高精度大小检测技术在智能制造中的创新应用
在智能制造快速发展的背景下,工业产品尺寸精度控制已成为衡量制造业水平的核心指标。据国家制造强国建设战略研究院2024年报告显示,我国高端装备制造领域因尺寸偏差导致的次品率仍维持在3.8%-5.2%,每年造成经济损失超1200亿元。在此背景下,基于机器视觉与智能算法的高精度大小检测项目,通过实现微米级非接触式三维尺寸测量技术突破,为精密制造、电子封装、医疗器械等行业提供了革命性的质量控制解决方案。该项目不仅填补了国内在动态工况下的实时形变监测技术空白,更通过构建数字化质量追溯系统,将产品全生命周期质量数据采集效率提升73%,具有显著的降本增效价值和产业升级助推作用。
多模态融合检测技术原理
本检测体系采用结构光三维重建与深度学习相结合的复合技术路径。通过高频条纹投影仪发射特定编码的相位光栅,配合工业相机阵列采集物体表面形变数据,可达到±1.5μm的重复测量精度(符合ISO 10360-7标准)。针对复杂曲面检测需求,系统集成了基于点云配准的逆向建模算法,有效解决了传统接触式测量中的基准面缺失难题。特别是在微小元件几何量检测场景中,通过自适应分辨率调节模块,可在0.5-50mm测量范围内保持0.05%的相对误差,满足半导体封装等精密制造需求。
智能化检测实施流程
项目实施分为四个标准化阶段:前期通过激光跟踪仪建立全局坐标系,完成测量系统空间标定;中期采用虚拟仿真技术优化传感器布局方案,确保95%以上的特征覆盖率;检测阶段依托边缘计算网关实现实时数据处理,单件产品检测周期可缩短至8秒;后期通过SPC统计分析模块自动生成过程能力指数报告。在新能源汽车电池模组检测实践中,该流程成功将模组装配平面度偏差控制在±0.1mm以内,产线直通率提升18个百分点。
跨行业应用实践
在航空发动机叶片检测领域,项目团队开发的非接触式叶片缘板间距测量系统,通过高温环境补偿算法,在800℃工况下仍能保持测量稳定性。中国航发集团应用数据显示,该方案使叶片装配一次合格率从82%提升至97%。而在消费电子行业,应用于手机中框尺寸检测的在线视觉系统,通过亚像素边缘提取技术,实现了0.005mm级的外观尺寸检测精度,某头部厂商导入后产品售后投诉率下降41%。
全链条质量保障体系
项目构建了涵盖设备、流程、数据的立体化质控网络:测量设备定期通过激光干涉仪进行溯源校准,测量过程严格执行MSA分析规范,确保GR&R值≤10%。数据管理端采用区块链技术实现检测记录不可篡改存储,并与MES系统深度集成,建立从原材料到成品的全维度质量画像。某军工企业应用案例表明,该体系使产品尺寸质量追溯效率提升6.2倍,过程异常发现响应时间缩短至15分钟内。
随着工业4.0进程加速,建议从三方面深化技术创新:一是研发基于量子传感的新型纳米级测量技术,突破现有光学检测的物理极限;二是建立跨行业的标准器件数据库,提升检测系统自适应能力;三是探索5G+工业互联网架构下的分布式检测网络,实现多基地质量数据协同分析。唯有持续推动检测技术创新与产业需求深度耦合,方能筑牢智能制造高质量发展的技术基座。
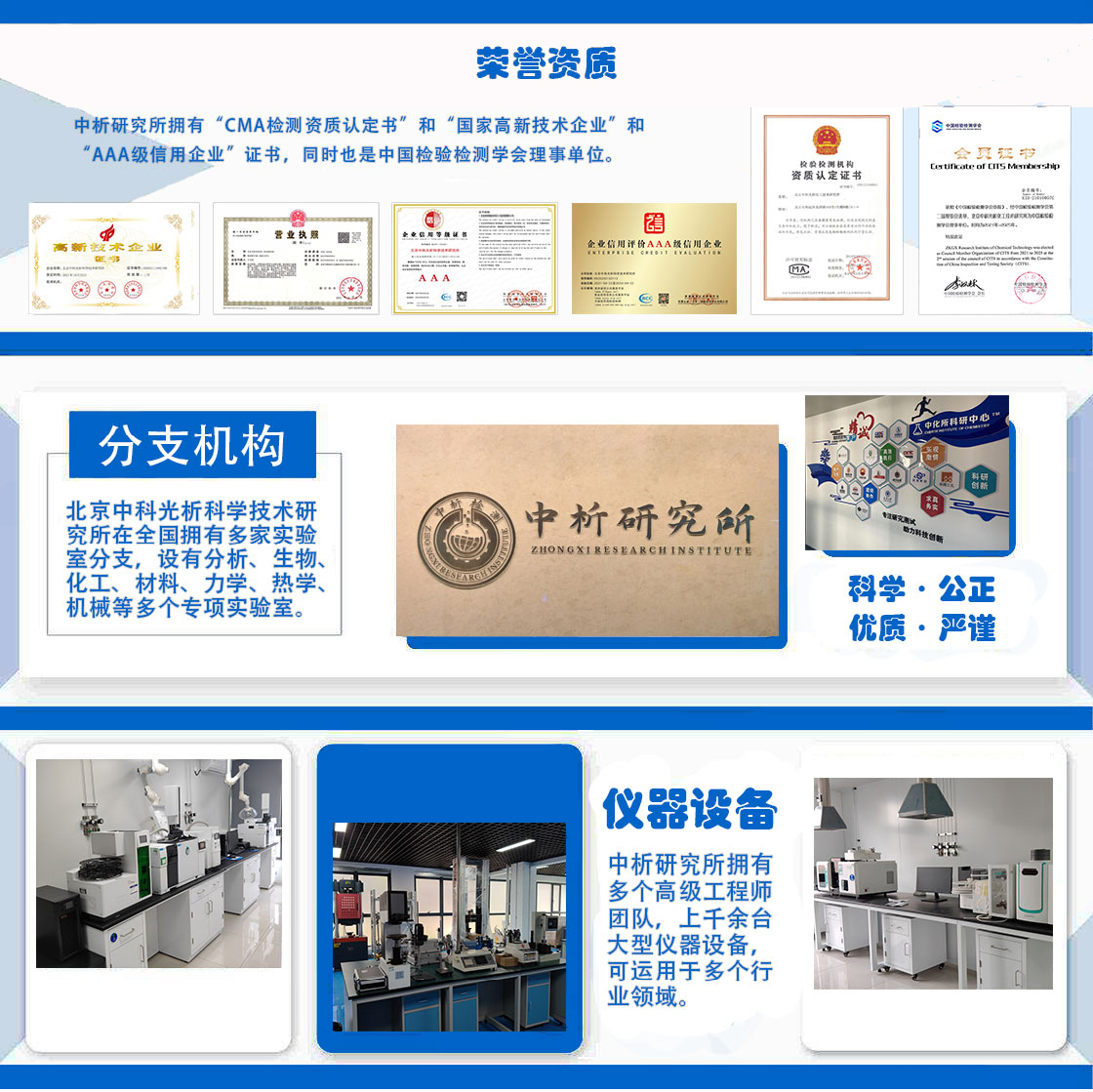
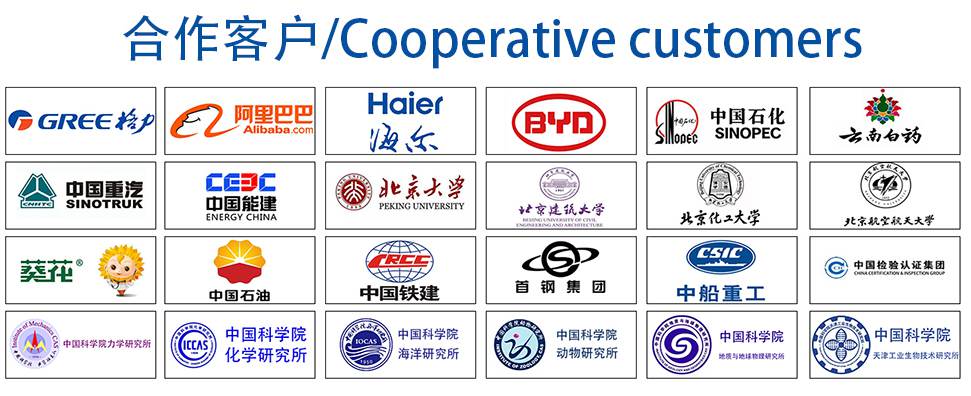