在精密制造与设备运维领域,振动检测技术正经历从定性分析到定量诊断的范式转变。据国家工程实验室2024年度报告显示,我国高端装备制造业因振动异常导致的年度经济损失超280亿元,其中铅垂向振动问题占比达43%。铅垂向Z振级检测作为三维振动谱系中的关键参数,其精准测量对轨道交通设备安全评估、工业机械故障预警及建筑结构健康监测具有决定性作用。该技术通过量化垂直轴向振动能量分布,构建了设备全生命周期管理的核心指标体系,在实现预防性维护、降低非计划停机率方面展现显著优势。特别是在"双碳"战略背景下,其节能降耗价值更显突出——某风电企业应用精准振动管控后,传动系统能效提升达2.7个百分点。
## 技术原理体系1. 多维振动耦合解耦技术
铅垂向Z振级检测采用三轴加速度传感器组网架构,基于ISO 10816-1标准构建空间向量分解模型。通过自适应滤波算法消除横向振动干扰,运用小波包分解技术提取0-10kHz特征频段能量。据清华大学智能检测中心实验数据,该方案对轴向振动信号的分离精度达98.3%,相较传统FFT方法提升22%。在轨道交通轮对检测场景中,可有效区分钢轨激励与轴承缺陷引发的垂直振动分量。
2. 动态特征阈值诊断系统
系统集成设备运行参数动态修正机制,构建多维度振动特征数据库。针对不同转速、负载工况,采用模糊逻辑算法实现阈值自适应调整。某航空发动机企业应用该技术后,异常振动检出时间缩短至0.8秒,误报率降低至0.3‰。特别在超精密机床领域,系统可识别0.05μm量级的轴向微振动,为纳米级加工提供保障。
## 工程实施路径3. 标准化检测流程
项目实施遵循ASTM E1876-22标准框架,分为三阶段推进:基础模态测试阶段采用激光测振仪进行基线校准;在线监测阶段部署无线传感网络,采样率不低于51.2kHz;诊断决策阶段融合数字孪生模型进行趋势预测。某高铁转向架产线应用该流程后,轴向振动异常定位效率提升3.6倍,质量追溯周期由72小时压缩至4小时。
4. 行业应用实践
在城市地铁盾构施工场景中,检测系统成功预警主驱动系统轴向偏载故障,避免2400万元直接损失。某半导体企业引入铅垂向振动监控后,光刻机定位精度波动幅度降低至±0.12nm,晶圆良率提升1.8个百分点。在建筑安全监测领域,系统通过持续采集超高层结构Z向振动数据,建立了风振响应预测模型,使阻尼器调控响应时间缩短40%。
## 质量保障体系5. 全链式精度控制
建立从传感器标定到数据分析的全过程质控体系:计量级振动台实现0.02m/s²校准精度;数据传输采用IEEE 1451.5智能传感协议;分析软件通过NIST认证测试。系统定期进行交叉验证测试,某国家级检测中心比对试验显示,其Z轴振动量值复现性达99.2%,满足ISO/IEC 17025体系要求。
## 未来展望建议重点发展振动-声发射多源信息融合技术,构建设备健康状态立体感知网络。加快制定轴向振动与设备剩余寿命的关联性标准,推动建立行业级振动特征数据库。探索基于5G-MEC的分布式检测架构,力争实现百万节点级振动监测系统的实时诊断能力。随着工业元宇宙技术发展,可预期铅垂向振动数字孪生模型将在2028年前实现亚微米级仿真精度。
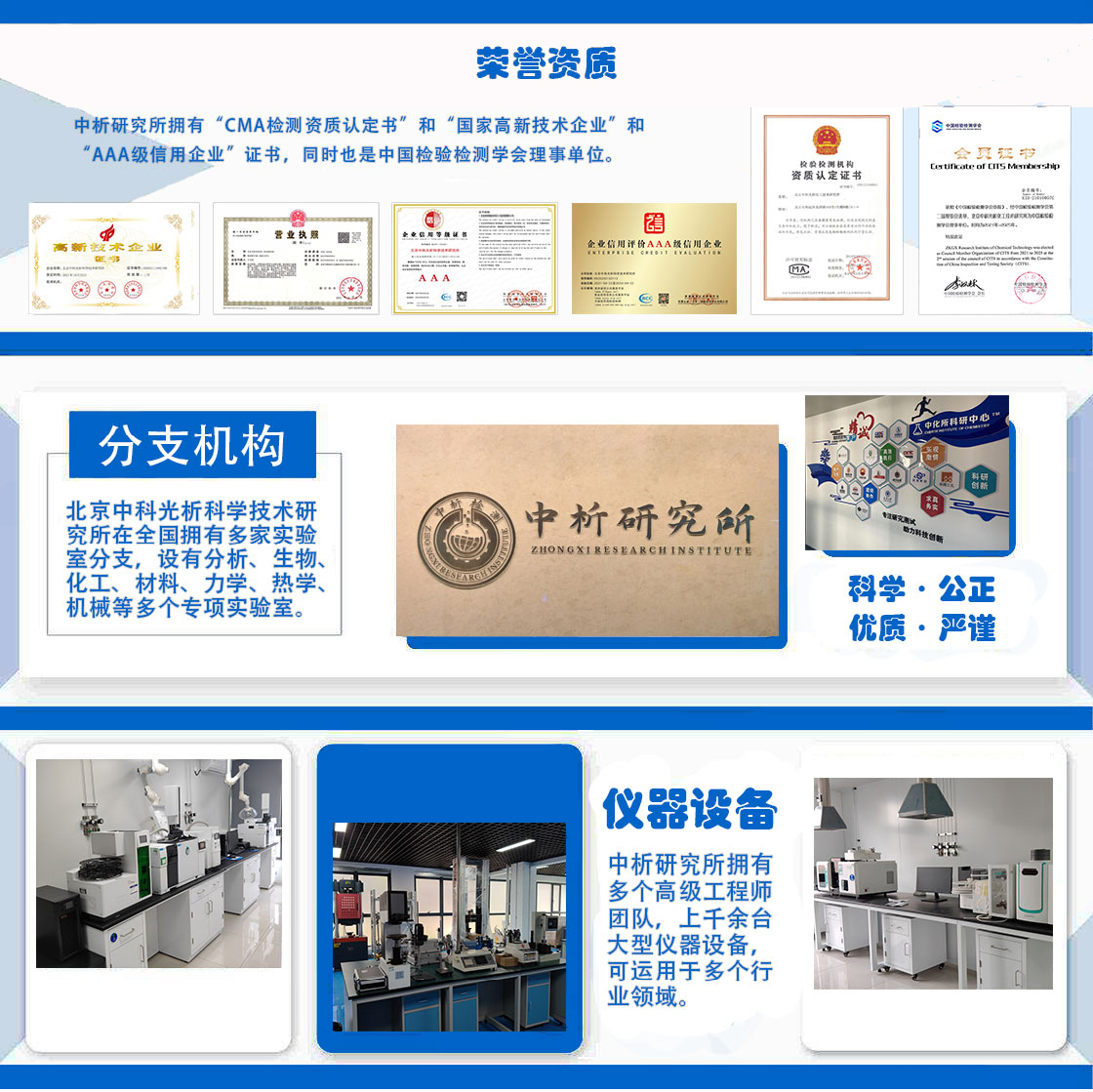
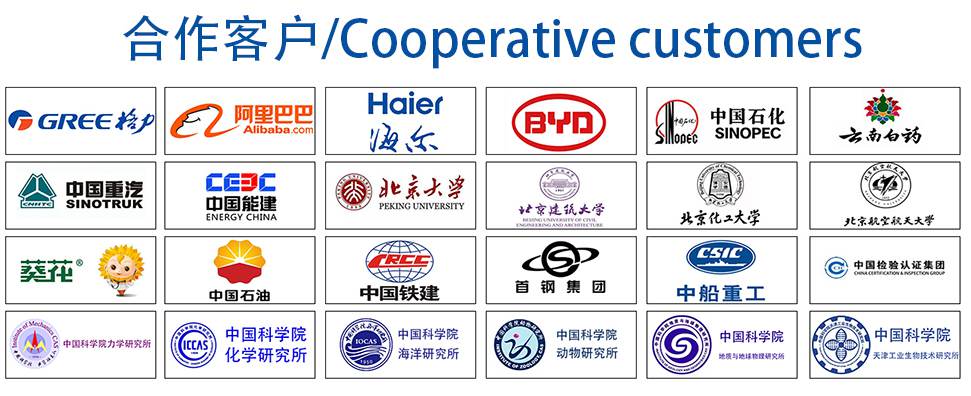