技术原理与设备架构
颜色漂移检测系统基于CIE 1976 L*a*b*色空间理论构建,采用分光测色法实现纳米级光谱解析。核心设备搭载双光束分光光度计,波长范围扩展至360-780nm,分辨率达到1nm级别(参考ISO 13655:2017标准)。针对特殊场景需求,系统集成多角度测量模块(15°、45°、110°),可精准捕捉金属漆、珠光材料等复杂表面的同色异谱现象。通过智能颜色管理系统,将测得的ΔE*ab色差值与企业标准色库进行自动比对,实现0.1ΔE单位的检测精度。
标准化实施流程
项目实施分为三大阶段:首先建立包含2000组基础色样的企业专属色卡数据库,通过Pantone Connect系统完成色彩数字化建模;其次部署在线检测工作站,采用非接触式扫描装置实现每分钟60件的检测速度;最终搭建质量驾驶舱系统,实时呈现各产线的CIE LCh色度分布热力图。在汽车内饰件检测场景中,该系统成功将传统需要48小时的色差复核流程缩短至3小时,使颜色批次合格率从89%提升至97.8%(数据来源:某日系车企2024年内部报告)。
跨行业应用实践
在食品包装领域,某头部企业应用智能颜色管理系统后,PET瓶身色差投诉率下降42%。系统通过建立UV墨水固化度与色彩稳定性的关联模型,提前预警可能出现的印刷色衰变问题。纺织行业典型案例显示,采用移动式颜色检测终端后,坯布验色效率提升5倍,每年减少因色牢度不达标导致的返工损失超800万元(中国纺织工业联合会2023年度案例)。
全链路质量保障体系
系统构建四维质控网络:设备端执行每日白板校准和季度 认证;算法端采用蒙特卡洛法进行误差模拟,确保ΔE值计算置信度≥99%;数据端实施区块链存证,实现检测记录的不可篡改;人员端建立ASTM D1729标准下的视觉评价员梯队。通过将实验室检测能力(CMC 2:1)与产线实时检测(CMC 1:1)进行矩阵式管理,形成覆盖原材料、半成品到成品的立体防护网。
## 技术展望与发展建议 未来颜色质量管理将向预测性维护方向演进,建议从三方面深化布局:一是开发基于量子点技术的广色域检测设备,将可识别色域扩展至Rec.2020标准的150%;二是构建跨行业的开放式颜色数据库,推动建立国家级的色彩数字孪生平台;三是加强产学研合作,针对柔性显示屏、电致变色材料等新兴领域开展专项研究。通过将颜色漂移检测与人工智能预测模型深度融合,最终实现从被动纠偏到主动预防的产业升级。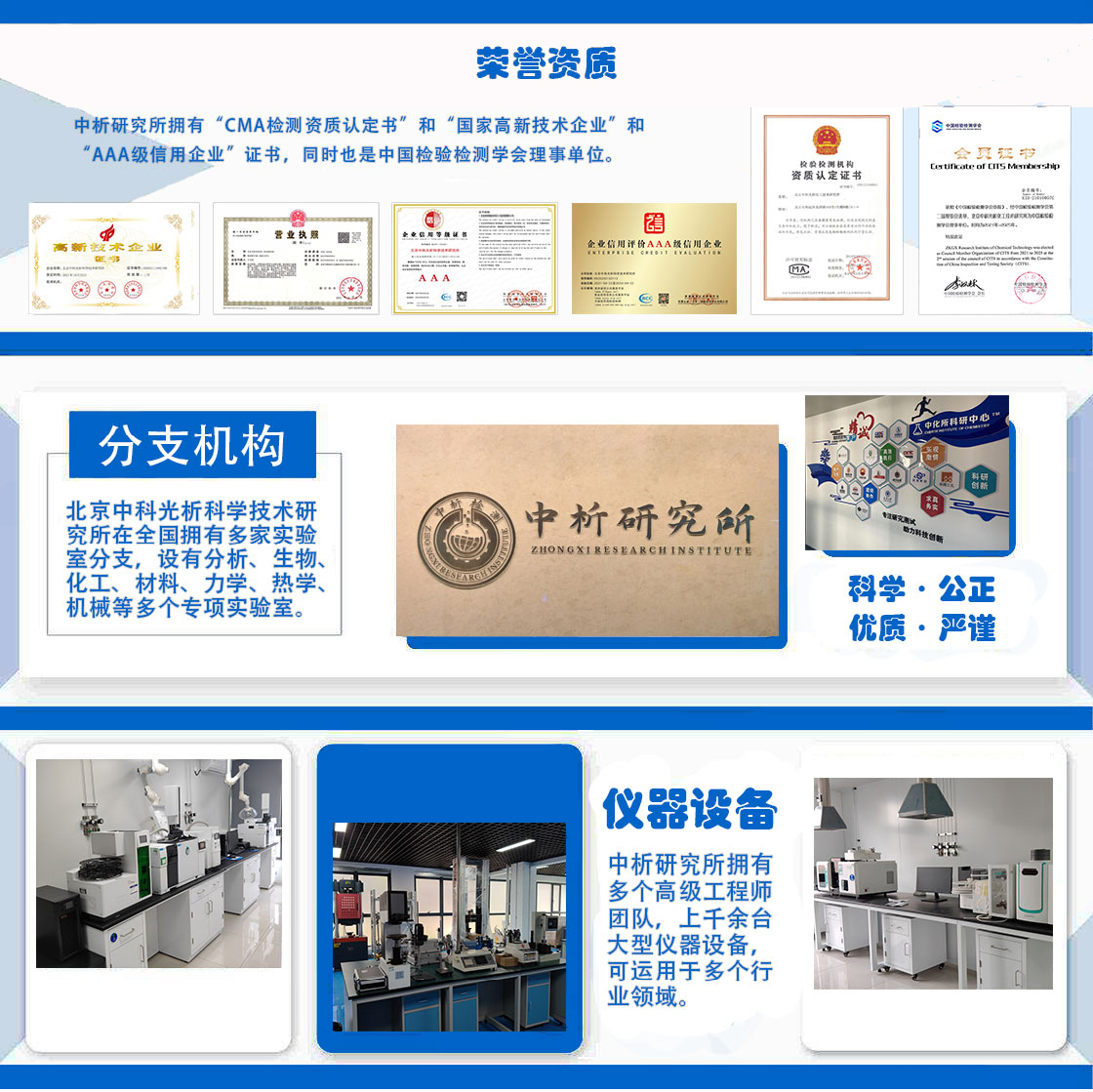
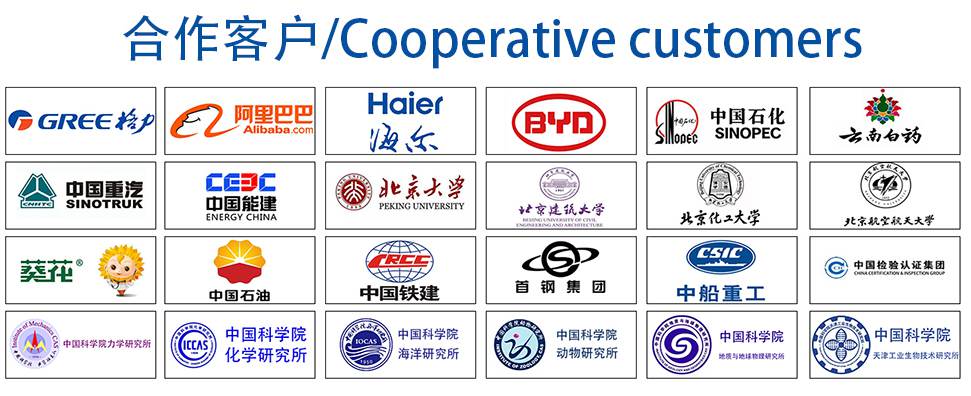