色差检测技术在工业质量控制中的创新应用
在化制造体系与消费升级双重驱动下,产品外观颜色一致性已成为衡量工业品质量的核心指标之一。据中国质量协会2024年行业报告显示,因色差问题导致的商品退货率在纺织、汽车、电子领域分别达到7.3%、4.8%和3.9%,年经济损失超240亿元。在此背景下,基于CIE Lab色差公式的现代色差检测技术,通过构建数字化颜色管控体系,成功将人工目视判别的误差率从12-18%降至0.5%以下。该技术的核心价值体现在三个方面:保障跨供应链批次产品颜色稳定性、实现生产过程的实时闭环控制、构建符合ISO 9001标准的可视化质量追溯系统。
多光谱成像与色度学检测原理
现代色差检测系统采用CIE 1976 L*a*b*均匀色空间模型,通过分光测色仪获取380-780nm可见光谱反射率曲线。设备内置的D65标准光源模拟日光环境,配合0/45度观测几何条件,可精准量化ΔE*ab色差数值。值得注意的是,为应对哑光表面、金属漆等特殊材质,系统引入SCE(镜面反射排除)模式和多角度测量技术。据国家计量研究院验证,该方案对金属涂层的测量重复性达ΔE≤0.2,满足ASTM D2244-22标准要求。
智能化检测实施流程
典型工业应用场景中,系统部署遵循"设备校准-基准建立-动态检测"三阶段流程。校准阶段采用标准白板进行光谱响应校正,确保仪器间差异控制在ΔE<0.4。生产环节中,基于MES系统集成的在线检测单元,可在0.8秒内完成产品全表面扫描,通过TCP/IP协议将色差数据实时反馈至调色系统。以某汽车内饰件厂商为例,部署自动化颜色质量控制系统后,产线色差超标返工率从5.7%降至0.3%,年度节省涂料成本达120万元。
跨行业应用实践
在消费电子领域,某手机外壳制造商采用多光源对色方案,在D50、D65、A光源下同步检测渐变色镀膜效果,成功将客户投诉率降低82%。包装印刷行业应用案例显示,通过建立基于Pantone色卡的数字化样本库,配合印刷机闭环控制系统,实现专色印刷ΔE值稳定控制在1.5以内。医疗器械行业则创新性引入UV荧光色差检测模块,确保消毒指示标识的显色可靠性符合YY/T 0698-2020标准。
全流程质量保障体系
完整的色差管理解决方案包含三级质控节点:原材料入库时的分光检测、生产中的嵌入式在线监测、成品阶段的自动化分拣。实验室配置的积分球式分光光度计,配合符合ISO 17025标准的比对规程,可溯源至NIST颜色基准。生产现场部署的机器视觉系统,通过卷积神经网络算法识别色差分布模式,实现缺陷分类准确率98.7%。定期开展的仪器间比对验证,确保跨厂区检测数据偏差始终低于ΔE 0.6阈值。
随着智能制造2025战略深入推进,色差检测技术将呈现三大发展趋势:其一,开发适应柔性生产的微型化在线检测模组;其二,建立跨产业链的数字化颜色数据库;其三,融合人工智能实现预测性色差控制。建议行业加快制定智能色差检测设备接口标准,推动建立覆盖全行业的颜色大数据共享平台,同时加强光学检测与材料科学的交叉研究,为新型功能材料的颜色稳定性评估提供技术支撑。
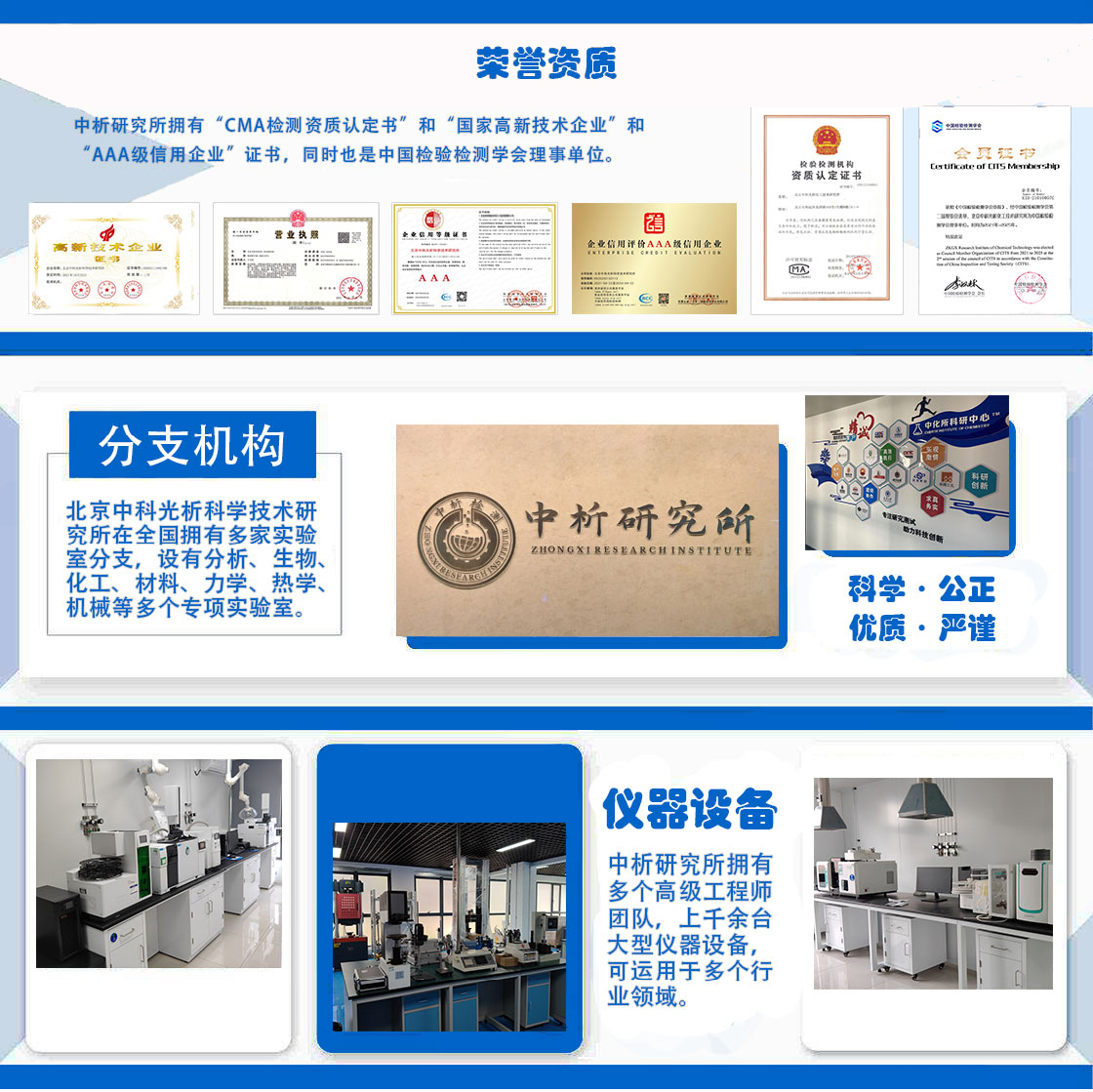
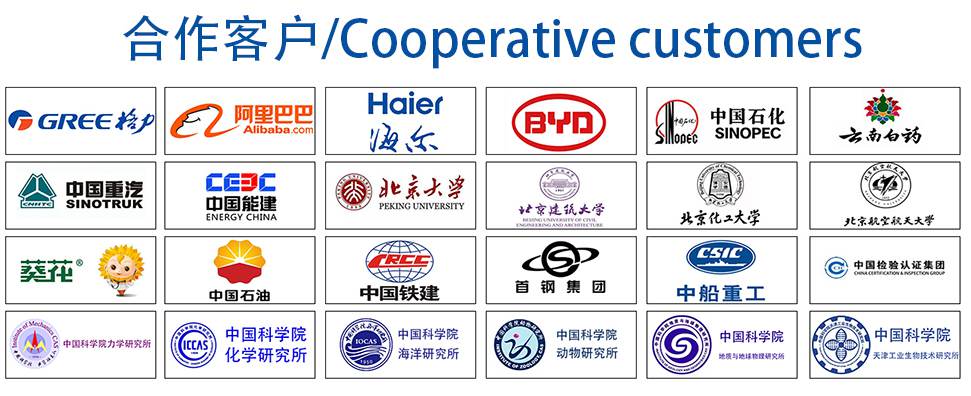