在用工业热交换器检测的重要性与范围
作为工业热能传递的核心设备,工业热交换器在化工、电力、冶金等领域的应用极为广泛。其长期运行过程中易受介质腐蚀、结垢、机械应力等多种因素影响,可能导致传热效率下降、泄漏甚至设备失效。定期开展在用工业热交换器的系统检测,不仅能保障生产安全、预防突发性故障,还可通过优化运行参数实现节能降耗,延长设备使用寿命。检测范围通常涵盖结构完整性、密封性能、传热效率等多维度指标。
关键检测项目及技术要求
1. 外部宏观检查
通过目视检验和简单工具测量,重点检查壳体变形、焊缝开裂、法兰连接处渗漏等异常现象。使用超声波测厚仪对壳体及管束进行壁厚测量,腐蚀严重区域需建立连续监测档案。
2. 密封性检测
采用气压试验(0.05-0.1MPa)或液压试验(1.25倍设计压力)验证密封系统完整性。对于高危介质设备,推荐使用氦质谱检漏技术,可检测出1×10⁻⁶Pa·m³/s级别的微小泄漏。
3. 管束状况检测
运用内窥镜技术对换热管内部进行可视化检查,评估腐蚀坑深度、裂纹扩展程度。通过涡流检测仪对管束进行快速扫查,可发现80%以上的管壁减薄缺陷,检测精度达到±0.1mm。
4. 传热性能测试
通过测量进出口温度、流量参数,计算实际传热系数与设计值的偏差。当K值下降超过15%时,需启动除垢程序或进行结构改造。配套红外热成像技术可直观显示温度场分布异常区域。
5. 支撑结构评估
对折流板、管板、拉杆等承力部件进行无损检测(MT/PT),重点排查应力腐蚀裂纹。弹簧支吊架的载荷测试需确保其补偿能力满足热膨胀位移要求。
检测标准与周期管理
检测活动应严格遵循TSG 21-2016《固定式压力容器安全技术监察规程》、GB/T 151-2014《热交换器》等标准要求。常规检测周期为12-36个月,对处于强腐蚀环境或连续高压运行的设备,需缩短至6-12个月。建立基于风险分析的RBI检测机制可显著提升检测效益。
检测后的处理措施
检测发现局部腐蚀时可采取复合材料修补技术,管束泄漏率超过10%时应考虑整体更换。每次检测后需更新设备健康档案,并结合运行数据优化清洗策略。极端工况下的热交换器还应加装在线监测系统,实现关键参数的实时预警。
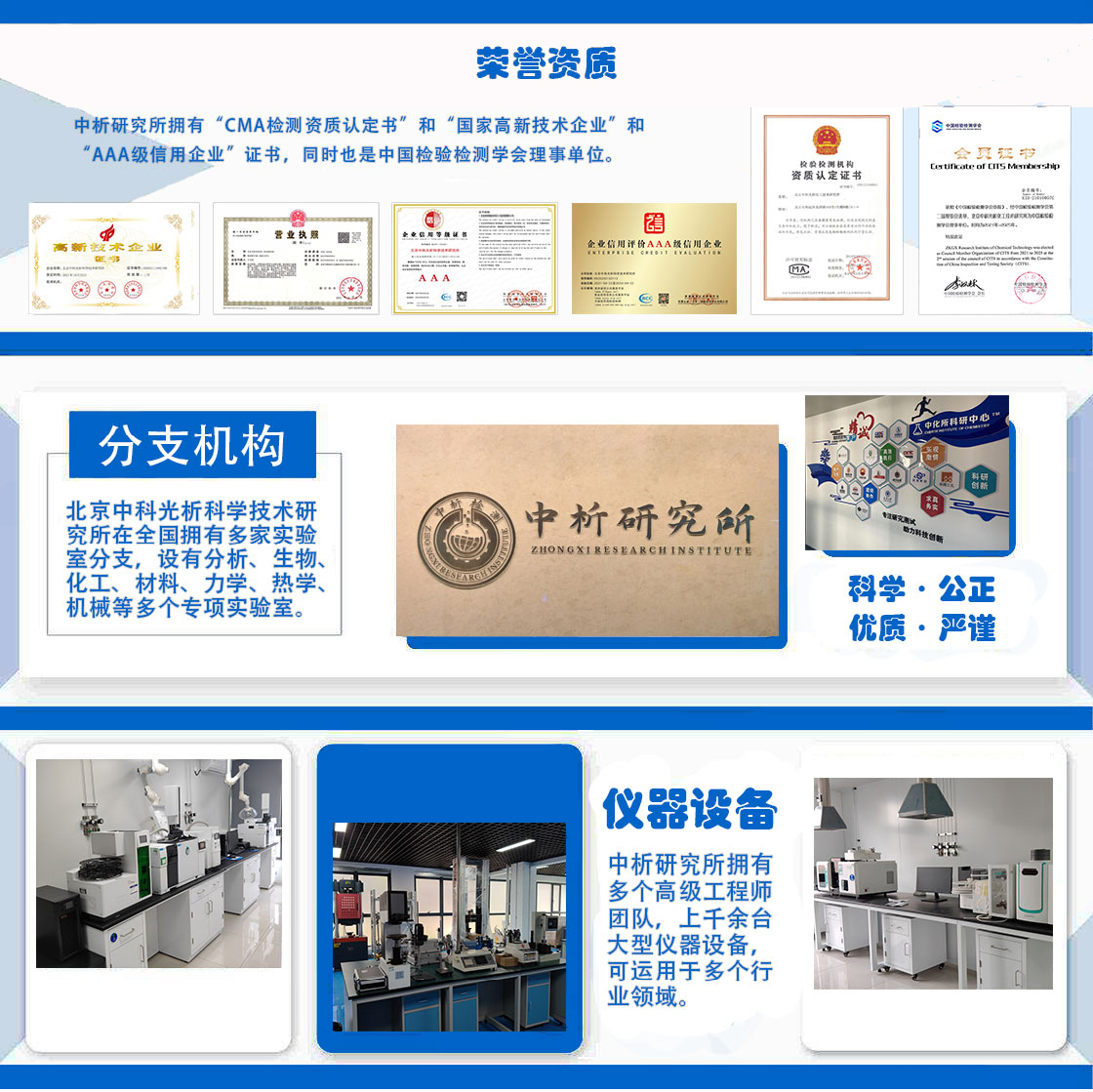
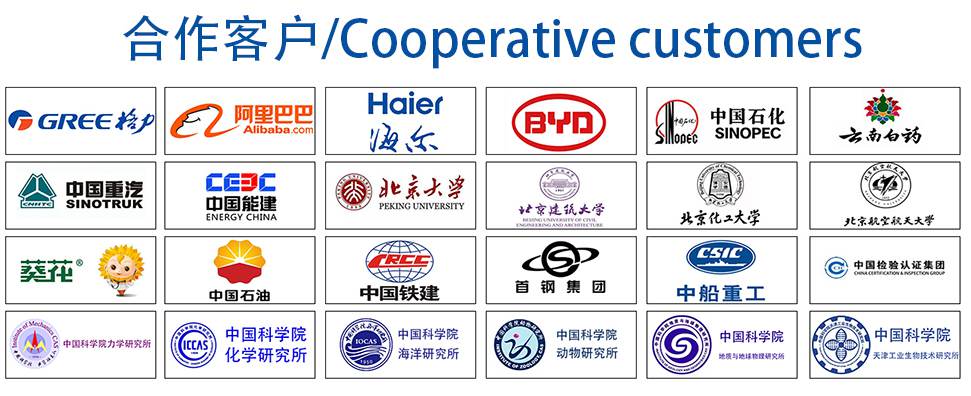