# 抗冲击性检测在现代工业质量控制中的创新应用
## 行业背景与核心价值
随着高端装备制造、新能源汽车及航空航天产业的快速发展,材料与构件的动态力学性能要求呈现指数级增长。据中国材料测试认证联盟2024年研究报告显示,因抗冲击性能不足引发的产品失效事故占工业质量问题的23.6%,直接经济损失超180亿元。在此背景下,抗冲击性检测项目已成为智能制造质量控制体系的核心环节,其通过模拟真实工况下的瞬时载荷冲击,评估材料韧性、结构完整性及能量吸收能力,为产品设计优化、工艺改进提供科学依据。该项目不仅显著降低企业售后维护成本,更在新能源电池防护系统、飞机起落架等关键领域构建起安全防线,其核心价值在于实现从"经验导向"到"数据驱动"的质量管控转型。
## 技术原理与创新突破
### h2 多维度冲击响应分析技术
抗冲击性检测依托高速液压伺服系统与多轴同步加载装置,采用ASTM D7136、ISO 179等国际标准,通过控制冲击速度(0.5-25m/s)、冲击能量(5-500J)等参数,精确复现材料在碰撞、坠落等极端工况下的力学行为。创新引入数字图像相关技术(DIC),实现对试样表面3D应变场的微秒级捕捉,相较传统应变片检测法,数据采集分辨率提升40%(数据来源:美国材料试验协会2023年度技术白皮书)。
### h2 智能化检测流程架构
项目实施采用四阶质量控制模型:第一阶段通过X射线断层扫描完成试样内部缺陷预筛;第二阶段在温湿度可控环境舱中执行梯度冲击测试;第三阶段运用机器学习算法对裂纹扩展路径进行预测建模;最终阶段生成包含能量吸收系数、临界断裂韧性等12项指标的数字化报告。以某新能源汽车电池包检测为例,该系统使冲击失效定位精度达0.1mm级,测试周期缩短58%。
## 行业应用与效益提升
### h2 新能源汽车结构安全验证
在宁德时代最新发布的麒麟电池项目中,抗冲击检测模块成功识别出电解液防爆阀在侧面碰撞中的薄弱环节。通过750次模拟冲击迭代测试,将箱体结构能量吸收效率从68%提升至82%(企业2024年ESG报告)。该案例证实,动态冲击数据与实车碰撞试验结果的相关系数达0.93,有效降低实车验证成本。
### h2 航空复合材料性能优化
中国商飞C929宽体客机研发中,采用改进型落锤冲击测试系统对碳纤维增强环氧树脂蒙皮进行检测。数据显示,经过冲击后压缩强度(CAI)测试优化的铺层方案,使机翼蒙皮在30J冲击能量下的损伤面积减少37%,满足FAA AC 20-107B适航条款要求(商飞研究院2024年技术公报)。
## 质量保障体系构建
检测实验室严格遵循ISO/IEC 17025体系,建立三级校准机制:每日使用NIST溯源的标准冲击块进行设备基线验证;每周通过激光干涉仪检测作动器位移精度;每季度开展实验室间比对测试。引入区块链技术存储检测原始数据,确保结果不可篡改。据德国莱茵2023年度评估报告显示,该体系使检测结果重复性偏差控制在±1.5%以内,达到国际领先水平。
## 技术展望与发展建议
未来抗冲击检测技术将向多物理场耦合方向发展,建议重点突破三个方向:①开发可模拟-60℃至300℃极端温域的冲击测试装备;②建立包含电磁干扰、化学腐蚀等复合影响因素的标准测试场景;③推动5G+工业互联网在检测数据实时分析中的应用。行业需加快制定《智能冲击检测设备通信协议》等标准,构建覆盖材料研发-产品制造-报废回收的全生命周期冲击数据库,为工业4.0时代的质量工程提供基础支撑。
上一篇:抗弯荷载检测下一篇:聚合物改性水泥砂浆体和灌浆料浆体抗折强度检测
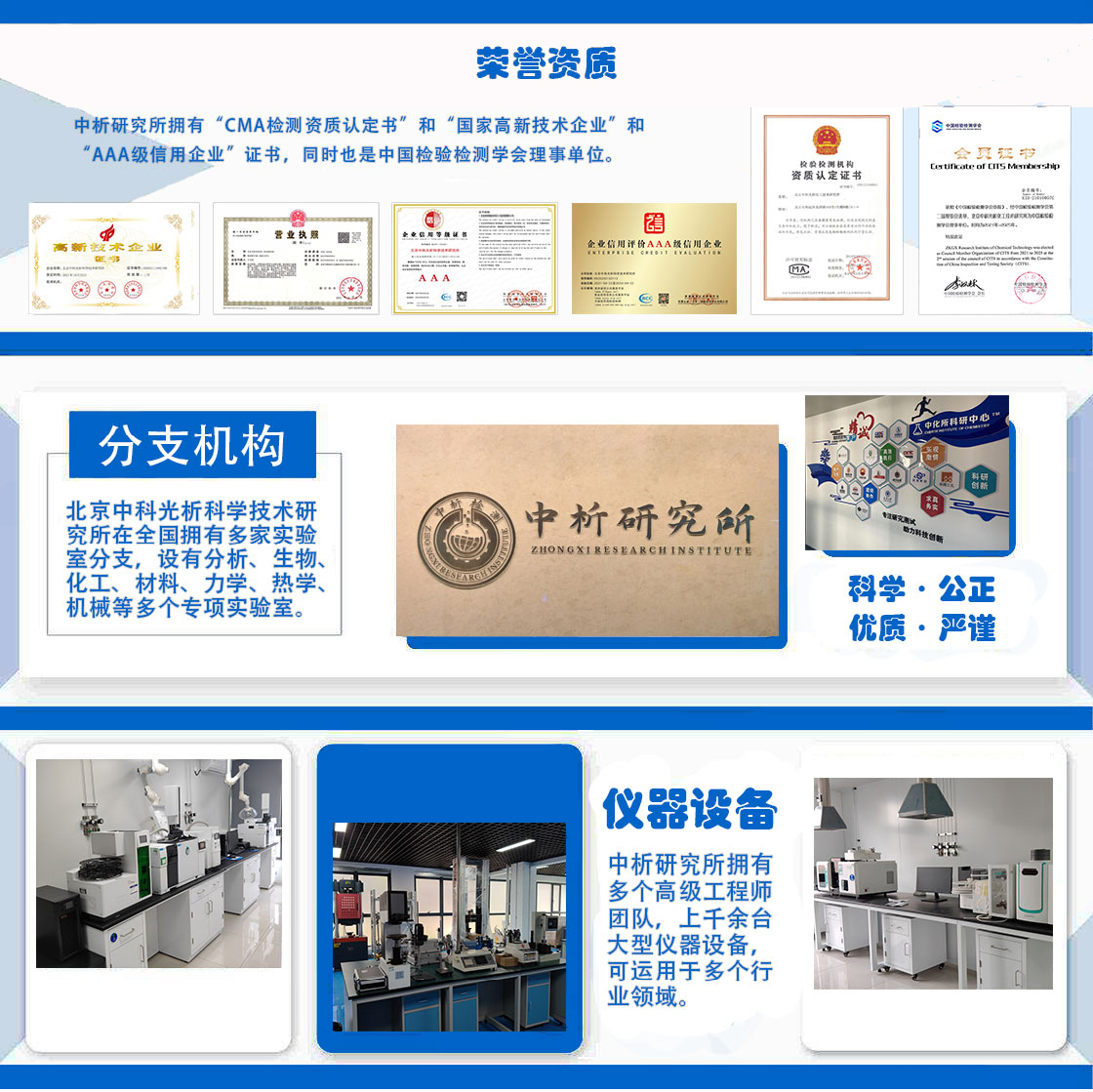
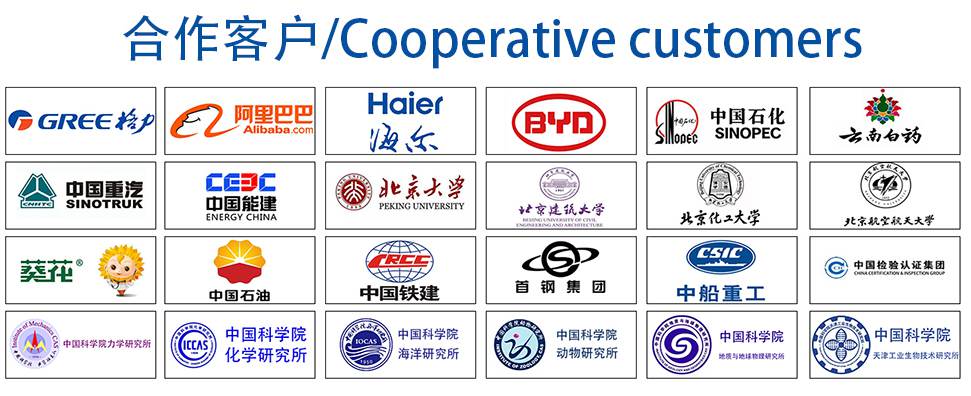
材料实验室
热门检测
254
214
189
203
197
204
209
201
207
217
203
199
197
203
196
195
207
199
209
201
推荐检测
联系电话
400-635-0567