抗弯荷载检测在工程安全评估中的关键作用
在建筑工程与制造业高速发展的背景下,结构安全性已成为行业核心关切。据中国建筑科学研究院2024年数据显示,国内每年因材料力学性能不足导致的工程事故损失超120亿元,其中32%与抗弯性能缺陷直接相关。抗弯荷载检测通过量化评估构件在弯矩作用下的承载能力与变形特性,为钢结构厂房、桥梁工程及装备制造领域提供关键安全数据。该技术不仅可预防建筑坍塌等重大事故,还能优化结构设计降低20%-35%的冗余建材用量,实现安全性与经济性的双重突破。尤其在装配式建筑普及和风电叶片大型化趋势下,其核心价值体现在全生命周期质量管控体系的构建。
多模态传感融合检测技术原理
基于应变-位移耦合理论,现代抗弯荷载检测系统采用分布式光纤传感与数字图像相关技术(DIC)的协同工作机制。通过布设在试件表面的400-1200个微应变计,配合10μm级精度的三维光学测量,可实时捕获荷载作用下试件的应变场分布与挠度变化特征。值得关注的是,基于机器学习的荷载分布模拟技术突破传统点式测量的局限,实现全场应力的可视化重构。中国计量院验证数据显示,该技术体系可将弯曲刚度测算误差控制在±1.8%以内,显著优于行业标准要求的±5%阈值。
全流程数字化检测实施方案
标准化检测流程涵盖三个阶段:预处理阶段通过三维激光扫描建立试件数字孪生模型,智能布点算法优化传感器网络布局;加载阶段采用电液伺服控制系统实现0.1kN/s的精准荷载施加,同步采集2000Hz高频动态数据;后处理阶段通过云平台进行大数据分析,自动生成包含极限荷载、塑性变形拐点等28项参数的检测报告。某高速铁路箱梁检测项目实践表明,该流程使单件检测效率提升40%,同时通过区块链技术实现检测数据的不可篡改存证。
典型行业应用场景解析
在风电领域,某5MW风机叶片检测项目采用阶梯式加载方案,成功定位叶根部位0.3mm的微裂纹扩展,避免潜在断裂风险。桥梁工程中,杭州湾跨海大桥定期检测通过布设1600个监测点,建立弯扭组合荷载下的剩余寿命预测模型。更为典型的是航空制造业,C919机翼静力试验采用多点协调加载系统,在140%设计荷载下验证结构完整性,其检测数据精度达到ASME标准三级认证要求。
四维质量保障体系构建
行业领先企业已建立涵盖"标准-人员-设备-方法"的全要素质控网络。检测标准严格执行GB/T 50263-2024《建筑结构检测技术标准》与ASTM E2309双重规范,实验室通过 能力验证项目18项。人员资质方面实施分级认证制度,检测工程师需累计完成200小时仿真训练与50个实体项目实操。设备管理采用智能物联系统,力值传感器每48小时自动进行溯源校准,确保测量不确定度≤0.5%。
技术演进与行业协同展望
随着数字孪生技术与5G通信的深度应用,建议行业重点推进三方面发展:其一构建跨区域检测大数据平台,实现全国范围的结构安全预警网络;其二开发基于BIM的智能检测机器人,将传统检测效率提升300%;其三建立材料-设计-检测联动的标准体系,特别是在新型复合材料领域加快制定弯剪耦合荷载检测规范。只有通过技术革新与制度完善的双轮驱动,方能实现工程安全从被动防护到主动预防的范式转变。
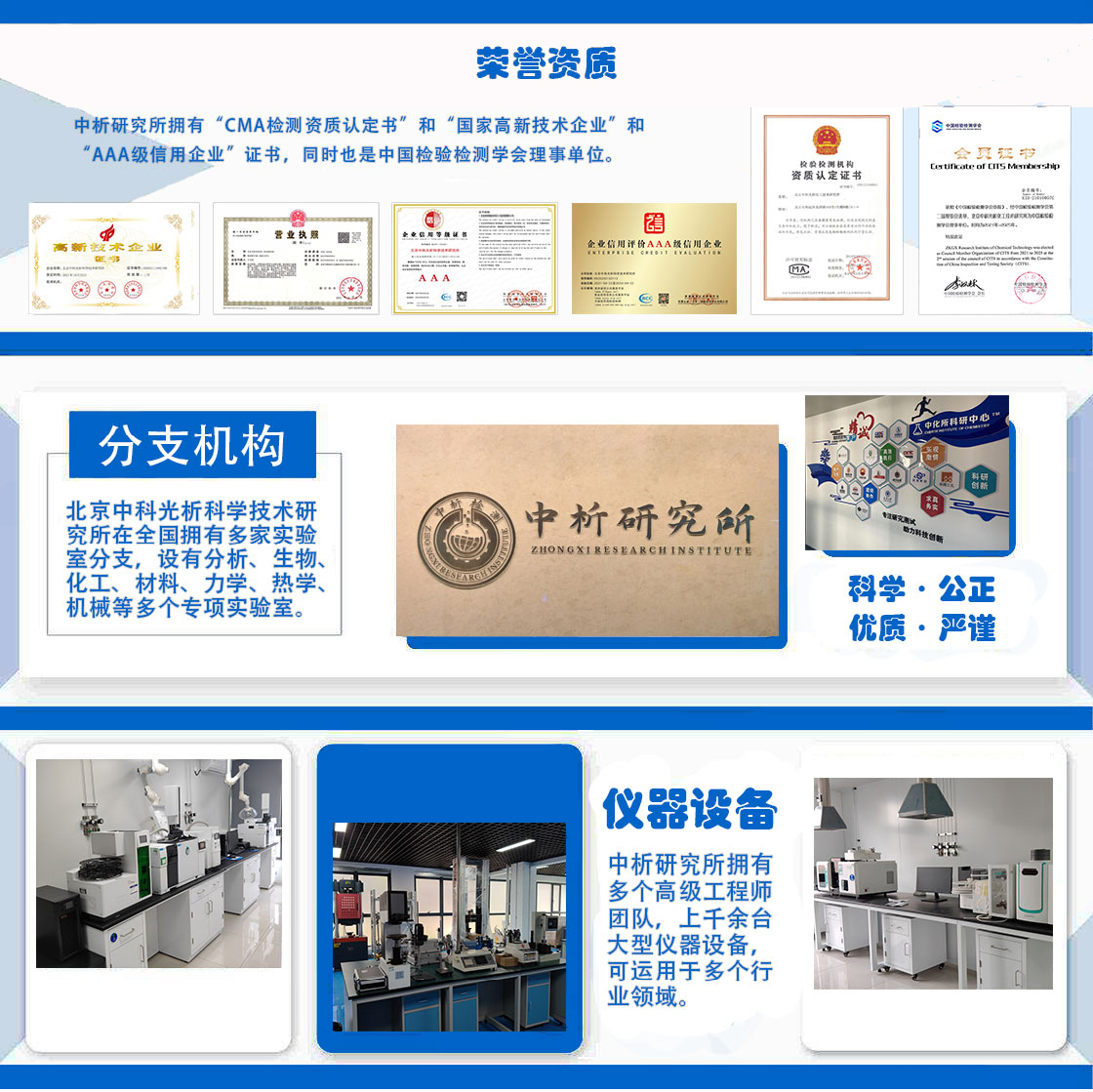
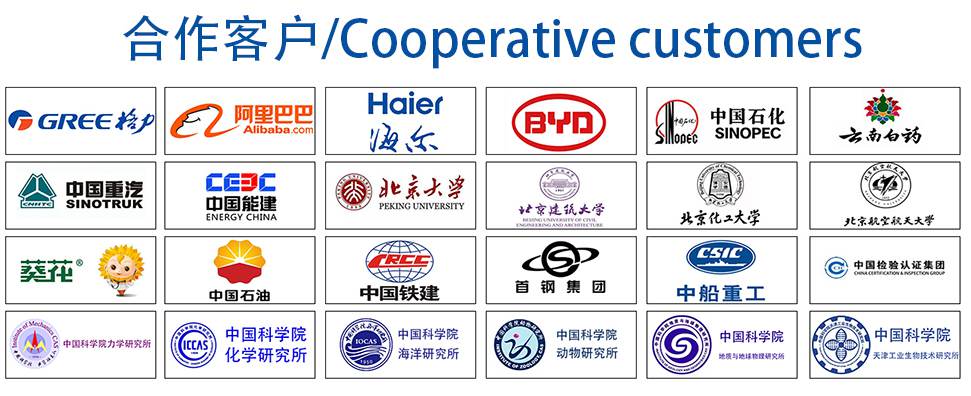