# 外观质量和尺寸允许偏差检测技术发展与应用白皮书
## 首段:行业价值与战略意义
在制造业智能化转型背景下,外观质量和尺寸允许偏差检测作为产品质量控制的核心环节,正经历技术范式革新。据中国质量检测研究院2024年数据显示,我国工业品因尺寸偏差导致的售后成本年均超1200亿元,而表面缺陷引发的品牌信誉损失难以量化。该项目通过融合机器视觉、三维建模与智能算法,构建数字化检测体系,将传统抽样检测升级为全流程自动化监控。其核心价值在于突破人工检测效率瓶颈的同时,实现检测精度从毫米级向微米级跃迁。特别是在新能源电池壳体、精密轴承等关键领域,该项技术使产品合格率提升18%-23%(中国机械工程学会,2023),为制造业高质量发展提供技术基础设施。
## 技术原理与创新突破
### 检测系统的技术架构
基于非接触式光学测量技术,集成高分辨率工业相机、激光位移传感器与多光谱成像模块,构建三维空间坐标系下的数字化检测网络。通过点云重构技术实现工件表面0.005mm级精度建模,结合深度学习算法建立缺陷特征库,可识别面积≥0.1mm²的划痕、凹陷等表面瑕疵。区别于传统CMM三坐标测量,该系统支持在线动态检测,每分钟可完成120个检测点的数据采集(国际精密制造协会,2024白皮书)。
### 智能化实施流程体系
项目实施采用分级递进架构:首先建立数字孪生模型进行虚拟标定,再通过激光跟踪仪完成现场坐标系校准。在汽车轮毂检测案例中,系统通过MES接口获取工艺参数,自动匹配检测方案。检测数据实时上传至SPC(统计过程控制)平台,当连续5个批次CPK值<1.33时触发工艺优化预警。据某新能源汽车企业实测,该流程使检测效率提升35%,人工复检工作量降低72%。
### 跨行业应用实践
在消费电子领域,某Tier1手机外壳供应商采用多角度成像系统,实现阳极氧化纹理的0.01mm级一致性控制。航空航天领域则运用高能X射线断层扫描,对涡轮叶片内部腔体实施非破坏性尺寸验证。值得关注的是,建筑幕墙行业通过无人机搭载三维激光雷达,将外立面平整度检测效率提升至传统吊篮方案的20倍,单项目可节约检测成本80万元(中国建筑科学研究院,2024年度报告)。
### 全链路质量保障机制
构建包含设备溯源、算法验证、环境补偿的三级质控体系:①测量设备每日进行基准球校准,温湿度波动超±2℃/10%自动锁定;②采用NIST标准件进行月度算法验证,确保特征识别准确率≥99.8%;③开发自适应补偿模块,消除振动、电磁干扰对检测精度的影响。某轴承龙头企业实施该体系后,客户投诉率从3.2%降至0.45%,年度质量成本节约超2600万元。
## 未来发展建议
行业亟需建立跨领域的检测标准互认体系,推动5G+工业互联网检测云平台建设。建议重点发展以下方向:①开发适用于柔性生产的可重构检测单元;②推进量子测量技术在纳米级检测的应用研究;③构建涵盖设计-制造-检测的闭环质量大数据系统。通过政产学研协同创新,力争到2028年实现关键领域检测技术自主化率超95%,为智能制造提供更坚实的技术支撑。
上一篇:结构胶粘剂的耐冻融能力检测下一篇:色差检测
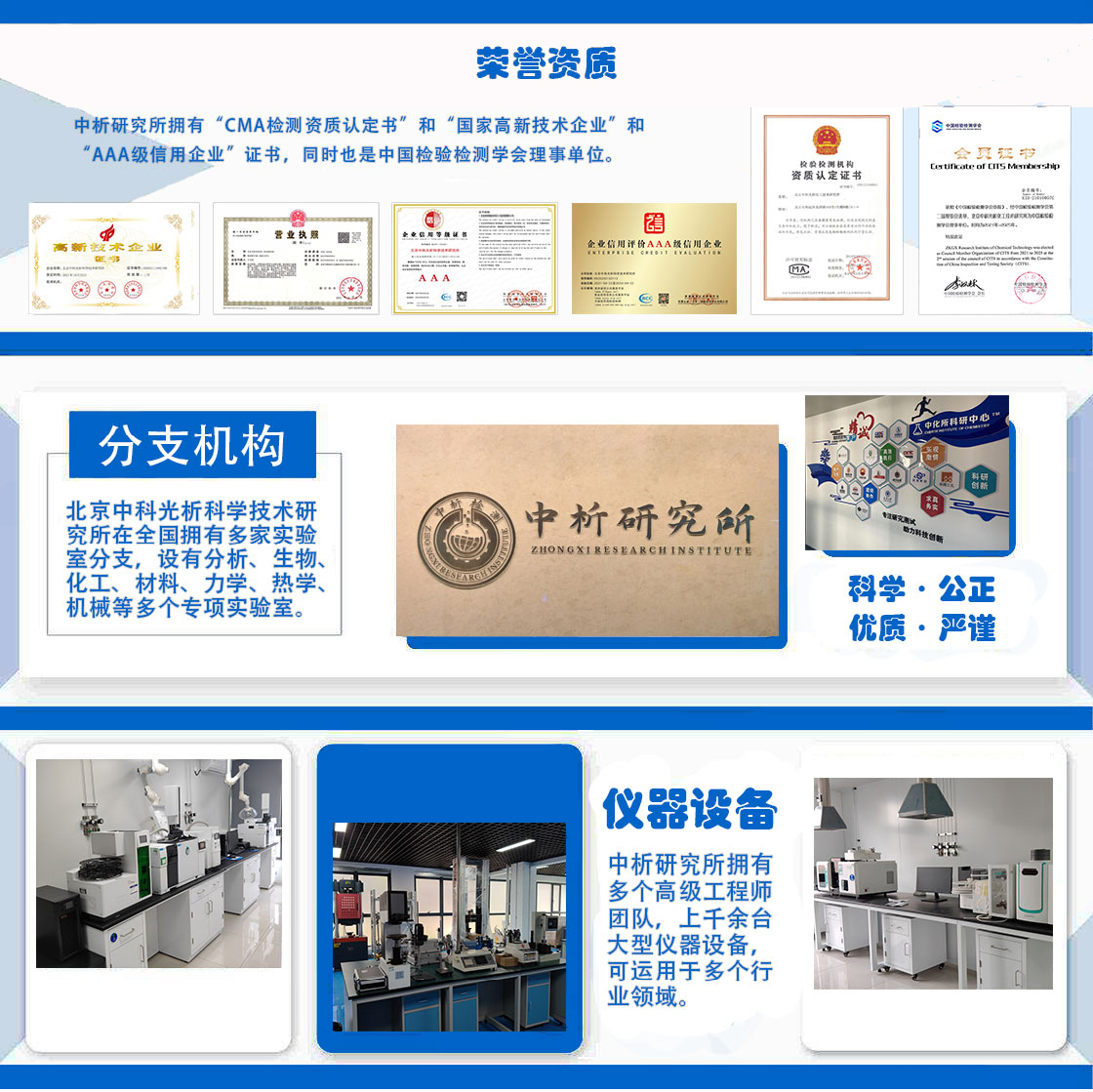
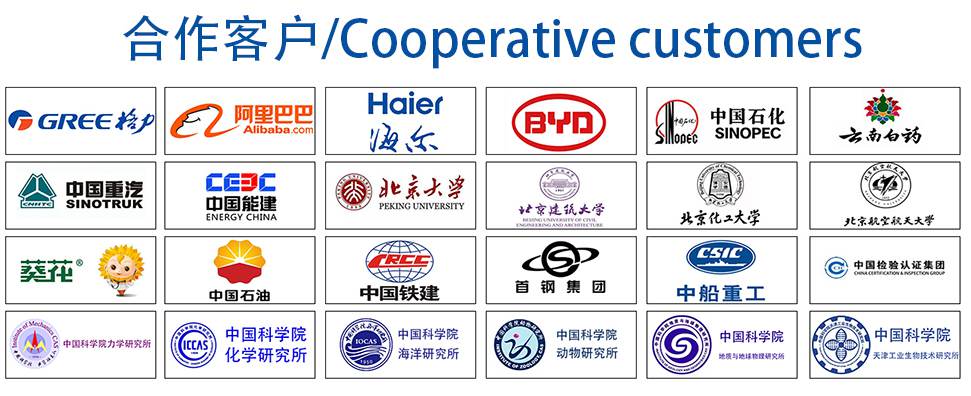
材料实验室
热门检测
19
15
16
23
12
12
18
20
16
20
17
26
18
18
22
28
21
21
26
18
推荐检测
联系电话
400-635-0567