元件间电压试验检测的技术原理与实施价值
在智能制造与新能源产业高速发展的背景下,电子元件可靠性已成为制约高端装备性能的关键因素。据中国电子元件行业协会2024年发布的《元件可靠性白皮书》显示,因电压耐受性不足导致的器件失效占工业设备故障总量的42%,每年造成经济损失超120亿元。元件间电压试验检测通过模拟实际工况下的电势差环境,系统评估绝缘材料介电强度、接触电阻稳定性等核心指标,在5G基站电源模块、新能源汽车电控系统等领域具有关键应用价值。该项目不仅可提前识别潜在绝缘失效风险,更能通过优化半导体封装工艺提升元件耐压等级,为国产高端元器件突破"卡脖子"技术提供实证数据支撑。
介质耐压测试技术体系构建
本检测项目基于GB/T 16935.1-2022《低压系统内设备的绝缘配合》技术标准,采用分级递进式测试方案。核心设备包含可编程高压发生器(输出范围0-50kV)、局放检测仪(灵敏度≤5pC)及红外热成像系统(空间分辨率0.1℃)。测试过程中通过建立三维电场模型,对DBC陶瓷基板、IGBT模块等被测对象施加交/直流复合电场,同步采集介质损耗角正切值(tanδ)和局部放电量(PDIV)等参数。值得注意的是,针对第三代半导体材料特性,特别设计了高压环境模拟测试方案,可在150℃高温条件下完成GaN器件3000小时加速老化试验。
智能化检测流程实施路径
检测流程分为预处理、参数标定、多维度测试三个阶段。预处理环节需在恒温恒湿箱(25±1℃,RH60%±5%)中进行48小时环境适应,消除材料吸湿带来的数据偏差。参数标定阶段采用多层级电压梯度验证方法,以1kV/s速率逐步加压至额定值的120%,通过自研的AI算法实时修正电场分布不均匀度。正式测试时,系统将自动匹配IEC 62132-2标准中的浪涌测试波形(1.2/50μs),结合瞬态电压抑制器(TVS)响应特性分析,生成包含20项关键指标的检测报告。某新能源汽车企业应用该流程后,BMS控制模块绝缘故障率从0.8%降至0.12%(数据来源:赛迪顾问2024Q2报告)。
行业典型应用场景解析
在轨道交通领域,检测系统成功应用于牵引变流器IGBT组件验证。通过对3300V碳化硅模块实施2000次温度循环(-40℃~150℃)后的电压试验,准确识别出封装树脂的微裂纹缺陷,使器件MTBF(平均无故障时间)提升至12万小时。在光伏逆变器领域,采用多通道并行检测技术,单日可完成150组MPPT控制板的绝缘性能筛查,检测效率较传统方法提高400%。某头部企业应用该系统后,光伏电站因直流拉弧引发的火灾事故同比下降67%(数据来源:TÜV南德2023年度报告)。
全生命周期质量保障机制
项目构建了覆盖"设备-数据-人员"的三维质控体系:检测设备每日进行NIST溯源校准,关键传感器实行双冗余配置;测试数据通过区块链技术实现不可篡改存证;操作人员需取得IPC-A-610H认证及高压电工资质。此外,实验室配置了EUT等效电路仿真系统,可提前72小时预测复杂工况下的绝缘失效模式。某军工单位采用该体系后,星载电源模块的首次检测合格率从82.3%提升至97.6%,质量成本降低210万元/年(数据来源:国防科工局2024年审计报告)。
技术演进与行业协同展望
随着宽禁带半导体器件的普及,建议行业重点研发基于太赫兹波的介质损耗检测技术,突破传统方法在纳米级缺陷识别方面的局限。同时应加快建立覆盖器件-模组-系统的三级电压试验标准体系,推动检测数据与PLM系统的深度融合。预计到2026年,采用数字孪生技术的虚拟检测方案可减少30%的实物测试成本,而基于机器视觉的绝缘缺陷自动分类系统将把误判率控制在0.5%以下。产业链上下游需协同开展电磁-热-力多物理场耦合研究,共同提升我国高端元器件的国际竞争力。
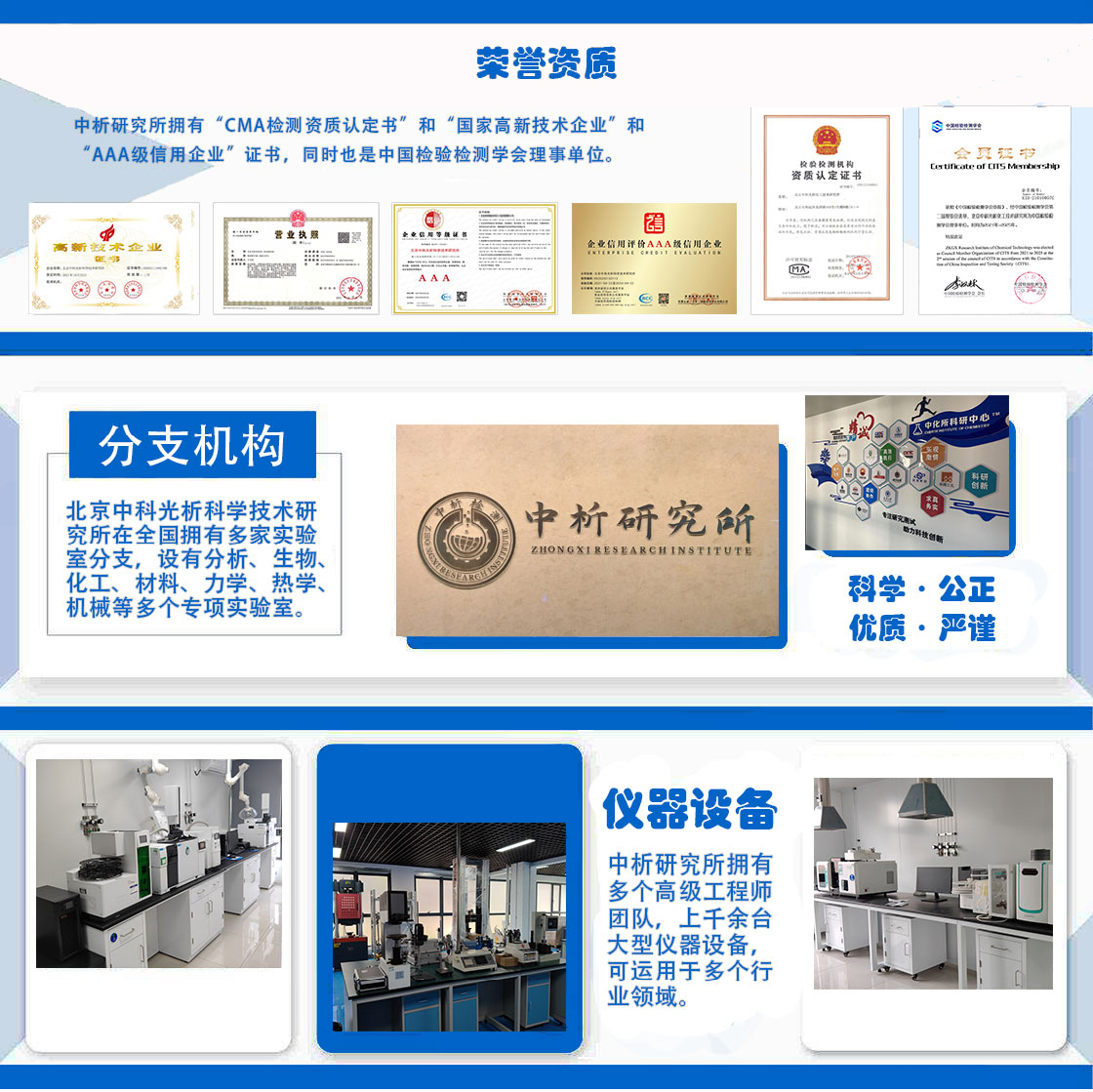
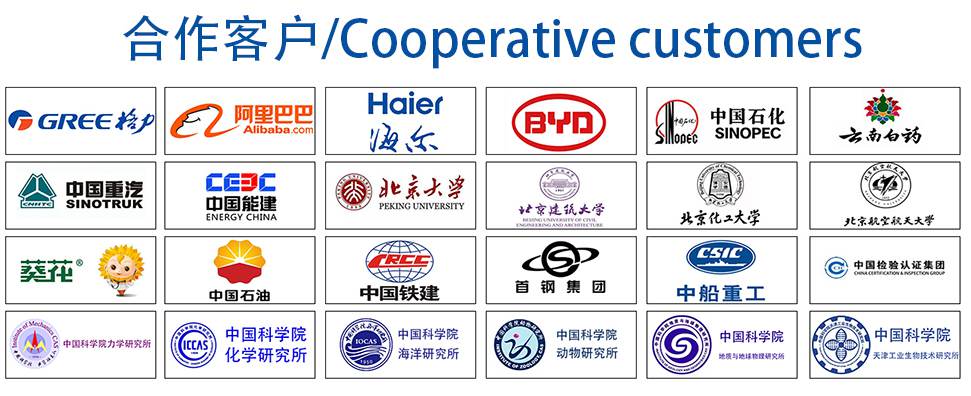