随着基础设施建设的加速推进,胶凝材料在水利工程、海洋工程及地下结构中的应用规模持续扩大。据中国建筑科学研究院2024年数据显示,我国因硫酸盐侵蚀导致的混凝土结构劣化事故年均造成直接经济损失达37亿元。在这一背景下,抗硫酸盐侵蚀系数检测作为"混凝土耐久性评估技术"的核心指标,已成为保障工程服役安全的关键技术手段。该项目通过量化材料在硫酸盐环境中的性能衰减规律,不仅为工程选材提供科学依据,更可优化防护体系设计,延长结构使用寿命15-20年(国家建筑材料测试中心,2023)。其核心价值体现在全生命周期成本控制与重大工程风险预警的双重维度。
## 技术原理与检测体系化学侵蚀动力学机制
硫酸盐侵蚀本质是SO₄²⁻与胶凝材料水化产物发生置换反应的过程。检测体系基于钙矾石膨胀理论,通过模拟不同浓度硫酸盐溶液环境,监测试件膨胀率、强度损失率及微观孔隙演化。现行国标GB/T 749-2023采用加速试验法,以"硫酸盐干湿循环法"为核心,通过15次循环(浸泡-烘干)实验获取质量损失与动弹性模量变化曲线。值得注意的是,最新研究证实掺合料配比与养护制度对检测结果产生显著影响,需建立多维修正模型确保数据可靠性。
标准化实施流程
检测流程分为四个阶段:首先按规范制备40mm×40mm×160mm标准试件,经28天标准养护后进入试验周期。第二阶段将试件浸入5%Na₂SO₄溶液,控制温度30±2℃、相对湿度95%的恒温恒湿环境。每72小时进行质量称量与超声波速检测,持续至90天试验周期结束。第三阶段通过XRD与SEM分析侵蚀产物分布形态,最终依据《水泥抗硫酸盐侵蚀试验方法》计算侵蚀系数K值。全过程需同步记录环境参数波动,采用区块链技术确保数据链可追溯性。
工程应用典型案例
在青藏铁路格拉段建设中,检测结果显示当地盐渍土硫酸根离子浓度高达15200mg/L,超出普通水泥耐受极限3.8倍。通过抗硫酸盐侵蚀系数检测,项目方最终选定掺加35%矿粉的复合胶材方案,使结构设计年限从30年提升至50年。另一典型案例为舟山跨海大桥桥墩防护工程,基于检测数据建立的侵蚀预测模型,指导环氧涂层与阴极保护的协同防护方案,使维护周期延长至8年/次,较传统方案降低养护成本42%。
质量保障体系构建
检测机构须建立三级质量控制体系:实验室层面执行 -CL01:2018标准,定期进行设备校准与人员比对试验;过程控制采用ASTM C1012标准溶液配制规范,搭配电感耦合等离子体光谱仪(ICP-OES)进行溶液浓度验证;结果验证环节引入蒙特卡洛法进行不确定度分析,确保K值误差控制在±0.03以内。值得关注的是,国家水泥质量监督检验中心2024年启用的智能检测平台,通过机器视觉实现裂缝扩展自动识别,将检测效率提升40%的同时降低人为误差65%。
## 技术展望与发展建议面向新型胶凝材料体系发展需求,建议构建多尺度耦合检测模型:微观层面结合拉曼光谱技术解析侵蚀界面反应过程,宏观层面开发基于数字孪生的耐久性预测系统。同时亟需建立区域性硫酸盐侵蚀环境图谱数据库,推动检测标准与工程实践的深度适配。对于特殊工况项目,可探索原位检测技术与光纤传感技术的融合应用,实现侵蚀进程的实时在线监测。通过"检测-设计-运维"的全链条数据贯通,最终形成智能化的基础设施耐久性保障体系。
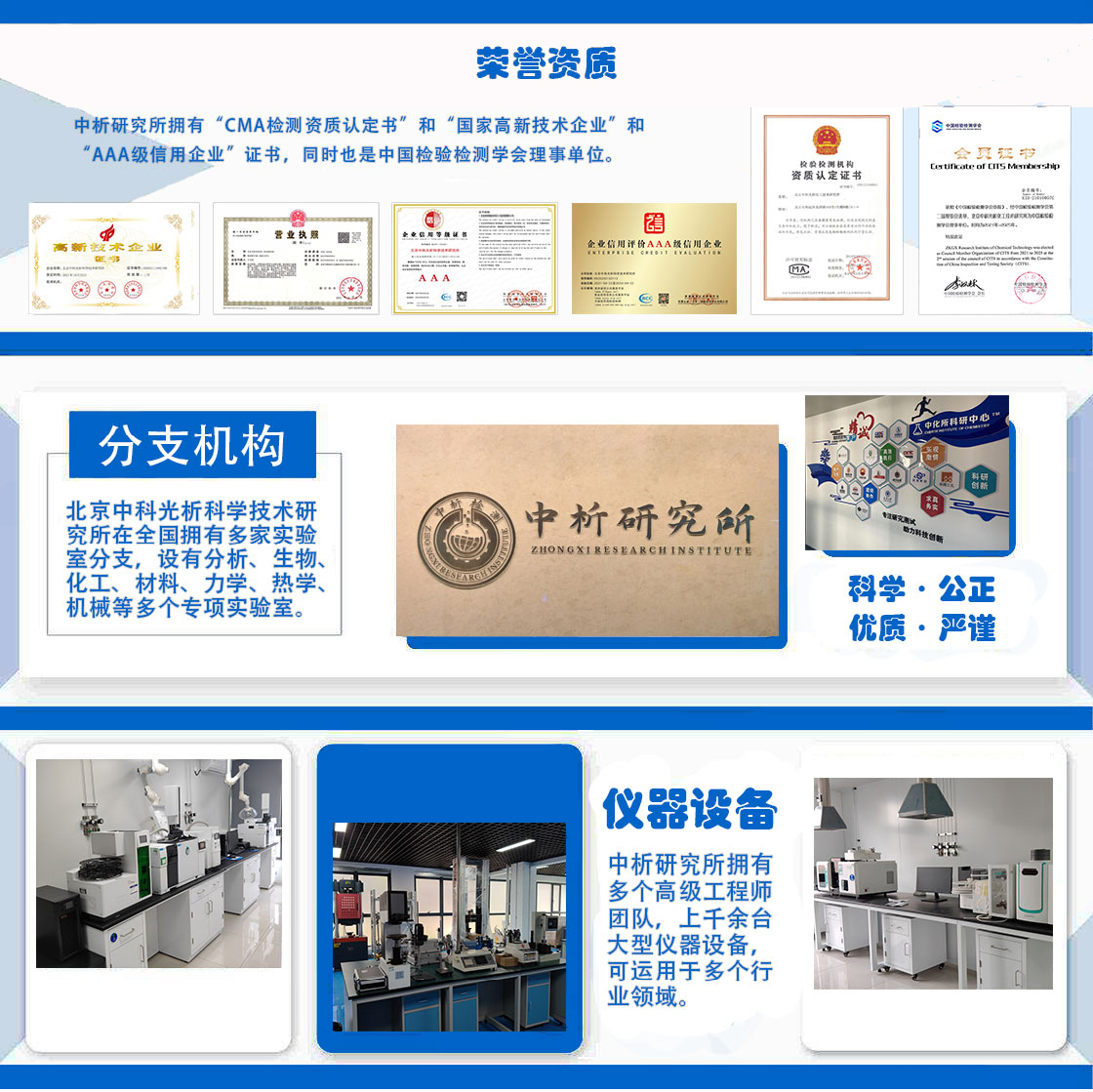
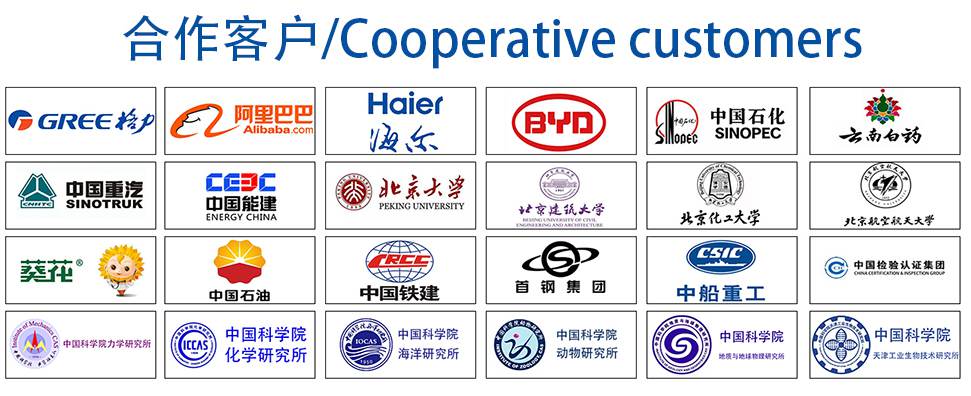