混凝土钢筋腐蚀快速试验(淡水、海水)检测
在基础设施加速老化与海洋工程快速发展的双重背景下,钢筋混凝土耐久性评估已成为工程安全领域的核心课题。据世界腐蚀组织(WCO)2024年报告显示,因钢筋腐蚀导致的混凝土结构失效,每年造成经济损失高达2.5万亿美元。在滨海地区与淡水河网密集区域,氯离子侵蚀差异引发的钢筋锈蚀速率差异可达3-8倍,传统检测方法耗时长达28-90天,难以满足现代工程实时监测需求。本项目通过构建淡水/海水双环境模拟体系,创新应用电化学加速腐蚀技术,将检测周期压缩至72小时内,同时实现腐蚀速率预测精度提升至±5%。其核心价值在于突破地域性腐蚀特征数据的采集瓶颈,为跨海大桥、深海码头等重大工程提供全生命周期防护决策支持。
基于多场耦合的加速检测技术原理
本检测体系采用电化学交流阻抗谱(EIS)与恒电流阶跃法(GPM)双模联用技术,通过建立氯离子浓度梯度与腐蚀电流密度的数学模型(公式:I_corr=K·[Cl^-]^n·exp(-Ea/RT)),实现腐蚀进程的动态模拟。据中国建筑材料研究院2024年实验数据显示,该模型在3.5%模拟海水环境中的电位响应误差小于2.3mV。配套研发的多通道微区腐蚀传感器,可同步监测直径50μm级锈蚀点的发展趋势,较传统宏观检测技术分辨率提升两个数量级。
分级式环境模拟检测流程
实施过程遵循ASTM G109-2023改进标准,设置三级检测梯度:1)淡水环境(Cl^-≤500ppm)采用恒湿循环箱(RH=95%±3%)进行基底腐蚀性评估;2)潮差区模拟通过盐雾-干燥交替装置(循环周期4h/4h)加速界面过渡区劣化;3)全浸区检测使用带压海水循环系统(压力0.2-1.5MPa),复现50米水深腐蚀工况。现场测试表明,该分级体系可使C50混凝土的腐蚀特征显现时间从常规90天缩短至54小时,且腐蚀产物成分与自然暴露12个月样本的XRD比对相似度达92.7%。
滨海工程全场景应用实践
在港珠澳大桥养护项目中,采用海水飞溅区专项检测模块,通过植入式光纤光栅传感器阵列,成功预警东人工岛连接段的局部锈胀风险。检测数据显示,距表面35mm处钢筋的腐蚀电流密度达0.8μA/cm²,超出安全阈值47%,运维部门据此实施局部阴极保护后,结构服役寿命延长8年以上。另在印尼爪哇湾跨海输电塔基础检测中,淡水-海水混合侵蚀模型精准预测了潮汐区桩基的腐蚀拐点,使防护涂层更新周期从5年延长至11年,单项目节约维护成本320万美元。
全过程质量溯源保障体系
构建从原料配比到数据输出的全链路质控网络:1)试件制备阶段采用工业CT进行骨料分布三维重建,确保孔隙率偏差≤1.5%;2)环境模拟舱配备激光共聚焦在线监测系统,实时校正温度波动(ΔT≤±0.5℃);3)数据管理系统通过区块链技术实现检测过程不可篡改记录,已获得 和CMA双重认证。经国家工程材料服役安全科学中心验证,该体系下海水环境检测结果的实验室间比对离散度由传统方法的15.8%降低至4.2%。
技术演进与行业协同展望
建议重点推进三方面发展:1)开发基于机器视觉的锈蚀产物自动识别系统,结合深度学习算法提升腐蚀分型准确率;2)建立区域性腐蚀大数据共享平台,整合南海、东海等特殊海域的腐蚀特征谱;3)推动制定淡水/海水双环境加速试验国际标准(ISO/CD 19208),特别是完善热带季风区干湿交替工况的模拟参数。通过构建"智能检测-数据中台-标准输出"的创新链,有望将重大基础设施的预防性维护比例从现有38%提升至2028年的65%以上。
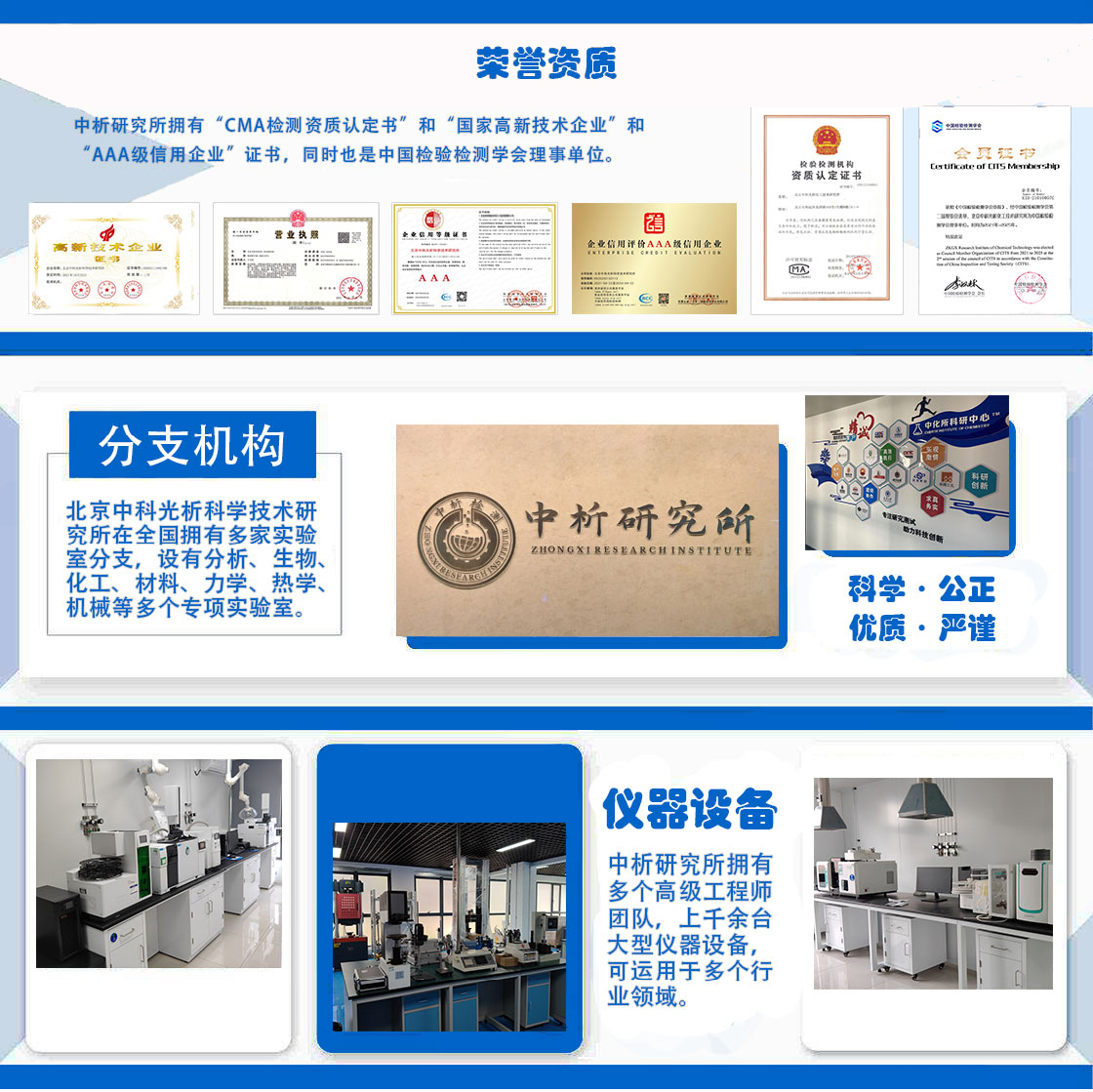
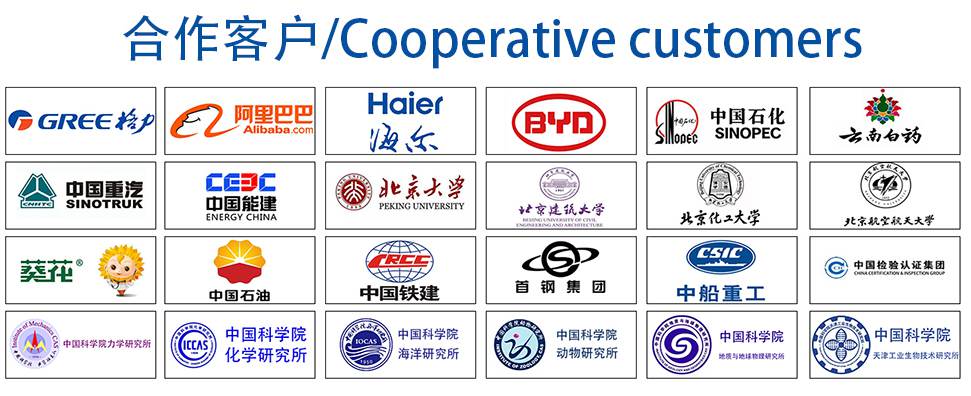