玻璃纤维工业用隧道式原丝烘干炉检测的重要性及关键项目
在玻璃纤维生产过程中,隧道式原丝烘干炉是核心设备之一,其性能直接关系到原丝的干燥效率、能耗水平及最终产品质量。由于烘干炉需长时间处于高温、高湿的复杂工况下运行,定期开展系统性检测是确保设备安全稳定运行、优化生产工艺的必要手段。检测工作不仅能够发现潜在故障隐患,还能为节能降耗和技术升级提供数据支持,从而提升企业生产效益。
一、温度均匀性与控制精度检测
烘干炉内部温度的均匀性是影响原丝干燥质量的关键因素。检测需通过多点温度传感器(如热电偶或红外测温仪)对炉内不同区域的温度分布进行实时监测,重点验证加热系统的响应速度、PID温控算法的稳定性以及各温区的偏差值(通常要求≤±3℃)。若发现温度波动异常,需检查加热元件、隔热层或循环风机的运行状态。
二、热风循环系统性能评估
热风循环系统的效率直接影响烘干炉的能耗与干燥效率。检测项目包括:风机风量及压力测试、热交换器换热效率分析、风道密封性检查等。需通过风速仪测量关键位置的风速均匀性,并利用压差计验证风道阻力是否符合设计要求(一般要求风量损失<5%)。同时,过滤装置的堵塞情况也需定期清理监测,以避免粉尘积累导致能耗上升。
三、安全防护与电气系统检测
高温设备的安全性是检测重点。需检查超温报警装置、紧急停机功能、烟雾探测系统的有效性,并对电气线路的绝缘电阻(≥1MΩ)、接地电阻(≤4Ω)进行测试。此外,燃气或电加热系统的燃烧器/加热管需定期进行泄漏检测及防爆认证核查,确保符合GB/T 12476等工业防爆标准。
四、能耗分析与节能潜力挖掘
通过能耗监测仪表记录烘干炉的单位产量能耗(如kWh/kg),结合热效率计算(目标值通常>65%),评估设备能效水平。重点检测余热回收装置的工作状态,并分析排烟温度是否处于合理区间(建议≤120℃)。结合数据可优化干燥曲线、减少无效热损耗,实现节能降本。
五、结构稳定性与耐腐蚀性检查
针对烘干炉长期高温环境下的金属疲劳问题,需对炉体框架、传动部件进行超声波探伤或目视检查,发现裂纹或变形需及时修复。内胆及风道材料的耐腐蚀性也需通过厚度检测(如使用涂层测厚仪)评估,避免因材料劣化导致热效率下降或安全隐患。
六、环境排放合规性验证
根据环保法规要求,需检测烘干炉废气中的颗粒物、VOCs排放浓度,确保符合HJ 2537-2014《玻璃纤维工业污染物排放标准》。若配置湿式除尘或催化燃烧装置,还需验证其净化效率(一般要求≥90%)及运行稳定性。
总结
隧道式原丝烘干炉的检测需覆盖热工性能、安全防护、节能环保等多维度指标。建议企业结合设备使用说明书及行业标准(如JC/T 2345-2015),制定年度检测计划并建立设备健康档案。通过科学化的检测与维护,可显著延长设备寿命、降低故障率,同时为玻璃纤维高质量生产提供坚实保障。
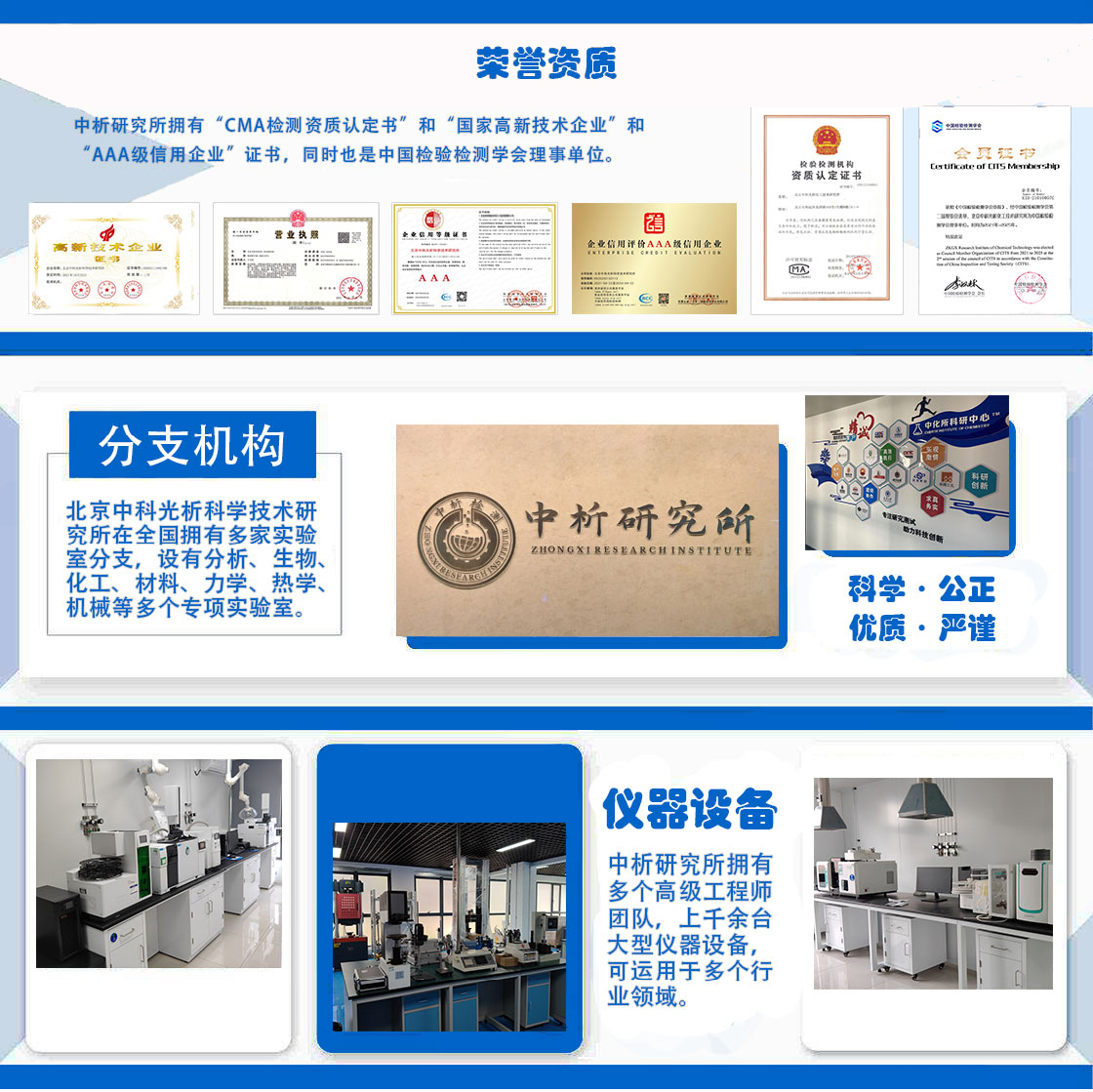
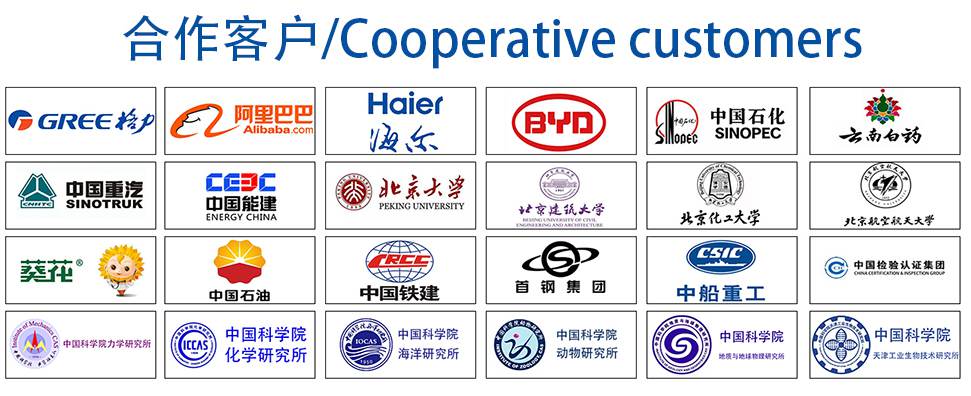