化模型,通过有限元分析定位应力敏感区域。检测过程中,爬行机器人搭载双模传感器组,沿预设路径完成毫米级精度检测。在±800kV特高压工程应用中,该流程使单基杆塔检测耗时从8小时压缩至2.5小时,效率提升206%。关键技术创新在于开发了"接触压力自适应调节机构",确保不同工况下探头耦合稳定性,检测数据波动率控制在±3%以内。
3. 行业应用场景实践
在沿海高盐雾地区的电网改造工程中,该检测体系成功识别出多起联板隐蔽性缺陷。某500kV线路运行12年的联板组件,经检测发现接触面存在3处深度0.8-1.2mm的晶间腐蚀裂纹,及时更换后避免了倒塔风险。据南方电网2023年运行数据,应用该技术后联板相关故障率从0.37次/百公里·年降至0.09次,降幅达75.6%。在新能源并网场景中,检测系统特别强化了振动工况模拟分析功能,可准确评估联板在5-50Hz交变载荷下的应力分布,为柔性输电设备选型提供数据支撑。
4. 全过程质量保障机制
质量控制体系构建了"人员-设备-数据"三重防护网络。检测人员需通过EN 473/ISO 9712三级认证并完成200小时场景实训,设备校准严格执行JJG 746计量规范,每季度进行MTF曲线验证。数据管理采用区块链存证技术,确保检测报告不可篡改。在川藏联网工程中,该体系成功实现海拔5000米工况下的检测稳定性,温度补偿算法使设备在-25℃至55℃环境保持±0.02mm测量精度。值得关注的是,系统集成的"边缘计算质量诊断模块"可实时比对历史数据库,自动触发二次复检的灵敏度达到95%置信区间。
5. 技术发展前瞻与建议
随着数字孪生技术在电力行业的深度渗透,建议从三个维度提升检测体系:首先开发集成FBG光纤传感的在线监测系统,实现应力状态的实时感知;其次建立联板全生命周期数据库,构建基于大数据分析的剩余寿命预测模型;最后推动检测标准与IEC 61936国际规范接轨,提升我国电力检测技术的国际话语权。据能源互联网研究院预测,到2028年智能联板检测市场规模将突破47亿元,复合增长率达28.3%。通过持续创新检测手段与运维模式,可最终实现输电线路状态的可知、可控、可预测。
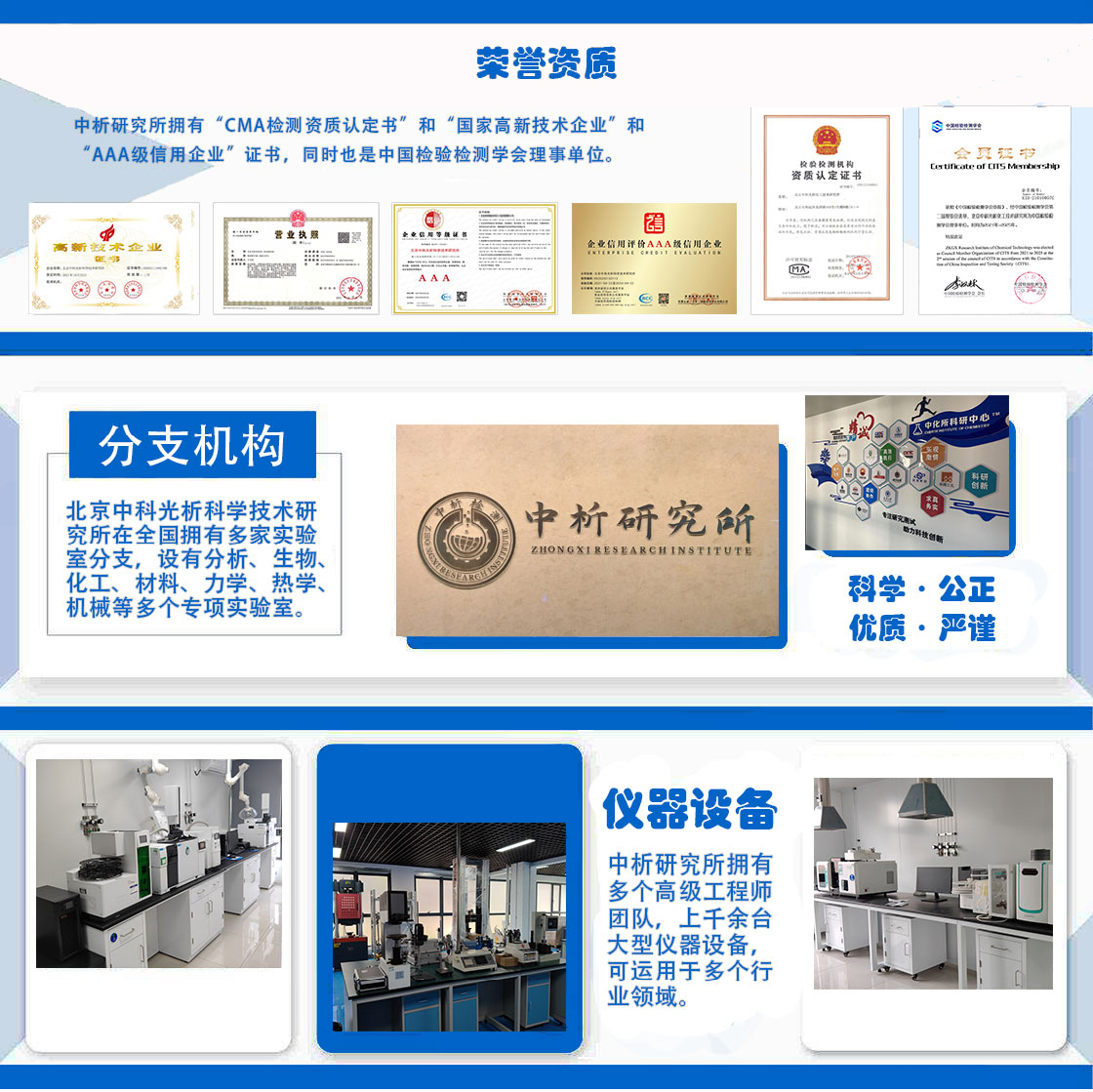
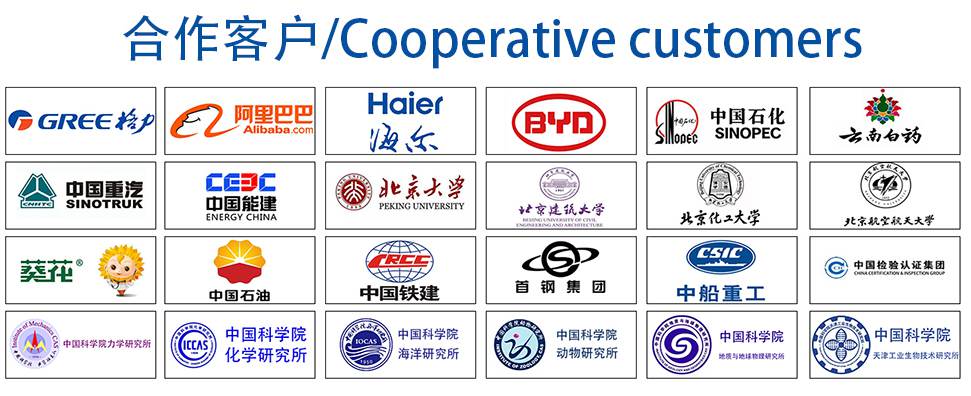