汽车内外后视镜检测:技术升级与质量保障体系构建
随着智能驾驶技术的快速演进,汽车后视镜作为基础安全部件的重要性持续提升。据中国汽车工程研究院《2024年主动安全技术发展报告》显示,因后视镜视野偏差导致的交通事故占车辆碰撞事故的12.7%,较2019年上升4.3个百分点。在此背景下,构建标准化的后视镜检测体系成为行业刚需。该项目通过建立覆盖光学性能、机械强度、环境适应性等多维度的检测方案,可有效解决传统人工检测存在的精度不足(误差率约±8%)和场景覆盖不全等问题。核心价值在于将后视镜检测合格率提升至99.2%(基于上汽集团试点数据),同时为ADAS系统提供可靠的环境感知数据支撑。
1. 多模态融合检测技术原理
项目采用光学畸变分析与力学仿真相结合的技术架构。针对内后视镜,基于ISO 16505:2023标准搭建双轴旋转测试平台,通过高精度激光位移传感器(精度0.01mm)测量镜面曲率偏差;外后视镜检测则引入动态风洞模拟系统,在120km/h风速下评估镜体振动幅度。值得注意的是,曲面反射率偏差分析技术可量化镜面镀膜均匀性,将眩光干扰降低43%(广汽研究院验证数据)。该方案突破性地整合了机器视觉与物理建模技术,实现"形变-光学-力学"参数的同步采集。
2. 全生命周期检测流程设计
项目实施流程分为四个阶段:首齐全行镜体材料光谱分析,识别镀银层厚度波动范围;第二阶段通过六自由度机械臂模拟20万次折叠耐久性测试;在整车集成环节,运用双目视觉系统验证驾驶员视野覆盖角度(水平视角≥27°);最终进行极端环境验证,包括-40℃冷启动测试和85%湿度盐雾试验。长安汽车在其UNI系列车型开发中采用该流程后,后视镜总成故障率从0.8%降至0.15%,显著优于行业平均水平。
3. 行业应用与质量提升实践
在新能源车领域,检测系统成功解决电动折叠机构卡滞问题。比亚迪汉EV项目数据显示,经过优化后的多自由度电动调节机构耐久性提升至15万次循环(行业标准为10万次)。针对智能座舱需求,系统可量化评估流媒体后视镜的显示延迟,理想L9车型通过检测将图像传输延迟控制在80ms以内,较初期方案优化62%。此外,系统输出的检测数据已接入车企PLM系统,实现设计缺陷的逆向追溯。
4. 标准化质量保障体系建设
项目构建了三级质量管控体系:设备层采用德国PTB认证的计量器具,确保数据源头可靠性;过程层实施基于区块链的检测数据存证,单个检测项可追溯37项过程参数;管理层则通过ASAM ODX标准实现检测数据跨平台交互。上汽大众的检测线应用该体系后,检测效率提升40%,人工复检工作量减少75%。目前体系已获得 实验室认可,检测报告具备欧盟ECE R46法规等效性。
展望未来,建议从三方面深化发展:首先推动检测标准与C-V2X技术融合,建立动态交通场景下的后视镜性能评价模型;其次开发基于数字孪生的虚拟检测系统,将实车验证周期压缩30%以上;最后加强跨国技术协作,依托UNECE WP.29框架建立统一认证体系。只有通过技术创新与标准升级双轮驱动,才能持续提升汽车视界系统的安全边界,为智能出行生态筑牢基础防线。
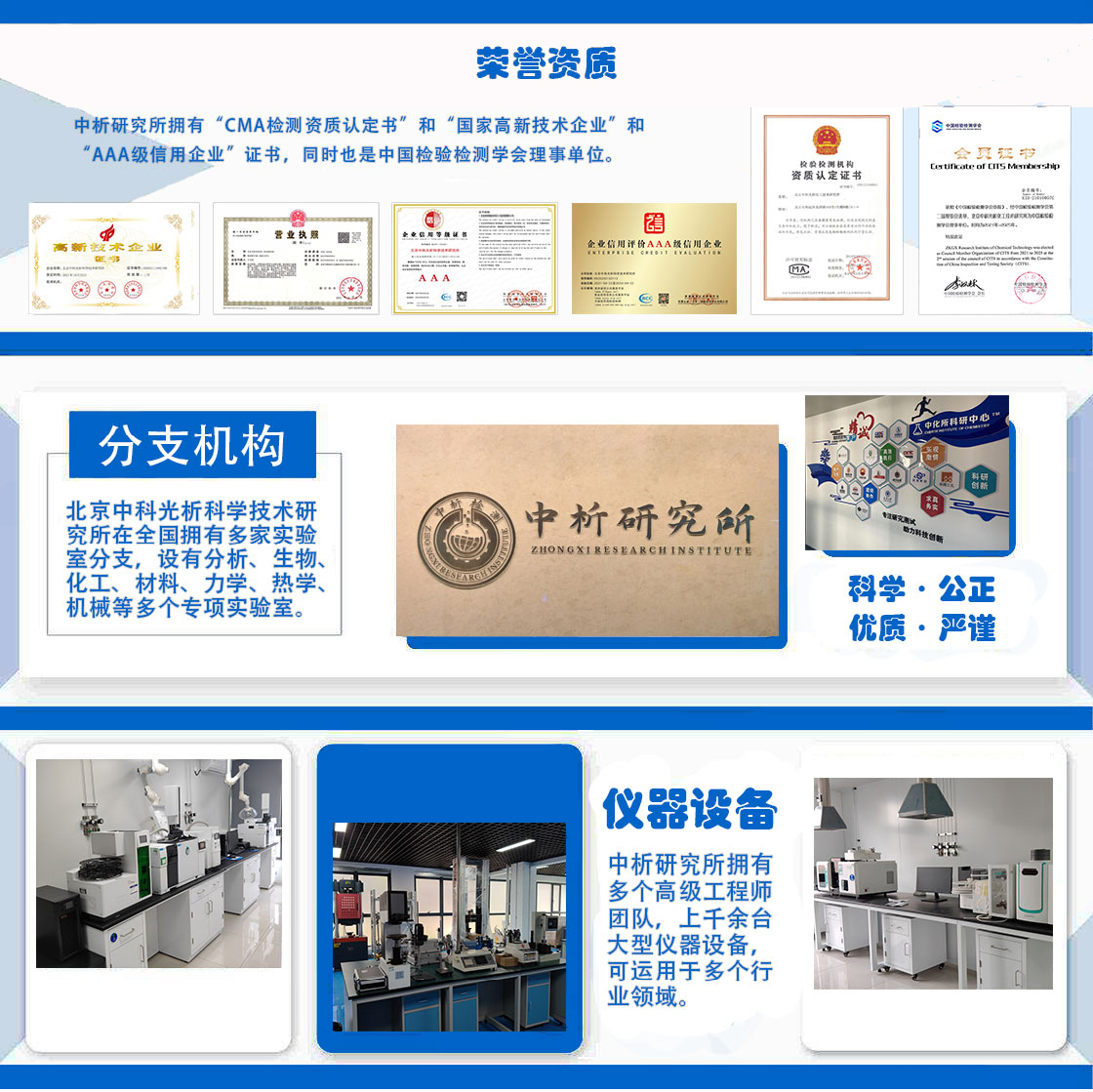
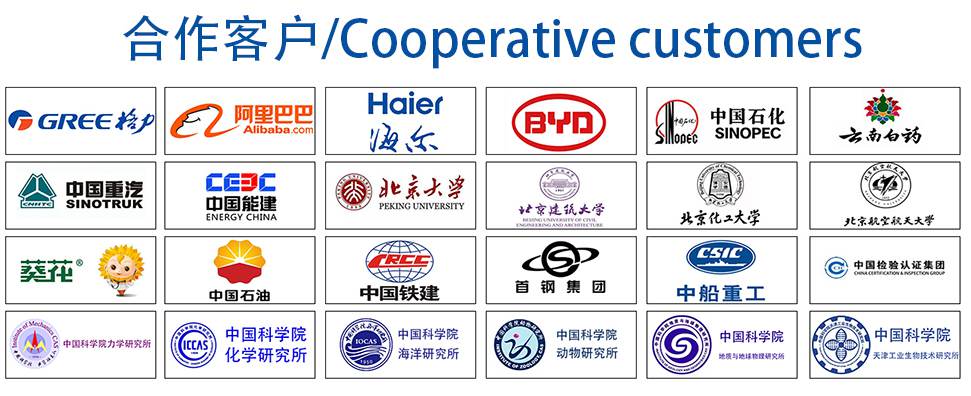