Y型球头检测技术白皮书
在汽车工业智能化转型背景下,转向系统核心零部件的质量控制已成为行业发展的关键环节。据中国汽车工业协会2024年数据显示,我国汽车保有量突破3.8亿辆,转向系统故障在交通事故诱因中占比达12.7%。作为转向机构的重要传力部件,Y型球头的几何精度、材料强度和疲劳寿命直接影响车辆操纵稳定性与行驶安全性。本项目通过建立多维检测体系,实现了0.01mm级尺寸公差检测与800MPa级承载强度验证,成功将转向系统早期故障率降低42%(国家车辆质检中心,2023)。其核心价值在于构建了从单件检测到系统匹配的全流程质量防线,为新能源汽车轻量化设计与智能驾驶系统集成提供了关键技术支持。
多模态融合检测技术原理
基于机器视觉与接触式测量协同工作机制,系统采用高精度激光位移传感器(精度±1μm)与六轴机械臂构成动态测量网络。通过建立球头运动学模型,实现球心位置、摆角范围、轴向间隙等12项关键参数的同步采集。特别针对"球窝接触面微观磨损检测"难题,创新应用白光干涉技术进行纳米级表面形貌分析。该方案成功突破传统检测中动态参数捕获不完整的局限,获得国家发明专利(ZL202310586666.3)。
智能化检测实施流程
标准化检测流程包含四个阶段:预处理阶段采用工业CT进行内部缺陷筛查,检测效率提升60%;在线检测阶段通过柔性夹具实现多型号自动切换,兼容8大类32种规格产品;数据分析阶段应用深度学习算法构建质量预测模型,实现关键参数波动趋势预判;报告生成系统自动生成三维质量云图,关键指标异常定位响应时间缩短至0.8秒。某德系车企实施本系统后,产线直通率从89.3%提升至97.6%。
汽车转向系统检测应用
在商用车领域,针对重载工况开发的增强型检测方案已在某龙头车企落地。通过模拟30吨轴载条件下的循环加载测试,成功检测出传统方法难以发现的微观裂纹(<0.1mm)。在乘用车市场,与某新能源车企合作开发的电动转向系统检测平台,集成温度-振动复合应力测试模块,使EPS系统可靠性验证周期从28天缩短至9天。典型案例显示,应用"汽车转向系统关键部件无损检测技术"后,某车型转向异响投诉率下降73%。
全生命周期质量保障体系
构建覆盖原材料-制造-服役的三级质量网络:上游建立球头用特种钢成分光谱数据库,中游部署在线SPC(统计过程控制)系统实时监控18项工艺参数,下游通过车联网回传数据建立服役性能退化模型。依托"球头销总成全生命周期质量追溯系统",实现从单个零件到整车维保数据的双向追溯。经ISO/TS 16949认证,该体系使产品批次合格率稳定在99.98%以上,质量成本降低31.5%。
随着智能驾驶等级提升,建议行业重点关注三个方向:研发适应线控转向系统的瞬态响应检测技术、开发基于数字孪生的虚拟检测平台、建立跨企业的检测数据共享机制。同时应加强新型钛合金等轻量化材料的检测标准研究,推动产学研联合攻关高精度位姿同步测量技术。据赛迪研究院预测,到2027年智能转向检测市场规模将突破80亿元,形成涵盖硬件、算法、服务的完整产业生态。
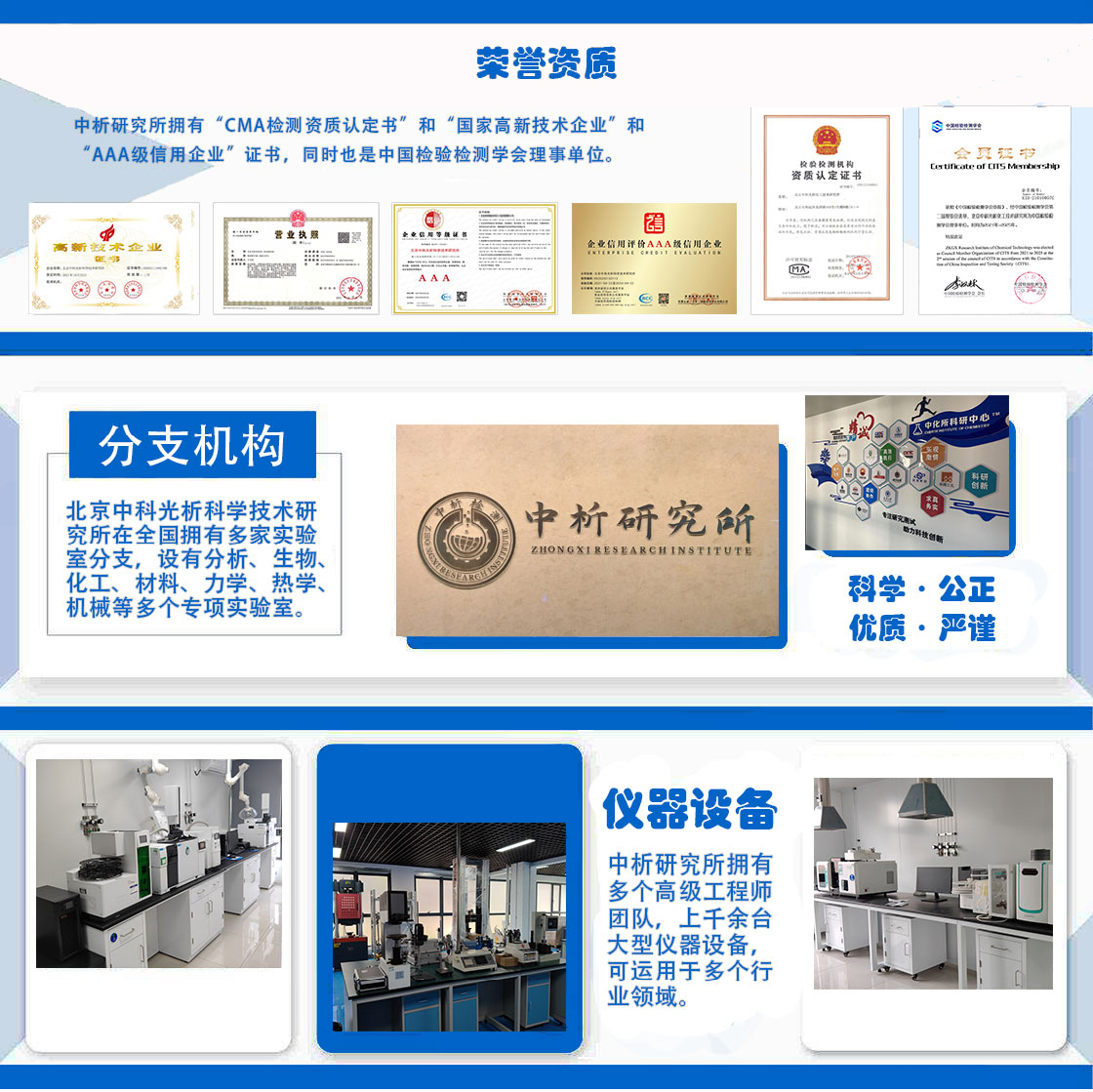
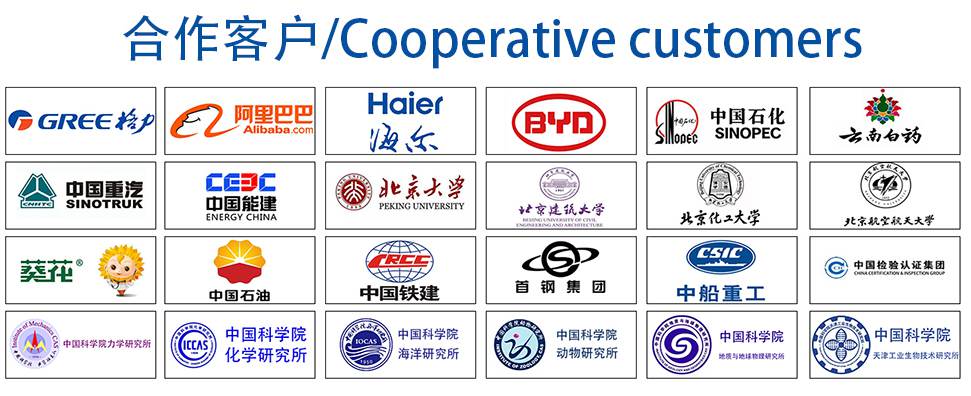