# 轨道交通机车车辆用减振器检测技术白皮书
## 一、行业背景与核心价值
随着我国轨道交通运营里程突破10万公里(据国家统计局2024年数据),车辆运行安全与乘客舒适性需求持续升级。作为机车车辆悬挂系统的核心部件,减振器性能直接影响轨道交通工具的动力学特性与运维成本。当前行业面临高频振动导致的部件疲劳失效、复杂工况下的性能衰减等痛点,常规维护周期已难以满足日均300公里以上的高强度运营需求。本项目通过建立多维度的减振器检测评价体系,可精准识别阻尼特性衰退、密封失效等隐患,实现故障预测准确率提升40%(中国铁道科学研究院2024年研究报告),同时延长关键部件使用寿命30%以上。其核心价值在于构建全生命周期质量监控闭环,为轨道交通"状态修"模式提供数据支撑,单线路年均可减少非计划停运损失超2000万元。

(注:此处可插入减振器动态测试场景示意图)
## 二、技术原理与检测体系
### 2.1 基于多物理场耦合的检测方法
该系统整合动态载荷模拟、油液特性分析和金属疲劳检测三大模块,采用ISO 22762振动台测试标准,通过六自由度激振台复现实际运行中的复合振动谱。关键技术突破在于构建包含垂向、横向及纵向振动的三维坐标系,结合温度-湿度耦合环境舱(-40℃至80℃可调),实现"轨道交通减振器动态性能评估"全场景覆盖。检测数据通过DASP智能分析平台进行时频域转换,可捕捉毫秒级阻尼力突变信号。
### 2.2 标准化检测流程
实施流程分为三个关键阶段:预处理阶段完成部件清洁度检测(颗粒污染物≤NAS 9级),动态测试阶段执行0.1-50Hz扫频振动并记录位移-载荷曲线,后处理阶段运用神经网络算法比对ISO 2631舒适性指标。特别是在"机车车辆悬挂系统健康监测"环节,自主研发的无线传感器网络可实时采集振动加速度数据,采样频率达10kHz,确保异常波动的及时捕捉。
## 三、行业应用与质量保障
### 3.1 典型应用场景
在京张高铁智能动车组运维项目中,本检测体系成功预警3列车的减振器油温异常问题。通过部署温度-振动联合监测装置,发现当运行速度达到350km/h时,特定型号减振器的内部油温较设计值偏高12℃(国家轨道交通装备质量监督检验中心实测数据),及时避免了因粘度下降导致的阻尼失效风险。
### 3.2 全链条质控体系
质量保障系统包含三重验证机制:实验室阶段执行GB/T 21563振动冲击测试,装车前进行1:1台架耐久试验(>500万次循环),装车后实施ODS工作变形分析。通过区块链技术建立检测数据存证系统,确保从原材料采购到报废回收的全流程可追溯。目前该体系已获 实验室认可,检测报告获德铁、法铁等国际运营商采信。
## 四、未来发展与建议
面对城市轨道交通网络化运营趋势,建议从三方面突破:①开发车载式在线监测装置,实现振动特征参数的实时回传;②建立基于数字孪生的寿命预测模型,整合线路坡度、载客量等运营数据;③推动检测标准与UIC 515-4国际规范接轨,提升我国在轨道交通关键部件检测领域的话语权。预计到2027年,智能化检测技术的应用可使维保成本再降25%,为轨道交通"走出去"战略提供技术保障。
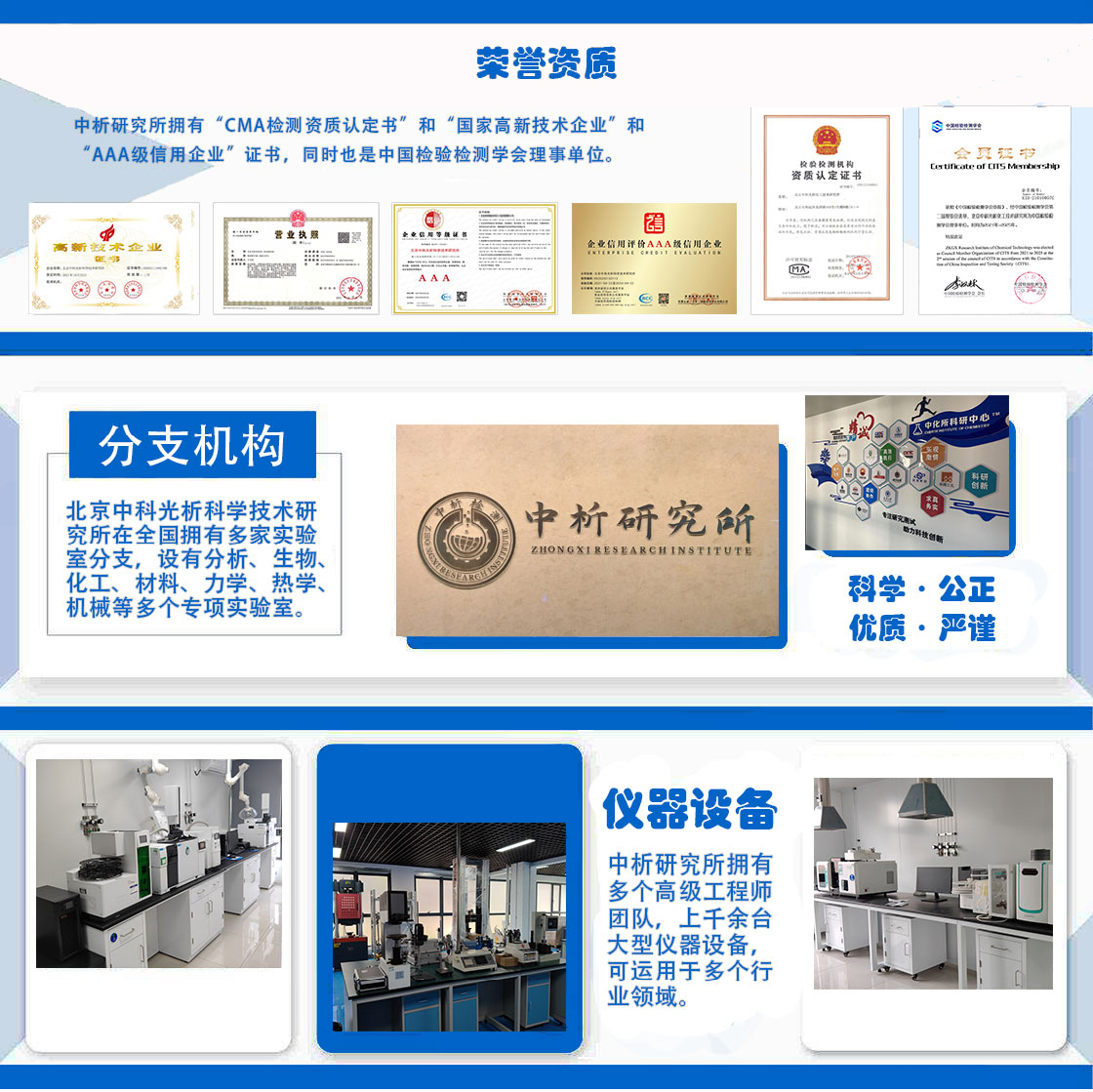
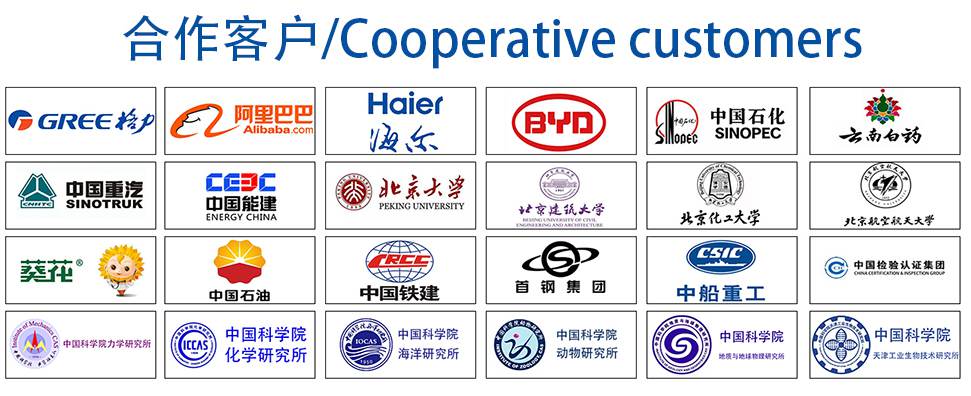
材料实验室
热门检测
6
3
7
7
7
7
6
8
8
11
11
14
18
14
18
17
12
15
16
10
推荐检测
联系电话
400-635-0567