蒸压砖自动液压机检测的重要性与核心内容
蒸压砖作为一种环保型建筑材料,其生产过程中液压机的性能直接决定了成品砖的强度、尺寸精度及生产效率。自动液压机通过高压成型、精准控温等工艺,可高效完成砖坯压制与养护。然而,设备长期运行中可能因磨损、参数偏差或控制系统故障引发质量问题。因此,定期对蒸压砖自动液压机开展系统性检测,是保障生产稳定性、延长设备寿命和降低能耗的关键环节。
核心检测项目及技术要求
1. 液压系统压力与稳定性检测
通过压力传感器和示波器监测主油缸、增压缸的压力输出曲线,验证峰值压力是否达到设计值(通常为20-35MPa)。同时检查保压阶段压力波动范围是否符合≤±1.5%的标准,排查液压阀组泄漏、油泵效率下降等问题。
2. 模具定位精度与平行度检测
使用激光测距仪和水平仪测量上下模具的闭合间隙,要求四角偏差≤0.05mm/m²。在空载和满载状态下分别检测模具平行度,确保成型砖坯厚度误差控制在±0.3mm以内。
3. 温控系统性能验证
在蒸压养护阶段,需对加热板的温度均匀性进行测试:布设9点测温探头,要求同一批次砖坯表面温差≤5℃。同时验证PID温控模块的响应速度,升温速率应达到2-3℃/min且无超调现象。
4. 自动化控制系统检测
通过PLC通讯测试检查各传感器(位置/压力/温度)信号反馈的实时性与准确性。模拟异常工况(如物料不足、超压报警),验证紧急停机、故障自诊断功能的触发成功率需达到100%。
5. 机械结构疲劳损伤排查
采用超声波探伤仪对机架焊接部位、立柱螺纹连接处进行裂纹检测。检查导向柱与衬套的配合间隙,若超过0.15mm需立即更换,防止偏载导致的设备变形。
检测周期与数据管理建议
常规检测建议每生产5000模次或3个月执行一次,关键参数需纳入设备运行数据库。通过比对历史数据趋势,可预判液压密封件老化、电气元件性能衰退等问题,实现预测性维护,将故障率降低60%以上。
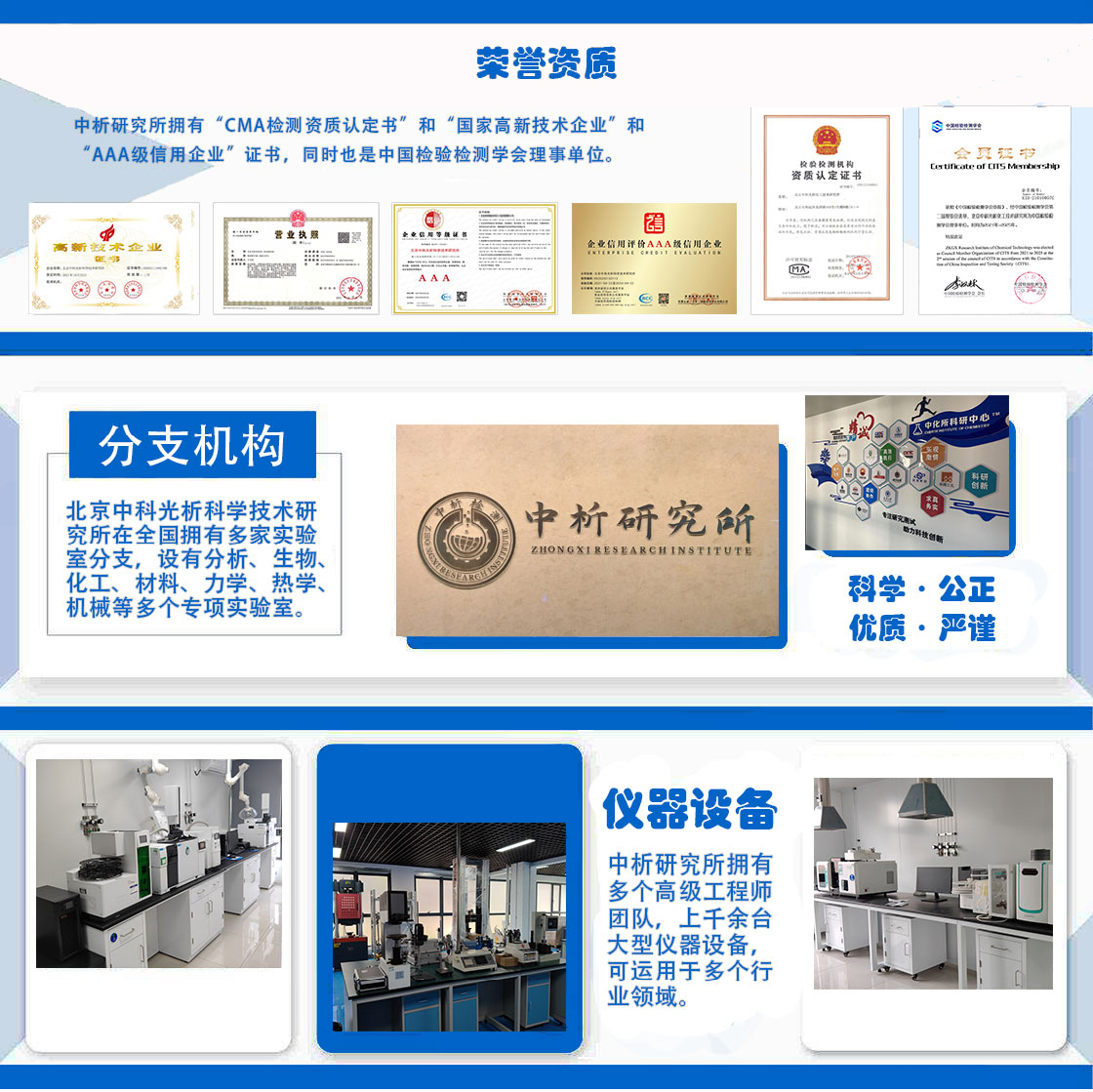
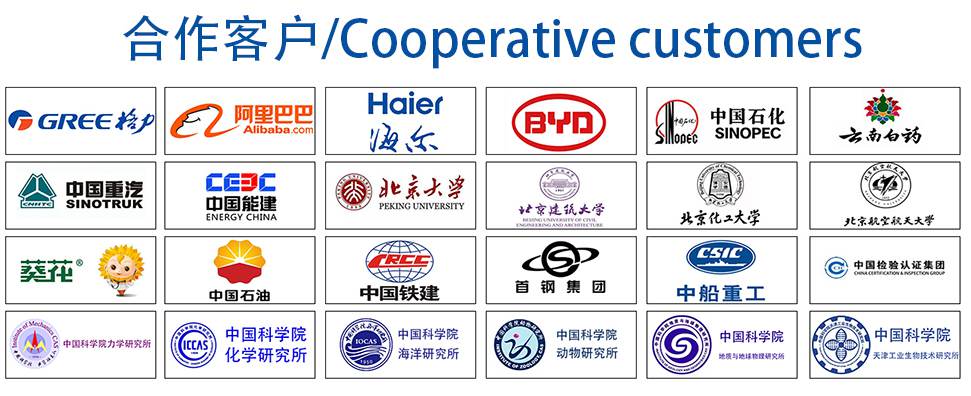