容积泵零部件液压与渗漏试验检测概述
容积泵作为工业流体输送的核心设备,其性能稳定性直接关系到生产系统的安全与效率。液压与渗漏试验是容积泵零部件出厂及维修后必检的关键环节,旨在验证零部件的耐压能力、密封性能及长期运行的可靠性。该检测通过模拟实际工况下的压力载荷和介质渗透条件,精准识别泵体、密封件、阀组等部件的潜在缺陷,确保其符合国家标准(如GB/T 7784)及行业技术要求。试验过程中需结合泵型特点(如齿轮泵、柱塞泵、螺杆泵等),针对关键零部件设计差异化的检测方案,以覆盖材料疲劳、密封失效、接口渗漏等主要风险点。
核心检测项目及技术要求
1. 泵体承压测试
采用水压或油压介质进行,试验压力通常为额定工作压力的1.5倍,保压时间≥30分钟。需监测泵体变形量(≤0.05%)、表面渗漏及异常振动,重点检查铸造缺陷区域和焊缝连接处。
2. 密封装置渗漏检测
包括机械密封、填料密封等组件,需在动态工况下验证密封效果。使用氦质谱检漏法或气泡法检测泄漏率,要求静态泄漏量≤5mL/h,动态泄漏量≤10mL/h(依据API 682标准)。
3. 连接部件密封性验证
对法兰接口、螺纹连接等部位进行气压试验(0.6-1.0MPa),通过涂刷检漏液观察气泡形成情况,要求所有连接点30分钟内无连续气泡产生。
4. 安全阀与压力补偿机构测试
验证安全阀启闭压力精度(误差≤±2%设定值),检测压力补偿装置的响应时间(≤0.5秒)。使用流量计记录溢流状态下压力波动,确保系统压力稳定性。
试验流程与判定标准
试验流程包括预处理(清洁度检查)→分级加压(按20%阶梯递增)→保压监测→降压观察→数据记录五个阶段。判定依据需满足:①无可见塑性变形;②压降率≤3%/h;③渗漏点数量≤3处且单点泄漏量<0.1mL/min。对于齿轮泵需额外检测齿面接触区的微渗漏,柱塞泵则重点关注缸体与滑靴配合面的油膜完整性。
常见失效模式及改进措施
试验中常发现密封圈老化(占比42%)、铸件砂眼(28%)、装配间隙偏差(20%)三类问题。针对性地采取表面纳米涂层强化、激光熔覆修复、装配公差优化(控制到±0.01mm)等措施,可显著提升零部件合格率。某案例显示,通过改进柱塞杆硬化工艺,泵体耐压能力提升37%,运行寿命延长至8000小时以上。
检测设备与技术发展
现代检测已集成PLC控制系统、高精度压力传感器(±0.25%FS)和红外热成像技术,实现实时数据采集与智能诊断。基于机器视觉的自动渗漏识别系统可将检测效率提升60%,同时AI算法能预测零部件剩余寿命,推动检测从被动验证向主动预防转型。
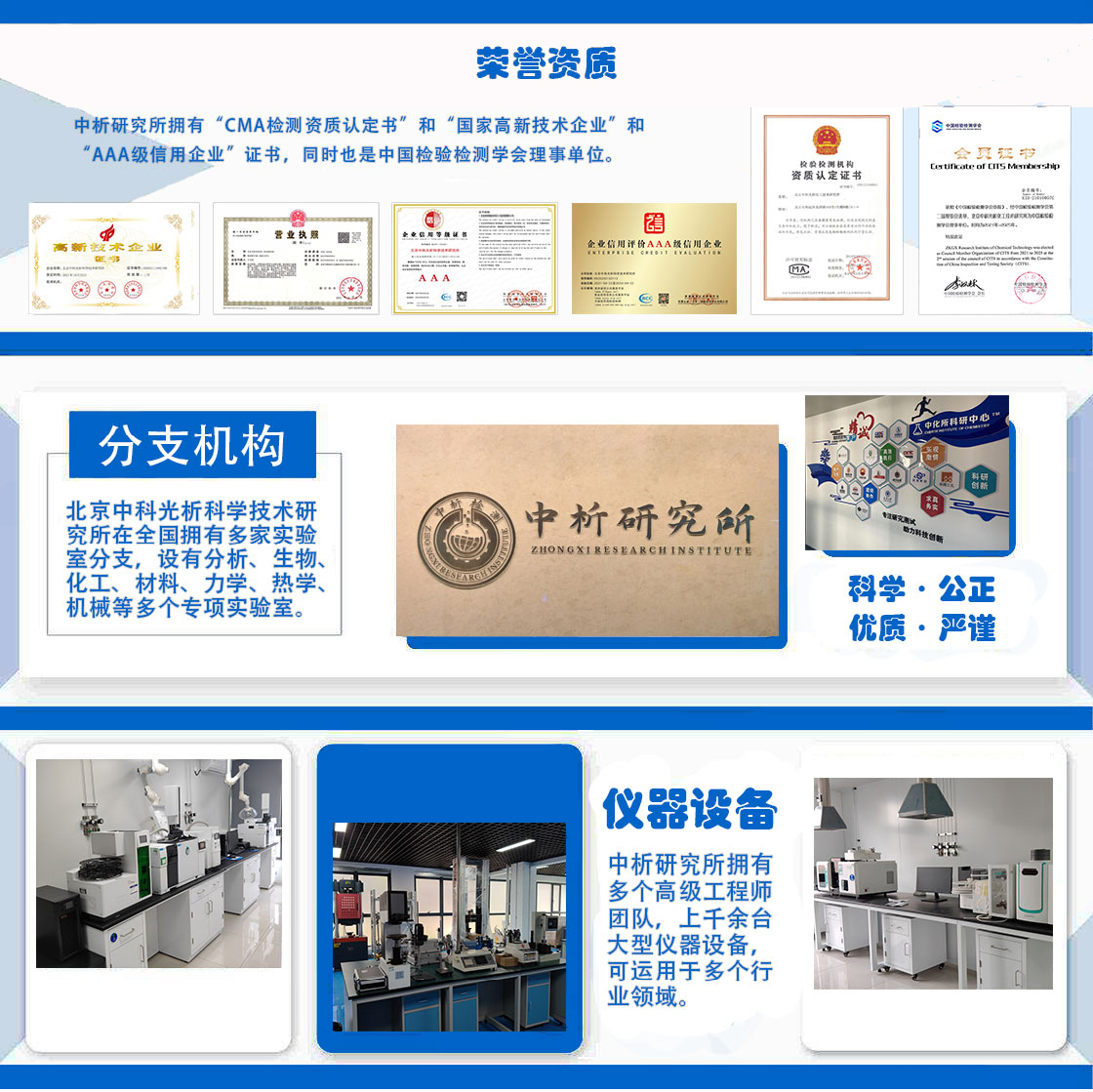
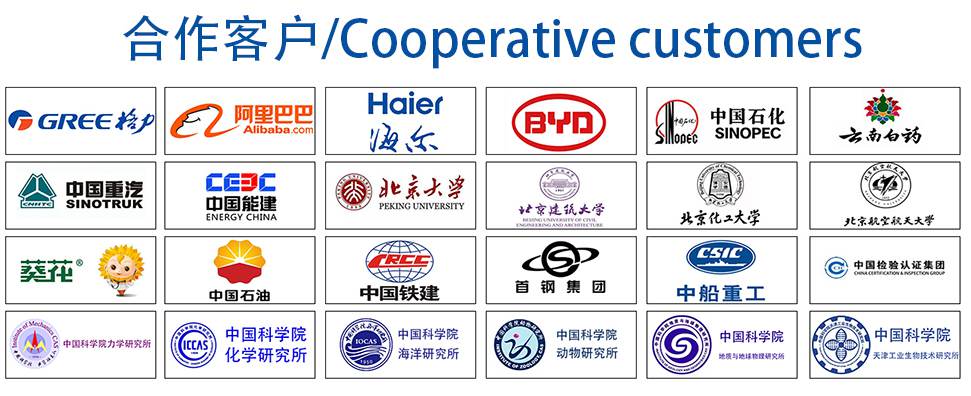