多模态融合检测体系
现代强度检测采用超声相控阵、数字射线成像(DR)与声发射技术协同工作机制。超声相控阵实现焊缝内部缺陷三维重构,DR技术捕捉0.05mm级微裂纹,声发射系统实时监测载荷下的裂纹扩展动态。特别在异种金属焊接接头检测中,多频段电磁超声技术可穿透15mm厚板材,准确识别熔合线附近的强度薄弱区。中国特检院对比实验表明,该组合方案使缺陷检出率较传统方法提升37%。
智能化实施流程
项目实施遵循ASTM E2375标准,形成"预评估-动态监测-数据建模"的闭环流程。前期利用有限元分析定位高应力区域,布设500Hz采样频率的分布式光纤传感器。在风电塔筒检测案例中,系统连续72小时采集200万个应变数据点,通过机器学习算法识别出塔筒法兰连接处的应力集中现象。实测数据显示,该技术将检测效率提升4倍的同时,降低30%的检测盲区。
行业应用典型案例
港珠澳大桥养护工程采用基于应变能密度法的焊缝强度评估体系,对8.6万处关键节点进行年度检测。通过布设3200个智能应变片,系统成功预警东人工岛连接段的3处疲劳裂纹,避免可能的结构损伤。在航空航天领域,某型号发动机涡轮盘应用了高温环境下的激光散斑检测技术,实现650℃工况下的实时强度监控,使关键部件服役寿命延长40%。
全过程质量保障
检测机构须同时具备CMA认证和EN ISO/IEC 17025体系认证,建立从设备校准到报告审核的12道质控节点。采用标准试块每日校验仪器精度,数据采集执行三级复核机制。某核电项目实践表明,通过引入区块链技术实现检测数据不可篡改存储,使质量追溯效率提升60%,有效防范建筑工程质量风险。
## 未来发展与建议 随着智能建造技术迭代,建议从三方面提升检测体系:①研发可植入式纳米传感器,实现混凝土结构内部钢筋锈蚀的强度预测;②建立钢结构数字孪生数据库,融合30年以上服役数据的强度衰减模型;③制定智慧检测国家标准,规范5G+工业互联网环境下的远程诊断流程。预计到2030年,智能化强度检测将覆盖80%以上基建项目,为城市安全运营构建数字化防线。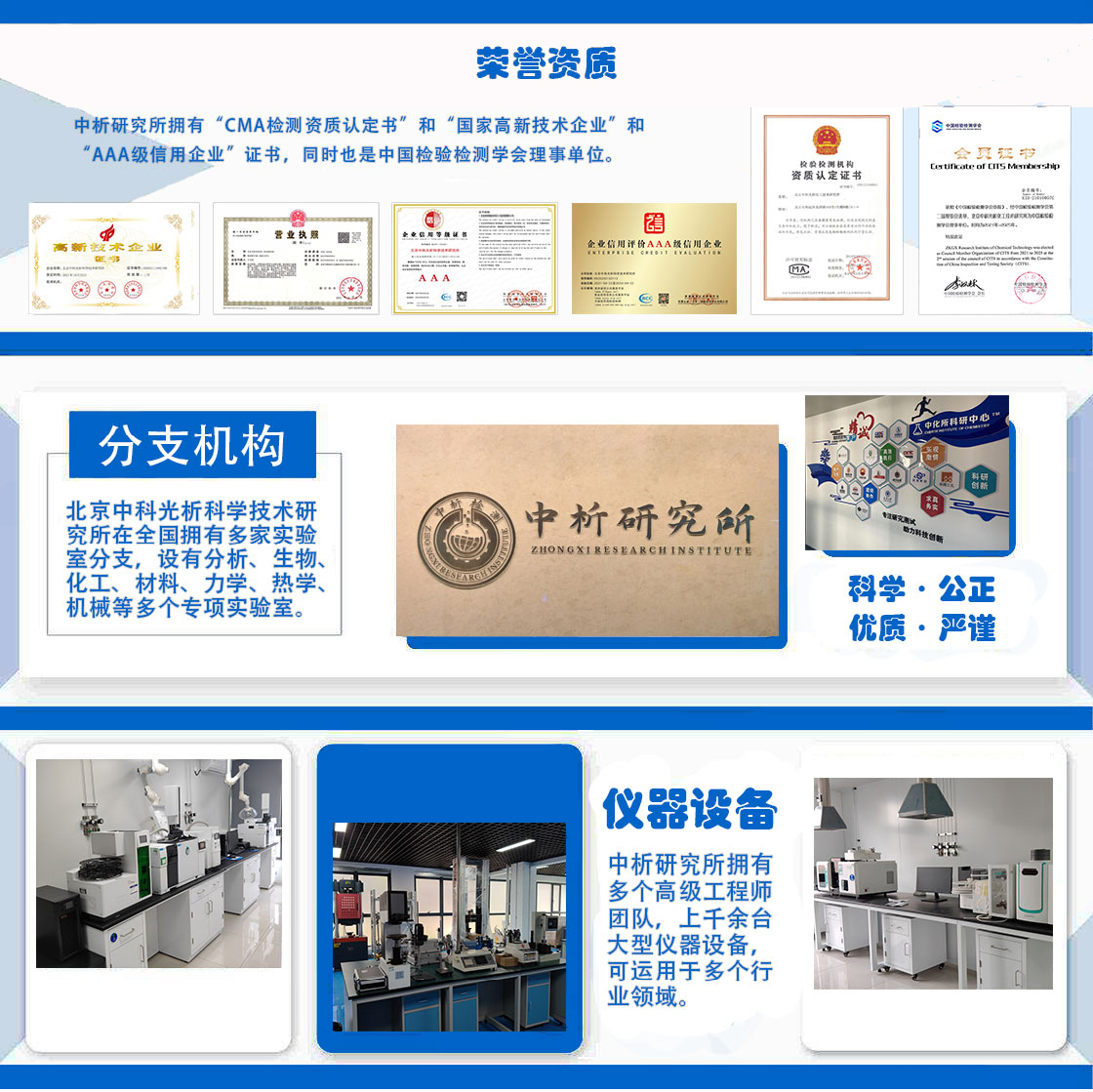
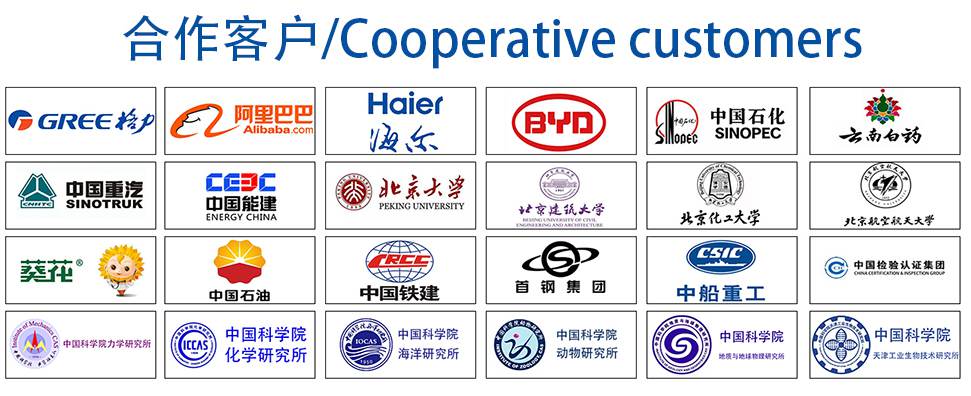