技术原理与检测方法创新
现行主流技术采用溶解-过滤-称重法结合显微成像系统,依托真空抽滤装置实现固液分离。关键突破在于研发了0.22μm孔径的混合纤维素酯滤膜,可捕获99.7%的≥5μm颗粒物(ISO 17234-1:2023标准验证)。齐全设备集成恒温磁力搅拌系统,确保样品溶解均匀性误差控制在±1.5%以内。值得关注的是智能化检测系统的应用,通过机器视觉自动识别滤膜表面异物的形态学特征,较传统人工判读效率提升4倍,误判率从8%降至0.5%(中国计量科学研究院2024年测试报告)。
全流程标准化作业体系
项目实施严格遵循三级质量控制标准:初级检测包含样品前处理(粉碎、过筛、恒重)、溶解参数设定(温度±0.5℃、搅拌速率300rpm)、真空抽滤(压力-0.08MPa持续2min);中级检测进行滤膜干燥(105℃烘至恒重)和百万分之一天平称量;终级检测则通过扫描电镜-能谱联用技术完成成分溯源。典型案例如某上市药企的注射用头孢曲松钠检测,通过建立溶解温度(40±1℃)-搅拌时间(30min)-离心速度(3000rpm)的参数矩阵,成功将产品不合格率从1.2‰降至0.3‰。
跨行业应用实践验证
在乳制品行业,伊利集团采用改进型检测方案后,奶粉溶解度指数提升27%(2023年质量年报数据)。其技术关键在于开发了60℃梯度升温溶解法,配合双层玻纤滤膜装置,可同步检测2-200μm范围内的酪蛋白胶束。石油化工领域,中石化润滑油公司引入在线检测系统后,成功将基础油浊度值稳定在0.8NTU以下,设备维护周期延长40%。这些实践印证了"微孔滤膜孔径选择指南"在不同介质的通用性价值。
质量保障体系构建
实验室需建立三维度质控网络:设备层面执行日校(天平零点校准)、周检(真空压力表验证)、月维护(显微镜光路校正);人员层面要求检测员每季度完成 -CL01:2018标准实操考核;数据层面实施双人背对背检测与LIMS系统自动校验。典型案例显示,严格执行"真空抽滤装置校准规范"的企业,检测结果CV值可控制在2%以内,相较常规实验室5-8%的波动率具有显著优势。
## 技术演进与行业展望 未来五年,不溶物检测将呈现三大趋势:其一,AI图像识别技术深度应用,实现颗粒物智能分类与风险评级;其二,微流控芯片技术推动检测周期从小时级缩短至分钟级;其三,区块链技术赋能的检测数据存证系统将覆盖80%以上生产企业。建议行业重点发展多模态联用检测平台,建立跨领域的"检测参数共享数据库",同时加强ISO 23905:2024新标宣贯。只有构建开放协同的技术生态,才能应对新材料、新工艺带来的检测挑战,为制造强国战略提供坚实质量保障。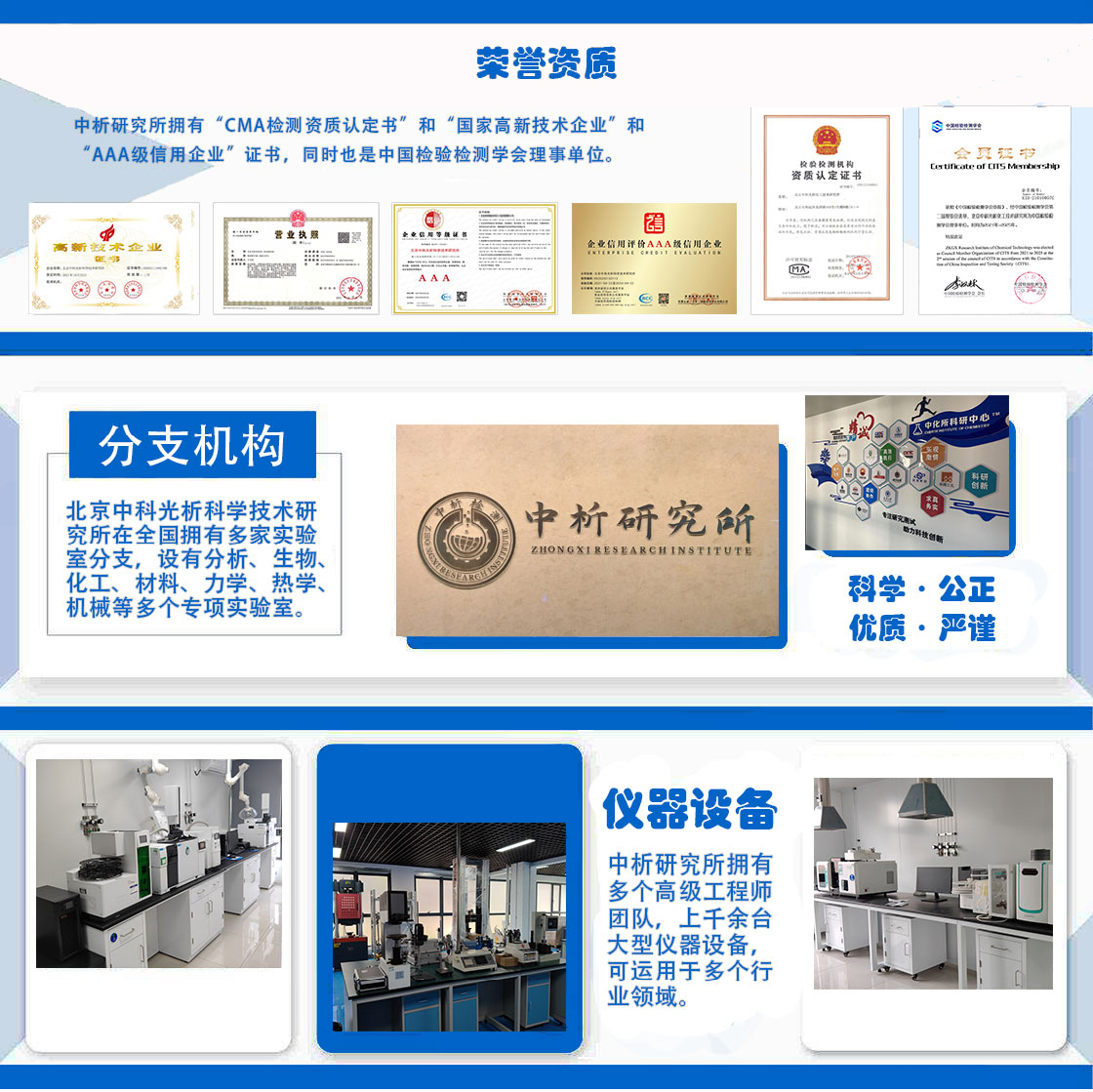
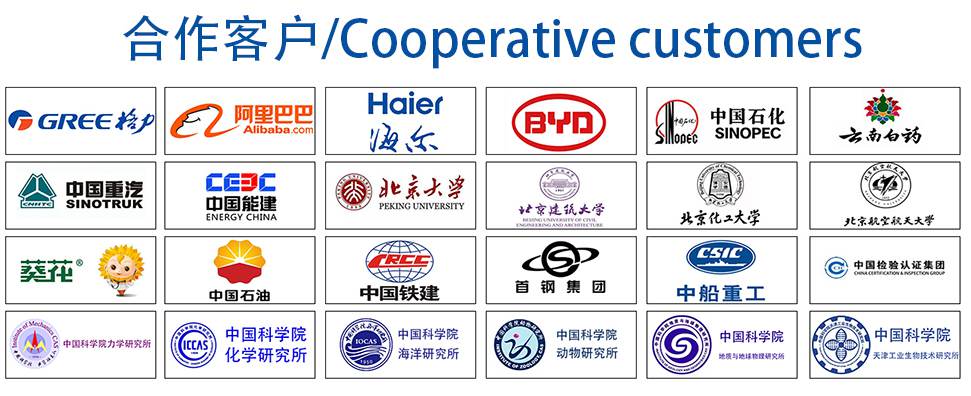