环形预应力混凝土电杆钢模检测的重要性
环形预应力混凝土电杆是电力输送和通信领域的关键基础设施,其钢模作为生产电杆的核心工具,质量直接关系到电杆的强度、耐久性和安全性。钢模检测旨在确保其几何精度、结构稳定性及材料性能符合国家标准(如GB/T 4623-2014),避免因模具缺陷导致电杆开裂、变形或承载力不足等问题。随着行业对电力设施可靠性要求的提升,钢模检测已成为电杆生产过程中不可或缺的环节。
核心检测项目及内容
1. 几何尺寸检测
通过激光扫描仪或三坐标测量仪对钢模的内径、锥度、长度等关键尺寸进行精确测量,确保其与设计图纸偏差不超过±1mm。重点检查合模间隙是否均匀,避免混凝土浇筑时漏浆或电杆表面不平整。
2. 材料性能检测
采用光谱分析仪验证钢材牌号(通常为Q235)是否符合要求,并进行硬度测试(布氏硬度≥120HB)、拉伸试验(屈服强度≥235MPa),同时检查焊缝质量(超声探伤合格率需达100%)。
3. 预应力系统检测
对张拉端锚具的定位精度(误差≤0.5mm)和承载能力(≥设计值的150%)进行测试,验证预应力筋布置的对称性。使用压力传感器校准张拉设备,确保张拉力控制误差≤3%。
4. 混凝土密实度验证
通过试生产电杆的超声波检测(波速≥4000m/s)或X射线探伤,分析混凝土是否存在蜂窝、孔洞等缺陷,同时检查电杆外表面的平整度和裂纹情况(允许裂纹宽度≤0.05mm)。
5. 耐久性测试
对钢模进行100次以上循环脱模试验,观测变形量(累积值≤0.2mm),并模拟极端环境(盐雾试验500小时)验证防腐涂层的附着力(划格法≥2级)和抗腐蚀性能。
6. 生产验证检测
连续生产30根标准电杆进行破坏性试验,检测抗弯承载力(需≥设计值的120%)、裂缝荷载(实测值/标准值≥1.05)等指标,全面验证钢模的工艺稳定性。
检测流程与质量控制
检测流程需遵循"进场初检-过程抽检-成品终检"三级体系,建立数字化检测档案。对于不合格项(如锥度偏差>1.5%),需进行模具校正或返厂维修,并通过复检闭环管理。检测机构应持有CMA/ 资质,确保数据权威性。
结语
通过系统化的钢模检测,可有效提升电杆生产合格率(目标≥99.5%),降低因模具缺陷导致的工程风险。随着智能检测技术(如机器视觉在线监测)的应用,未来钢模质量控制将向自动化、实时化方向发展,为电力基础设施安全提供更强保障。
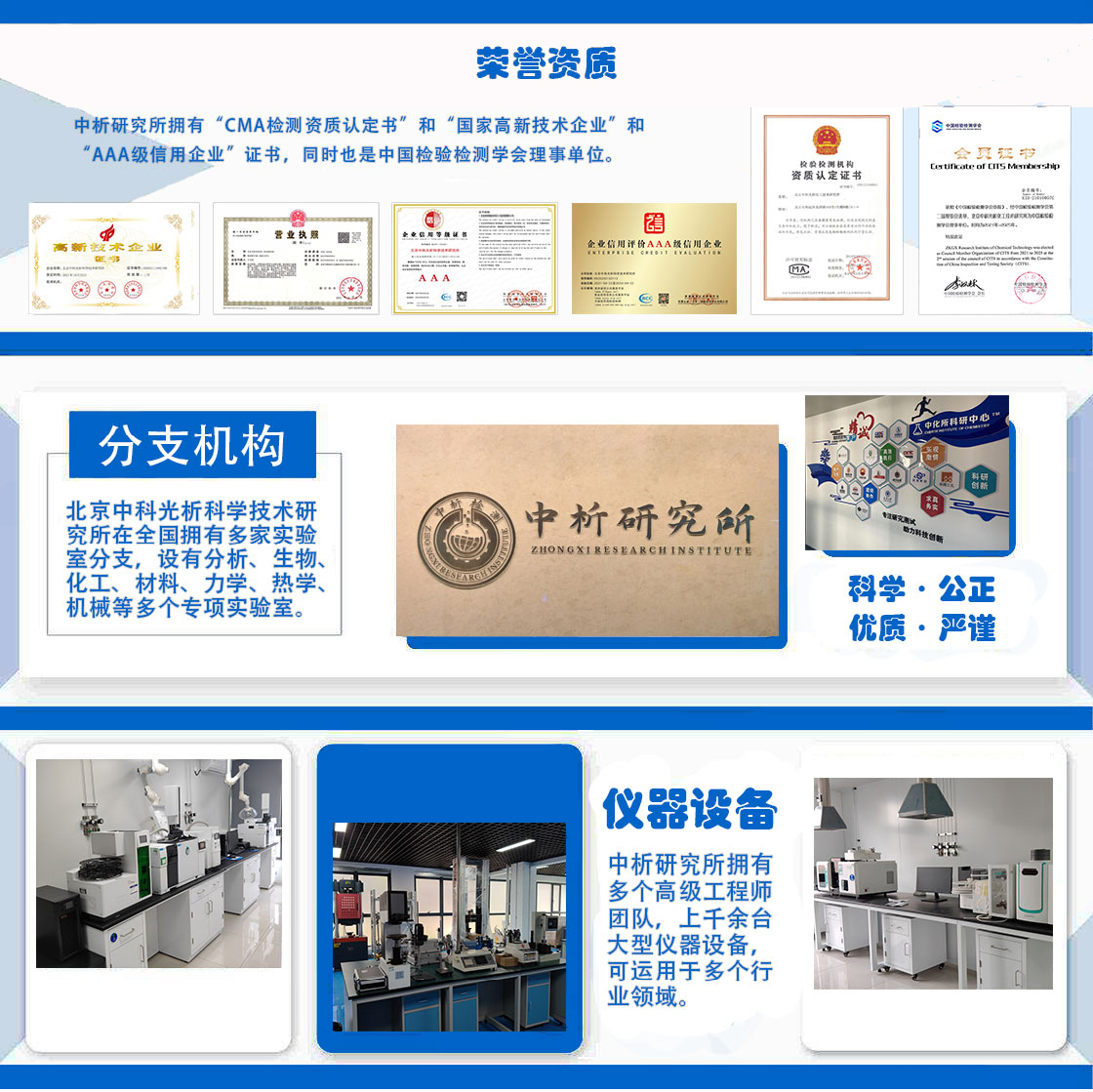
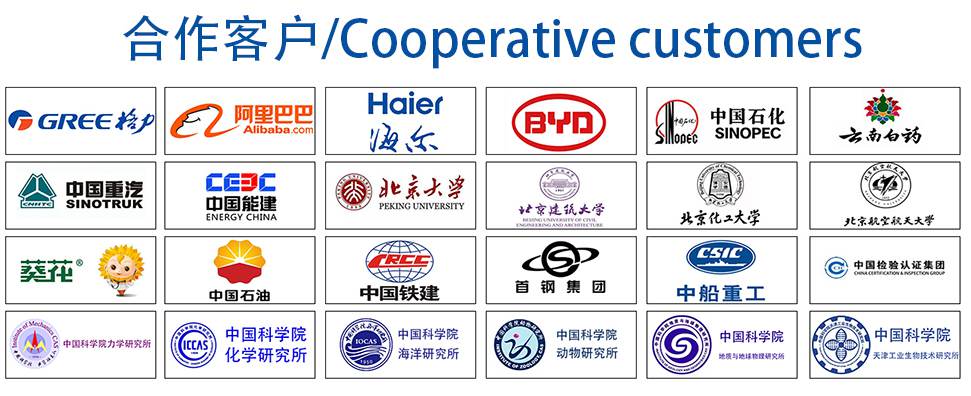