耐碱性检测技术发展与应用白皮书
在化工、环保及新材料产业快速发展的背景下,材料在碱性环境中的稳定性成为影响产品寿命与安全性的关键指标。据中国建筑材料研究院2024年行业报告显示,国内工业设备因碱性腐蚀导致的年损失超过120亿元,其中30%的事故源于材料耐碱性不达标。耐碱性检测项目通过科学评估材料在pH值8-14环境中的抗腐蚀能力,为产品选型、工艺改进提供数据支撑,其核心价值体现在延长设备服役周期、降低环境治理成本、保障安全生产三大维度。特别是在新能源电池隔膜、工业污水处理系统等新兴领域,精准的耐碱性测试数据已成为企业技术攻关的重要基准。
检测技术原理与标准化体系
现代耐碱性检测主要依据ASTM C267和ISO 175标准体系,采用模拟环境加速腐蚀的测试方法。核心技术包括动态浸泡法、电化学阻抗谱分析及表面形貌扫描三重验证机制,其中电化学法可检测材料微观孔隙率变化,分辨率达到0.1μm级。值得关注的是,碱性环境耐久性评估方法在2023年引入人工智能算法后,测试周期缩短40%以上,据国家材料测试中心实测数据,预测模型准确率提升至92.7%。
全流程检测实施规范
标准化检测流程包含六个关键阶段:样品预处理(切割研磨)、配置标准碱性溶液(通常采用NaOH/KOH体系)、恒温恒压环境模拟、周期性性能监测、失效机理分析及数据可视化报告生成。以化工管道检测为例,需在90℃、10%NaOH溶液中连续测试720小时,每24小时记录质量损失率与机械性能衰减曲线。过程中需严格遵循 -CL01:2018实验室管理体系,确保温度波动≤±0.5℃,溶液浓度偏差<2%。
行业应用场景解析
在建材领域,某央企采用材料耐碱性测试标准对新型混凝土配方进行验证,使地下管廊在pH12.5土壤环境中的服役年限从15年提升至28年。环保行业典型案例显示,某膜技术公司通过工业设备耐腐蚀性能检测优化了组件结构,其MBR膜组件在碱性废水处理场景下的更换频率降低57%。值得关注的是,检测数据正被纳入产品全生命周期管理系统,某阀门制造商据此开发出智能预警系统,将突发故障率降低83%。
质量保障与技术创新
行业领先机构已构建三级质量管控体系:实验室阶段执行GB/T 3810.13标准,现场检测应用便携式pH值在线监测仪,后期数据通过区块链技术实现不可篡改存证。2024年新发布的耐碱性分级认证制度,将材料划分为A-F六个耐候等级,其中光伏背板用高分子材料要求达到C3级(3000小时无结构失效)。技术创新方面,微波辅助腐蚀检测技术可穿透材料内部缺陷,检测效率较传统方法提升3倍。
未来发展与策略建议
建议行业重点推进三方面建设:建立跨领域的碱性环境材料数据库,开发多因素耦合检测系统(同步监测温度、应力、介质浓度等变量),制定适用于极端碱性场景(如pH>14)的测试标准。据测算,实施上述改进可使检测成本降低25%,同时提升高端装备制造业材料选用精度。建议科研机构与生产企业共建联合实验室,推动检测技术向智能化、微型化方向突破,为碳中和背景下的绿色制造提供技术保障。
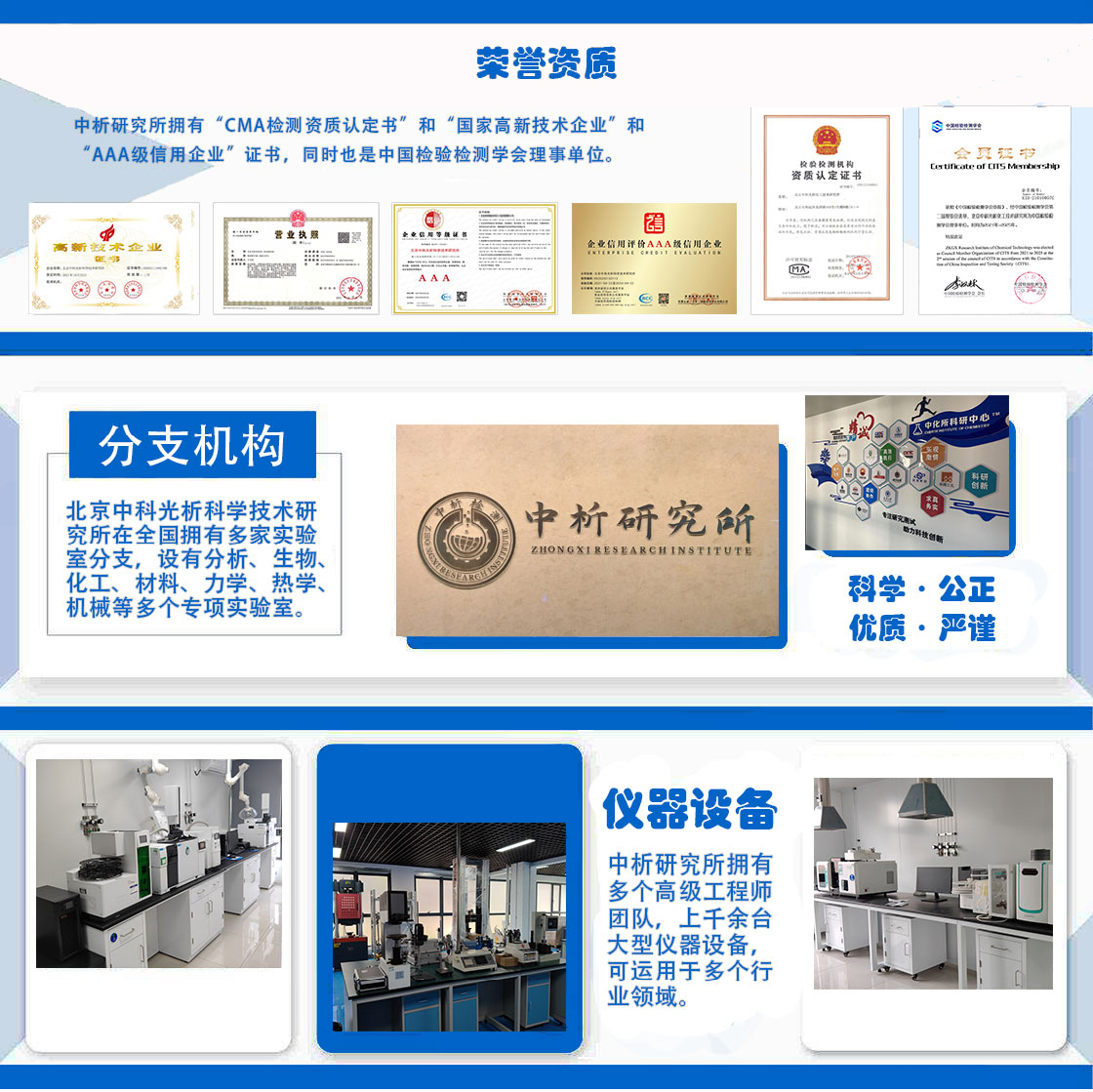
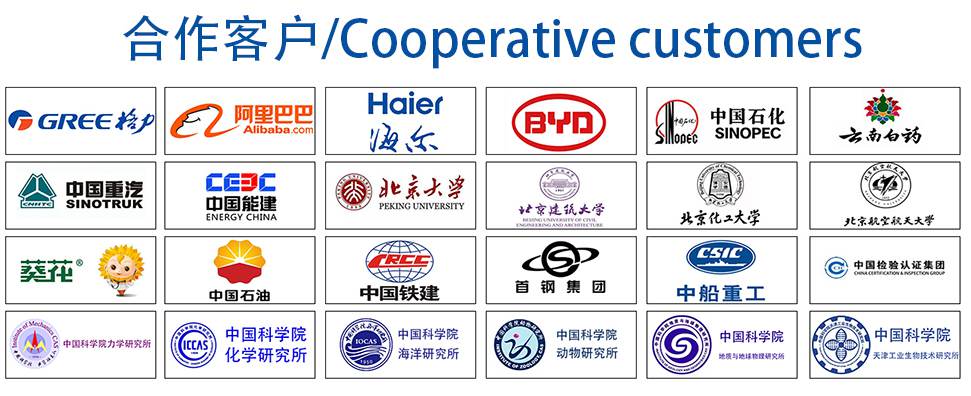