氧气(O₂)与氮气(N₂)检测技术解析
一、氧气(O₂)检测项目与技术
1. 检测项目
- 氧浓度检测:定量分析混合气体中氧气的体积百分比(% vol)或分压。
- 溶解氧(DO)检测:测定液体(如水、血液)中溶解的氧气浓度(单位:mg/L或ppm)。
- 氧纯度检测:验证高纯度氧气(如医用氧、工业氧)的杂质含量是否符合标准。
- 氧泄漏检测:监控密闭空间或管道中氧气的泄漏风险。
2. 检测方法
- 电化学传感器:通过氧化还原反应产生电流信号,检测范围0-25% vol,适用于工业安全与环境监测。
- 顺磁式分析仪:基于氧气的顺磁性,精度高(±0.1%),用于高纯度氧检测。
- 光学氧传感器(荧光法):利用荧光物质与氧的猝灭效应,适用于溶解氧实时监测。
- 激光光谱法(TDLAS):非接触式检测,抗干扰能力强,用于高温、高压环境。
3. 典型应用
- 工业过程控制:燃烧优化(锅炉、窑炉)、空分制氧系统监测。
- 医疗领域:呼吸机、麻醉机氧浓度校准,血气分析仪质量控制。
- 环境监测:水体溶解氧评估(河流、污水处理厂),密闭空间(矿井、储罐)安全检测。
二、氮气(N₂)检测项目与技术
1. 检测项目
- 氮气浓度检测:监测混合气体中氮气占比(常见于惰化保护工艺)。
- 氮气纯度检测:分析高纯氮(电子级、食品级)中残留的O₂、H₂O等杂质。
- 液氮温度与压力监控:确保低温储运系统的安全性。
- 氮氧化物(NOₓ)衍生检测:间接评估氮气转化产物(如燃烧尾气中的NO、NO₂)。
2. 检测方法
- 热导检测器(TCD):基于气体热导率差异,适合高浓度氮气(>90%)的快速测定。
- 气相色谱(GC):结合TCD或质谱检测器,精确分析氮气纯度及杂质成分。
- 红外吸收法:针对氮氧化物(NOₓ)的专项检测,灵敏度达ppm级。
- 压力-体积-温度(PVT)法:用于液氮储罐的实时状态监控。
3. 典型应用
- 食品工业:包装氮气纯度检测(防止氧化变质)。
- 电子制造:半导体生产环境中的超纯氮质量控制。
- 化工安全:反应釜惰化保护(防止爆炸),管道吹扫残留氧监测。
- 环保领域:燃煤电厂、汽车尾气中氮氧化物的排放检测。
三、检测技术对比与选型建议
参数 | 电化学法(O₂) | 顺磁式(O₂) | TCD(N₂) | 激光光谱法 |
---|---|---|---|---|
检测范围 | 0-100% vol | 0-100% vol | 0-100% vol | ppm至100% vol |
响应时间 | <30秒 | <10秒 | <1分钟 | <1秒 |
抗干扰性 | 中等 | 高 | 低 | 极高 |
典型成本 | 低 | 中高 | 中 | 高 |
适用场景 | 工业安全、环境 | 高精度实验室 | 常规气体分析 | 高温、腐蚀性环境 |
四、检测标准与规范
- 氧气检测:
- GB 8982-2009《医用及航空呼吸用氧》
- ISO 6142:2001《气体分析-校准用混合气体的制备》
- 氮气检测:
- GB/T 8979-2008《纯氮、高纯氮和超纯氮》
- EPA Method 7E(氮氧化物排放标准)
五、注意事项
- 交叉干扰:电化学传感器易受H₂、CO₂等气体影响,需定期校准。
- 温度补偿:溶解氧检测需考虑水体温度对溶解度的修正。
- 安全防护:检测液氮时需防冻伤,高氧环境需防火防爆。
- 数据合规性:工业检测需符合ISO 17025实验室认证要求。
六、未来趋势
- 微型化与物联网:MEMS传感器与无线传输技术推动远程监测网络建设。
- 多气体联检:集成式传感器实现O₂、N₂、CO₂等多参数同步分析。
- 人工智能优化:利用机器学习算法提升复杂环境下的检测准确性。
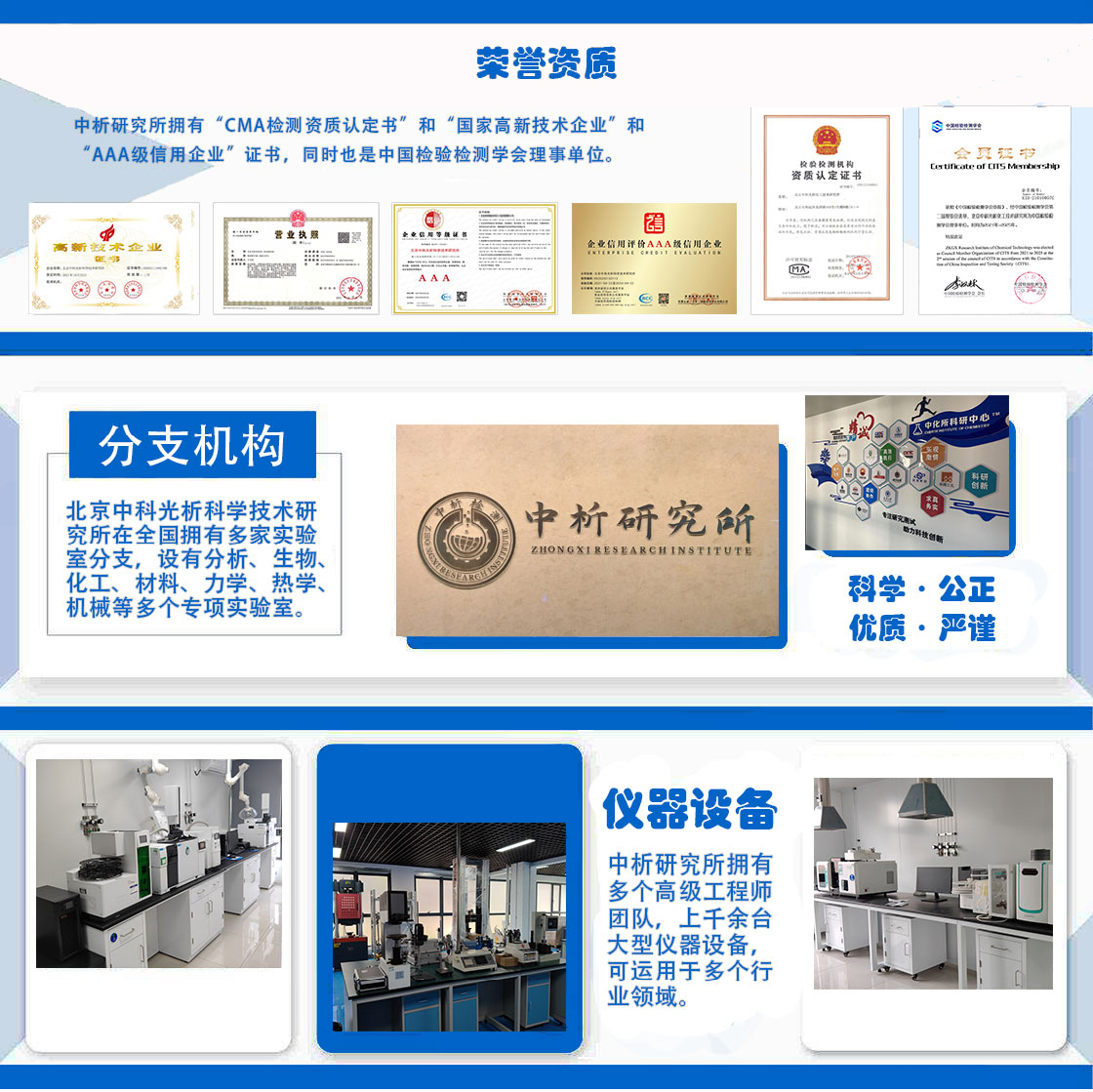
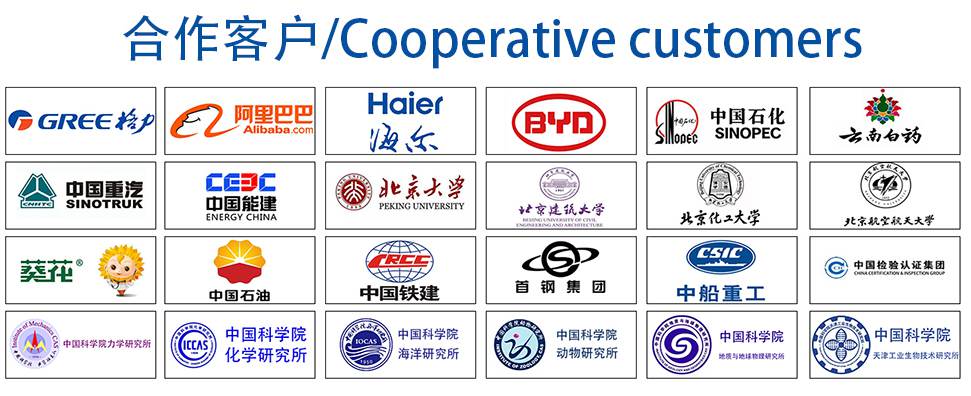
材料实验室
热门检测
256
215
191
203
198
204
210
202
208
217
204
199
204
204
198
195
210
199
209
203
推荐检测
联系电话
400-635-0567