水泥工业用空气炮清堵器检测的重要性与核心内容
在水泥工业生产中,空气炮清堵器是一种关键设备,主要用于解决物料在储仓、料斗或管道中因结块、粘附引起的堵塞问题。其通过瞬间释放压缩空气产生冲击波,有效破除积料,保障生产流程的连续性。然而,空气炮长期运行在高温、高湿、高粉尘的恶劣环境中,其性能可能逐渐劣化。因此,定期开展空气炮清堵器的系统性检测,对确保设备可靠性、延长使用寿命及避免安全隐患至关重要。
空气炮清堵器核心检测项目
完整的空气炮清堵器检测需覆盖以下核心项目:
1. 结构完整性检查
重点检测罐体、喷嘴、法兰连接处的腐蚀、裂纹或变形情况,使用测厚仪测量罐体壁厚是否符合标准(通常≥6mm),检查密封件老化程度及防爆片有效期。对焊接部位进行渗透探伤,确保无隐蔽缺陷。
2. 气密性测试
将系统加压至1.0MPa额定压力后保压30分钟,允许压降不超过5%。采用气泡法检测电磁阀、管路接头泄漏点,尤其关注高温区域的密封件性能。对储气罐进行年度耐压试验,验证其承压能力。
3. 控制系统功能验证
测试电磁阀响应时间(应≤0.3秒),检查控制箱输入电压稳定性(波动范围±10%以内),模拟故障信号触发报警装置。通过时序测试确保多台空气炮的联动逻辑正确,避免同时动作导致气压不足。
4. 安全性能评估
核查安全阀启跳压力(设置值应为工作压力的1.1倍),检查压力表校准有效期(需符合JJG52标准)。对防爆型设备进行绝缘电阻测试(≥10MΩ),并确认防静电接地电阻≤4Ω。
5. 现场运行试验
在空载状态下进行10次连续触发测试,记录每次动作压力曲线,要求波动范围≤5%。实际投料后观察清堵效果,测量冲击波作用半径是否达到设计值(通常3-5米),并分析能量衰减规律。
6. 维护记录与周期管理
审查历史维护档案,评估关键部件更换周期合理性(如膜片每2年强制更换)。建立基于运行小时数的预防性维护计划,对高频率使用设备增加润滑点检查频次。
检测周期建议
常规检测应每季度执行一次功能性测试,每年进行深度检测。对于环境温度持续超过120℃或粉尘浓度>50mg/m³的工况,需将检测周期缩短30%。检测数据应纳入设备健康管理系统,结合振动、温度监测实现预测性维护。
总结
系统化的空气炮清堵器检测不仅能显著降低突发性故障风险,还可优化设备能效。通过建立标准化检测流程与数字化管理平台,水泥企业可提升清堵系统综合效率15%以上,同时减少因堵塞导致的非计划停机损失,为稳定生产和成本控制提供有力保障。
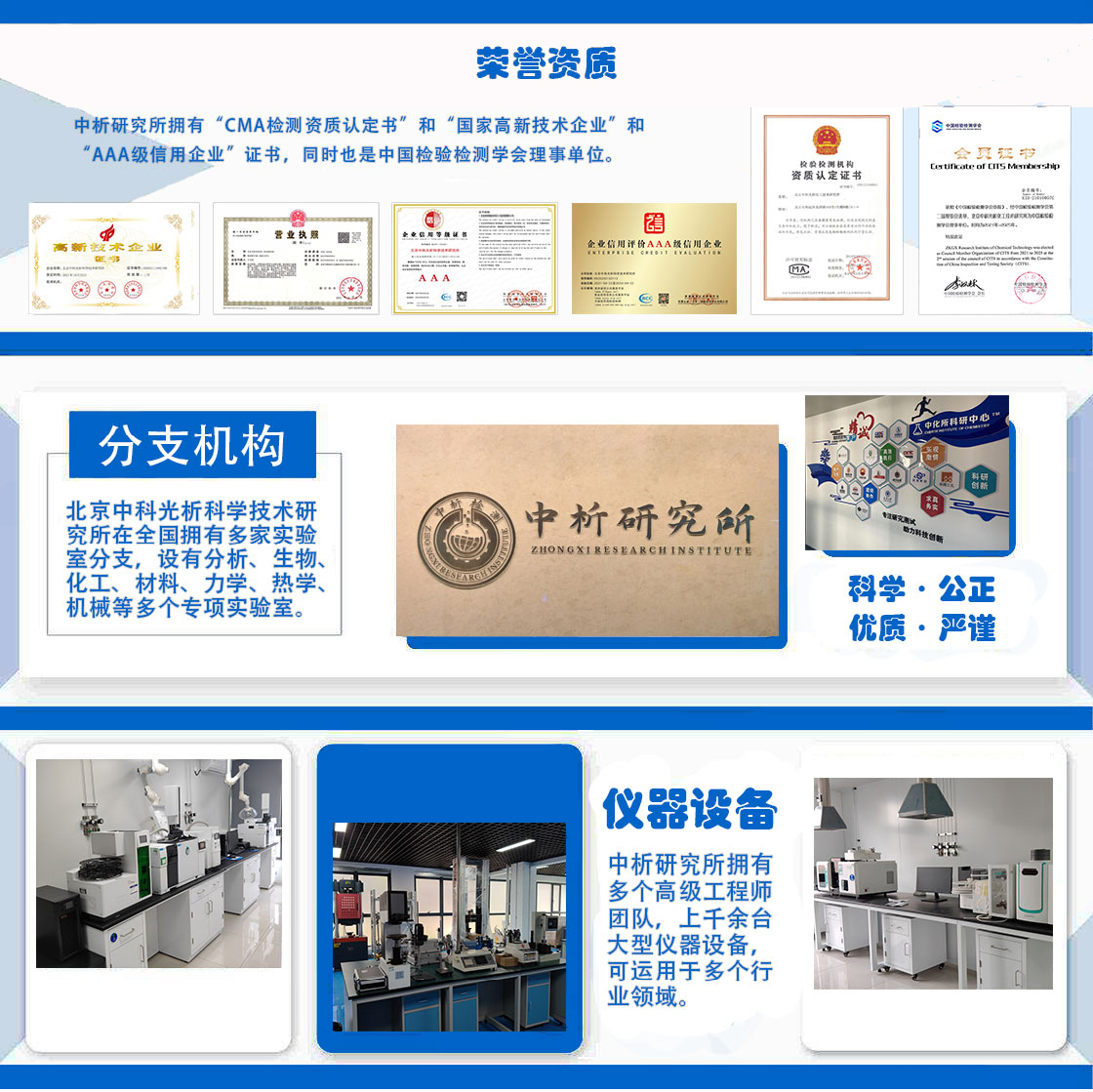
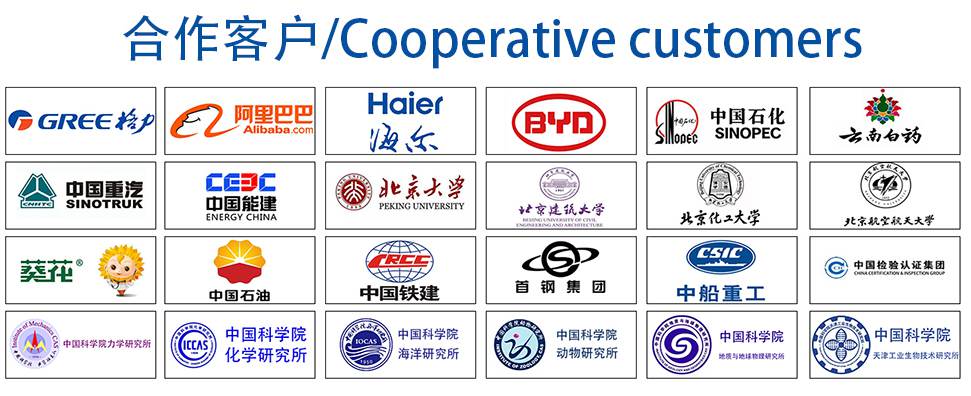