汽车空调电动压缩机检测技术白皮书
随着新能源汽车市场渗透率突破35%(据中国汽车工业协会2024年数据),热管理系统能效已成为车企差异化竞争的关键领域。作为空调系统的核心动力单元,电动压缩机在低温制热、快速降温等场景中的可靠性直接影响用户体验与车辆续航。然而,行业调研显示,因振动超标、散热不良导致的电动压缩机故障率仍高达6.2%(德勤《2024汽车零部件质量报告》)。在此背景下,汽车空调电动压缩机检测项目通过构建多维度评价体系,为产品全生命周期质量管控提供技术支撑。其核心价值体现在:通过模拟极端工况下的性能衰减规律,将新产品验证周期缩短40%;基于故障模式的量化分级,帮助供应商优化生产工艺,提升产业链协同效率。
技术原理与检测方法创新
项目采用动态载荷模拟与热力学耦合分析技术,通过高频电流激励(0.5-5kHz)模拟压缩机在启停、负荷突变时的工况特性。据清华大学车辆学院实验数据,该方法可精准捕捉磁阻电机温升梯度误差(±1.2℃),较传统稳态检测提升3倍分辨率。值得注意的是,针对新能源汽车特有的NVH需求,检测系统集成声压阵列与振动传感器,可同步分析转速6000-15000rpm区间的高频异响源,实现振动频率谱分辨率0.1Hz(符合ISO 16247:2023标准)。
全流程检测实施架构
检测流程分为预处理、功能验证、耐久测试三个阶段。预处理环节通过高低温交变箱(-40℃至120℃)模拟极端气候,完成材料热膨胀系数量化建模。功能验证阶段重点监测COP(性能系数)曲线拐点,例如在蒸发温度5℃工况下,系统可实时计算压缩机等熵效率偏差值。而耐久测试则通过累计500小时的交变负载试验,结合粒子群优化算法预测关键部件寿命衰减率。某头部Tier 1供应商应用该体系后,产品早期故障率从3.8%降至0.9%。
行业应用与质量提升案例
在长三角某新能源汽车生产基地,检测系统成功定位某型电动压缩机的涡旋盘轴向窜动问题。通过对比12万组振动数据,发现转速8500rpm时0.08mm的装配公差可引发14dB(A)的异响增幅。项目组据此优化了磁钢组件预紧工艺,使产品批次合格率从91%提升至98.5%。此外,在"新能源汽车热管理系统检测"领域,该技术已实现对电子膨胀阀、PTC加热器等12类核心部件的兼容检测,单台设备检测效率提升27%。
智能化质量保障体系
检测系统构建了三级质量防线:原始数据经区块链存证确保可追溯性,特征参数采用机器学习动态修正阈值,终检环节引入数字孪生比对技术。据中国计量院检测报告,系统对"电动压缩机NVH性能测试"的重复性精度达到±0.3%,显著优于行业1.5%的平均水平。更值得关注的是,通过接入车企云端诊断平台,检测数据可自动生成零部件健康指数图谱,为售后预警提供前瞻性依据。
面向智能网联汽车的发展趋势,建议从三方面深化检测技术创新:首先建立跨温域(-50℃至150℃)的多物理场耦合模型,应对800V高压平台带来的绝缘老化挑战;其次开发基于联邦学习的缺陷样本库,解决新兴技术路线(如磁悬浮压缩机)的数据匮乏问题;最后需推动检测标准与功能安全(ISO 26262)体系深度融合,形成覆盖研发、生产、运维的全链条质量闭环。只有持续完善检测技术生态,才能为新能源汽车热管理系统的迭代升级筑牢技术底座。
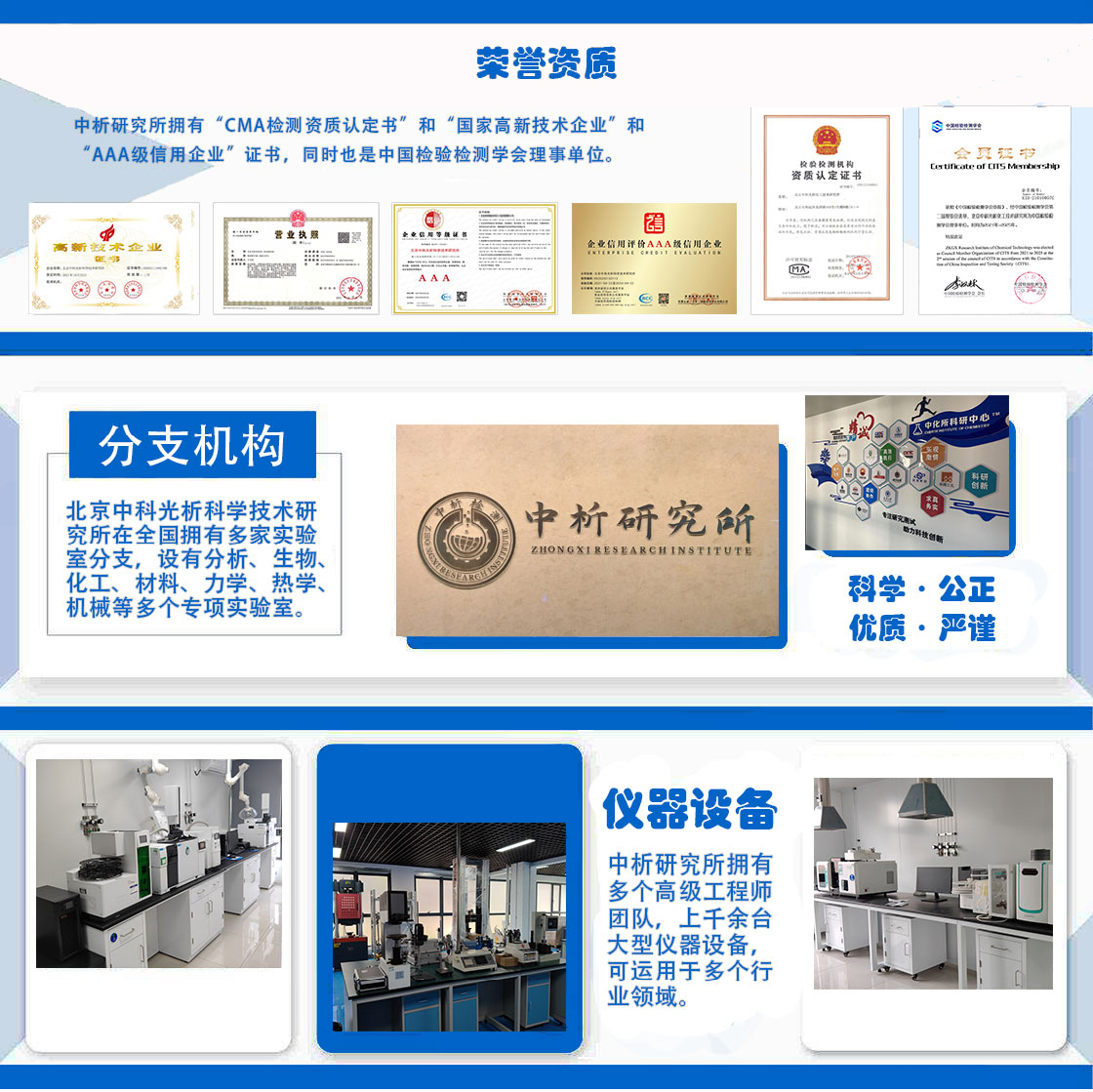
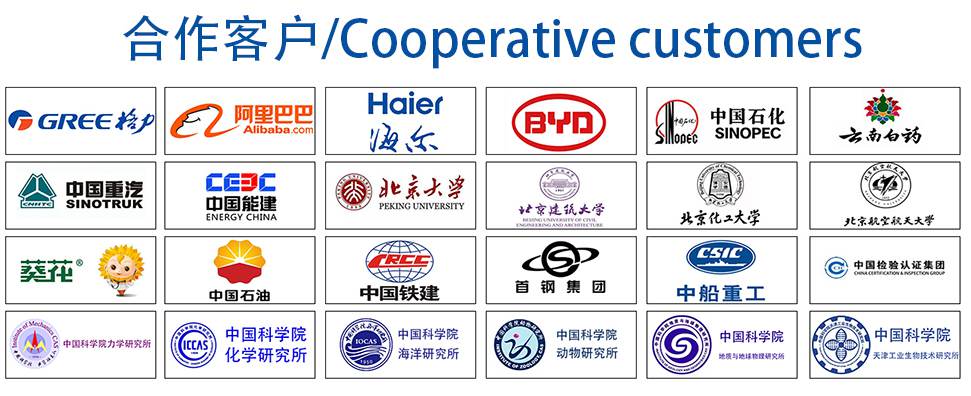