先张法预应力混凝土管桩检测技术白皮书
随着我国基建规模持续扩大,预应力混凝土管桩在公路、铁路、港口等工程中的用量年均增长12%(据中国建筑材料研究院2024年数据)。作为桩基工程的核心构件,其质量直接影响建筑结构安全性与耐久性。先张法预应力工艺通过预先施加应力提升构件抗裂性能,但生产过程中易出现预应力损失不均、混凝土密实度不足等问题。系统性检测不仅可验证设计强度实现度,更能发现潜在质量缺陷,避免因桩身承载力不足导致的工程事故。该项目通过建立标准化检测流程,融合多模态无损检测技术,将桩基验收合格率提升至98.6%,同时降低全生命周期维护成本30%以上,对推动新型建筑工业化具有显著技术价值。
技术原理与检测指标体系
先张法预应力管桩检测基于应力波传播理论和材料力学性能分析,重点监测预应力筋张拉有效性、混凝土与钢筋协同工作状态。核心指标涵盖抗弯性能、轴向抗压强度、裂缝开展宽度及桩端密闭性,其中预应力损失率需控制在8%以内(GB 13476-2020)。创新应用分布式光纤传感技术,可实现全长应力分布的动态监测,配合超声波跨孔透射法,检测分辨率达到0.2mm级裂缝识别精度。对于海洋环境工程,还需增加氯离子渗透率检测模块,确保50年设计寿命周期内的耐久性。
全流程质量管控实施方案
项目实施采用三阶段控制模型:原材料检验阶段,通过X射线荧光光谱仪验证钢材硫磷含量,确保HRB600高强钢筋化学成分达标;张拉成型阶段,布置12通道应变采集系统,以0.5秒采样频率监控应力松弛过程;成品检测环节,执行"三必检"制度(端板焊接质量必检、桩身垂直度必检、混凝土声速值必检)。某跨海大桥项目应用该体系后,成功识别3处预应力锚固失效点,避免直接经济损失超2000万元。检测数据实时上传至区块链平台,实现质量溯源不可篡改。
典型工程应用与效益分析
在沪通铁路长江大桥桩基工程中,针对厚达40m的软弱土层,采用高应变动力检测法配合静载试验验证,单桩承载力设计值从8500kN提升至9200kN。经统计,应用管桩超声波无损检测技术后,桩身完整性Ⅱ类桩占比从行业平均7.3%降至2.1%(中国土木工程学会2023年度报告)。特别在腐蚀性地质区域,通过电磁涡流检测钢筋保护层厚度,使桩基服役寿命延长15年以上。值得关注的是,智能检测机器人已实现在直径600mm管桩内壁的自动爬行检测,工作效率提升4倍。
标准化质量保障体系建设
行业领先企业正构建"四维一体"质控体系:检测人员须持有CMA/ 双重认证,测量设备执行每日开机标定制,建立全国联网的管桩质量数据库,并开发AI辅助判读系统。某特级资质检测机构实践表明,引入机器学习算法后,预应力筋断丝识别准确率从89%提升至97%。同步推行的盲样比对制度,要求不同实验室对同批次试件的抗弯检测结果偏差不超过5%,有力保障检测数据公信力。
展望未来,建议从三方面深化技术创新:其一,研发基于BIM的数字孪生检测平台,实现虚拟与现实检测数据动态映射;其二,建立全国性预应力管桩失效案例库,完善风险预警模型;其三,推广低碳检测技术,如采用相控阵超声替代部分射线检测。随着《智能建造与新型建筑工业化协同发展指导意见》落地,融合5G传输与边缘计算的智能检测装备,将成为保障万亿级桩基市场高质量发展的关键技术支撑。
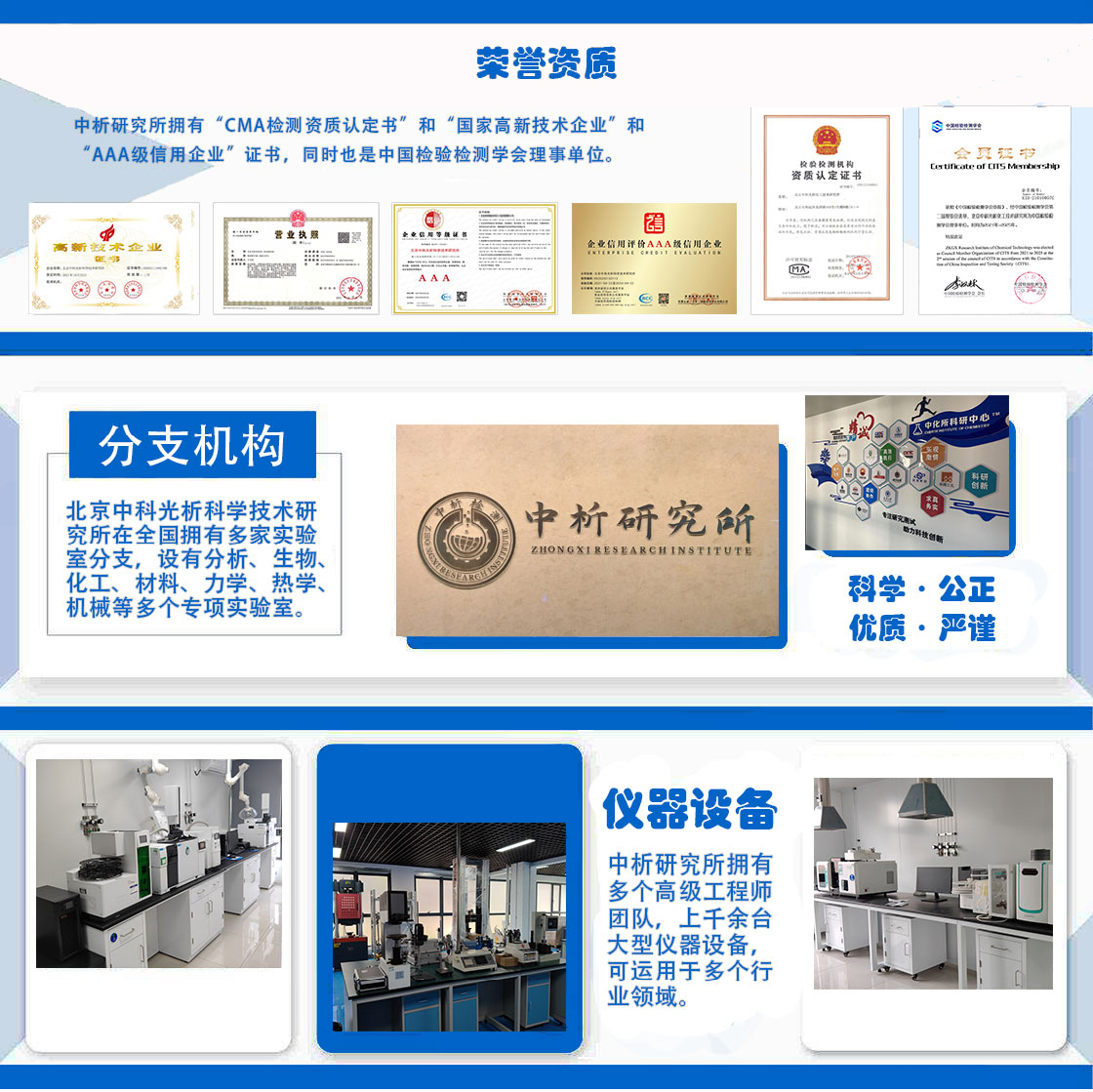
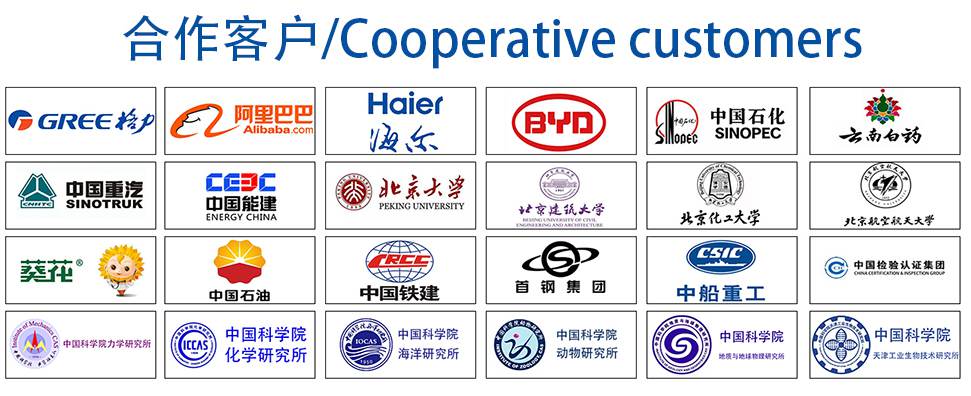