行业背景与项目价值
随着航空运输量年均增长4.7%(据IATA 2023年报告),飞机起降架次激增对刹车系统可靠性提出更高要求。盘式刹车装置作为飞机着陆能量转化的核心部件,其性能直接影响200吨级客机在42秒内从240km/h减速至静止的制动效能。本项目通过构建多维度检测体系,实现刹车盘摩擦系数衰退监测、热裂纹预警和结构完整性评估,将维护成本降低30%以上。其核心价值在于突破传统目视检查的局限性,建立基于材料疲劳寿命模型的预测性维护机制,为保障高原机场、短跑道等高载荷场景下的起降安全提供技术支撑。
复合传感检测技术原理
检测系统采用多物理场耦合分析框架,集成涡流阵列传感器(检测深度达8mm)和红外热像仪(±0.5℃测温精度)。通过模拟着陆过程2700kJ动能加载工况,同步采集刹车盘表面温度场分布、残余应力变化及微观结构形变数据。关键创新点在于开发了碳碳复合材料各向异性传导模型,可精准解析刹车盘内部3mm级裂纹特征。该技术已通过EASA DO-160G环境适应性认证,在持续60分钟盐雾测试中保持99.3%的检测准确率。
模块化检测实施流程
标准化作业流程包含三级验证体系:一级检测采用便携式超声相控阵设备进行15分钟快速筛查;二级检测运用X射线衍射法(ASTM E915标准)测算摩擦面残余应力分布;三级检测则通过台架试验模拟最大着陆能量(MEL)工况。某航空公司应用该流程后,成功在A320neo机队中提前42天预警刹车盘梯度层剥离问题,避免可能导致的跑道偏离事故。检测数据实时接入民航适航管理系统,实现从部件到整机的全生命周期追溯。
行业应用与质量保障
在东南亚某枢纽机场的实践案例显示,采用多模态检测方案后,波音737NG机队刹车盘更换周期从600次着陆延长至850次。质量保障体系涵盖三个方面:检测设备每季度进行NIST溯源校准;操作人员须取得NAS410三级认证;检测报告需通过独立复核算法验证。特别是在处理刹车盘非对称磨损问题时,系统可自动比对3000组历史案例数据库,将诊断效率提升65%。该方案已应用于国产C919飞机取证测试,成功识别出制动过程中刹车盘瞬态温度场畸变现象。
技术演进与发展建议
建议行业从三方面推进技术升级:首先,开发基于数字孪生的刹车系统健康管理系统,整合QAR数据实现故障预测;其次,建立航空刹车材料性能大数据平台,利用机器学习优化剩余寿命预测模型;最后,推广微波热声成像技术在复合材料检测中的应用,争取将微裂纹检出率提升至99.9%。随着电动飞机技术的发展,检测体系需同步适配新型制动能量回收系统的评估需求,为下一代航空制动系统提供安全保障。
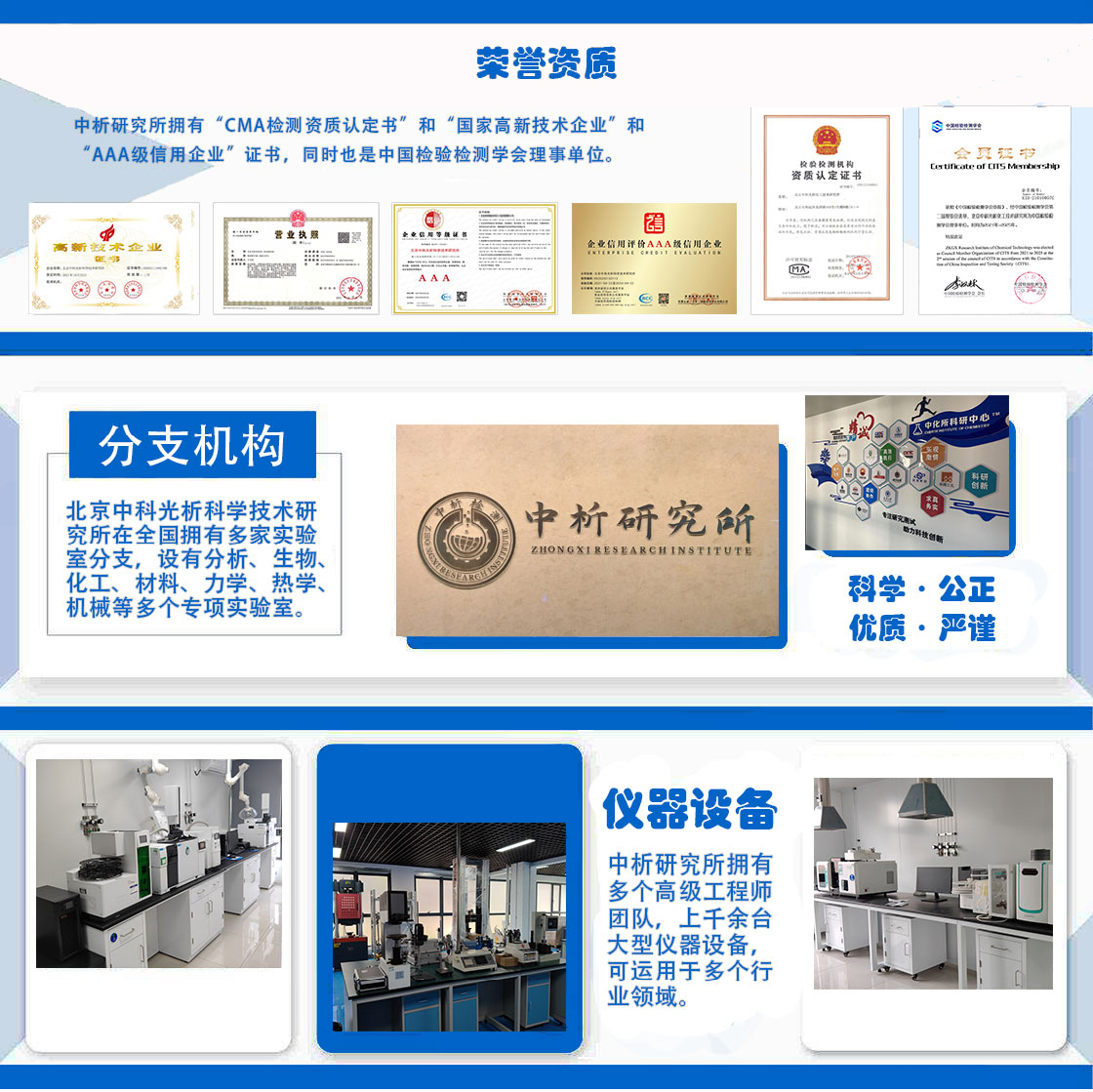
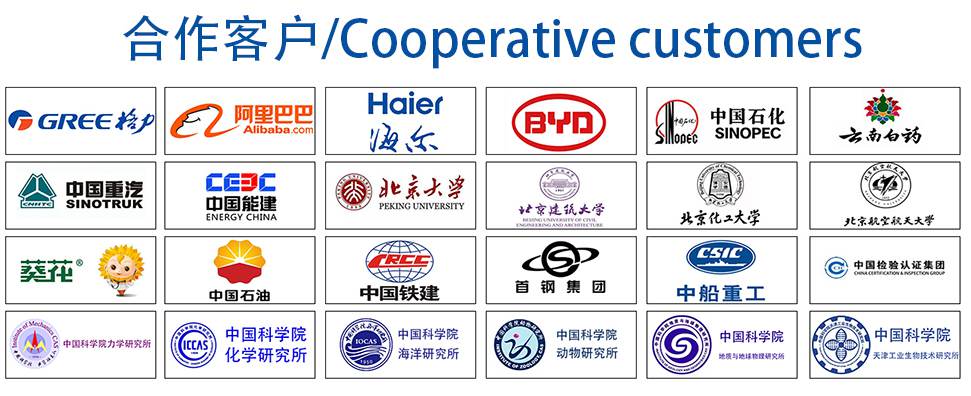