铸件重量检测:关键检测项目及其重要性
一、静态重量检测
- 使用高精度电子秤或地磅,在铸件完全冷却后测量其净重。
- 对比实测值与图纸或工艺规定的理论重量,误差需控制在允许范围内(通常±2%~5%)。 意义:
- 避免因重量偏差导致的结构强度不足或材料浪费。
- 识别浇注系统设计缺陷(如冒口过大导致金属液浪费)。
二、动态重量检测(在线监测)
- 在生产线上集成传感器和动态称重设备,实时采集铸件重量数据。
- 结合PLC系统,自动剔除超差产品并触发警报。 工具:
- 动态称重机、红外传感器、工业控制软件。 意义:
- 减少人工抽检的时间成本,提升检测效率。
- 及时发现模具磨损、铁水温度波动等异常因素。
三、批次平均重量检测
- 随机抽取批次样本(通常按10%~20%比例),计算平均重量及标准差。
- 分析数据波动是否在可控范围内(如CPK≥1.33)。 意义:
- 监控生产稳定性,预防系统性误差(如模具老化、原料密度不均)。
- 为工艺参数优化提供数据支持。
四、重量分布分析
- 绘制重量分布直方图或控制图,验证数据是否符合正态分布。
- 分析异常分布(如双峰分布可能预示多模具生产中的个体差异)。 工具:
- Minitab、Excel数据分析模块、SPC(统计过程控制)系统。 意义:
- 提前预警设备故障或工艺参数偏移。
- 优化浇注速度和冷却时间,提升产品一致性。
五、重量与尺寸关联性检测
- 同步测量铸件的关键尺寸(如壁厚、长度)和重量。
- 计算实际密度,对比材料理论密度,排查内部缺陷(缩孔、气孔)。 公式: 密度=重量体积密度=体积重量 意义:
- 识别因尺寸偏差或内部缺陷导致的隐性质量问题。
- 优化模具设计,确保壁厚均匀性。
六、自动化实时检测与数据追溯
- 采用MES(制造执行系统)记录每件铸件的重量、时间、生产线编号等信息。
- 通过条形码或RFID技术关联检测数据与生产批次。 意义:
- 快速定位问题根源,缩短故障排查时间。
- 满足汽车、航空等行业对质量追溯的强制性要求。
七、检测项目应用案例
- 汽车行业:发动机缸体铸件需严格控制重量(±1.5%),避免影响动力平衡。
- 泵阀行业:通过重量-密度关联检测,确保承压部件无内部气孔。
- 节能评估:统计月度重量合格率,优化金属利用率,降低吨铸件能耗。
转成精致网页
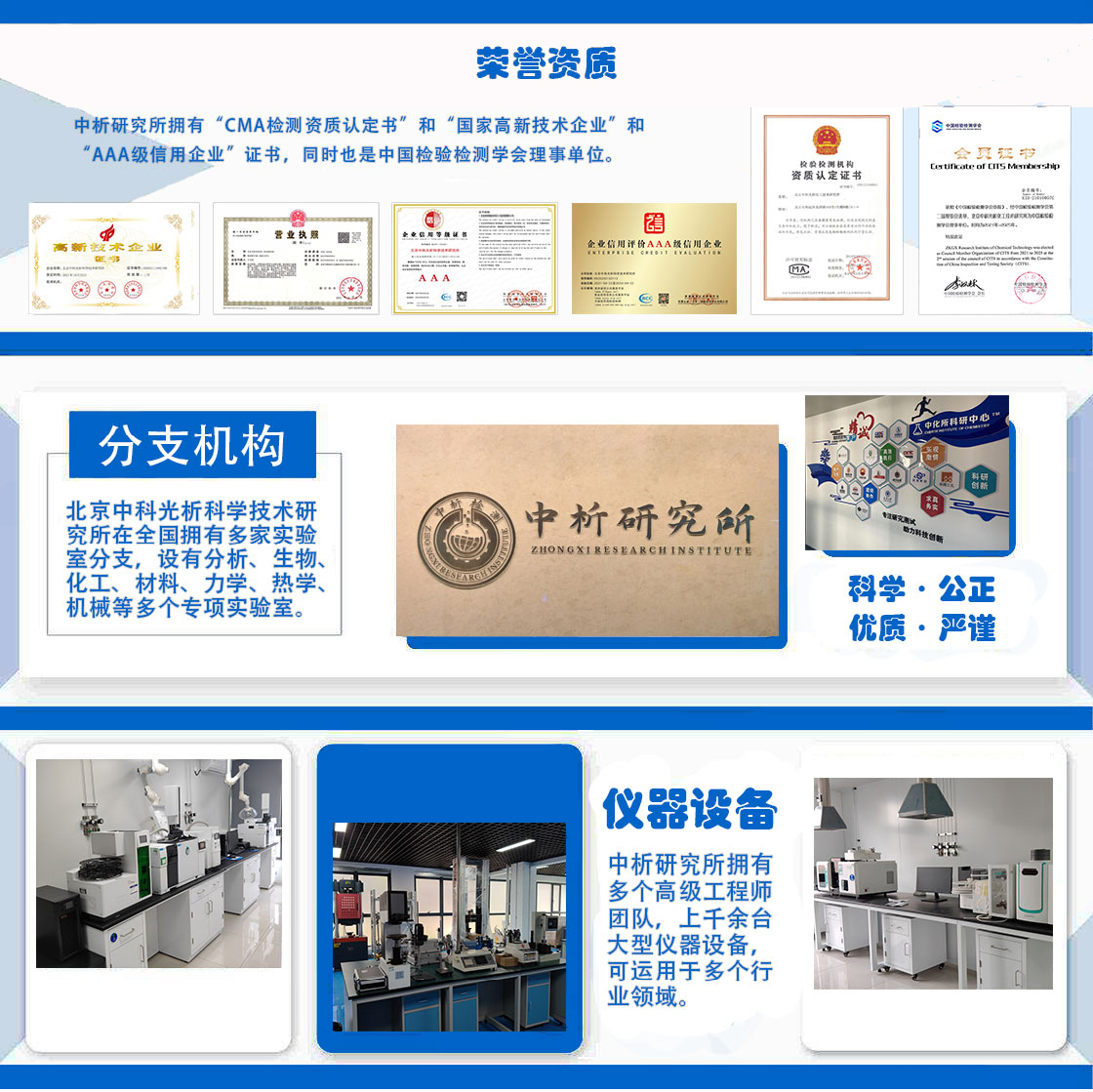
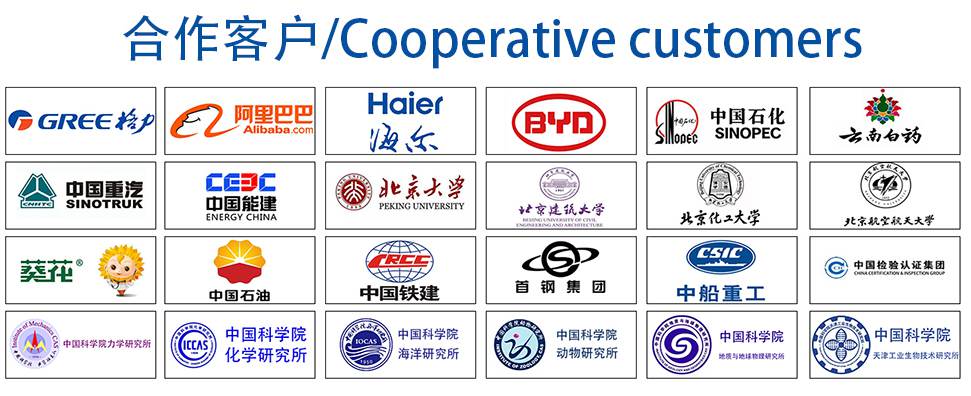
材料实验室
热门检测
16
10
19
14
19
18
22
28
21
18
20
22
20
26
28
21
29
25
21
28
推荐检测
联系电话
400-635-0567