轨道交通车辆作为现代城市交通体系的核心装备,其轻量化、高强度与安全可靠性成为技术发展的核心诉求。铝合金挤压型材凭借优异的力学性能、耐腐蚀性及加工成型优势,已成为车体结构制造的主流材料。为保障车辆运行安全和使用寿命,需对铝合金型材进行系统性检测,覆盖原材料特性、加工工艺质量以及环境适应性等关键指标。
一、化学成分与金相组织检测
通过光谱分析仪测定型材的合金元素含量,确保符合GB/T 5237或EN 755标准规定的6061、6082等牌号要求。金相显微镜观测晶粒形态与第二相分布,评估材料热处理工艺的合理性,晶粒度应控制在5-8级范围。
二、力学性能测试
采用万能试验机进行拉伸试验,检测抗拉强度(≥260MPa)、屈服强度(≥240MPa)及延伸率(≥8%)。维氏硬度计测量材料硬度值,布氏硬度需达到75HB以上,同时进行弯曲试验验证型材的塑性变形能力。
三、尺寸公差与形位精度检测
使用三坐标测量仪对型材截面尺寸进行三维扫描,壁厚偏差需满足±0.2mm精度要求。激光轮廓仪检测直线度与平面度,轨道车辆用大型材的弯曲度不得超过1mm/m,扭拧度应小于2°。
四、表面质量综合评价
通过目视检查与表面粗糙度仪检测型材外观,划痕深度不得超过0.1mm,表面粗糙度Ra≤3.2μm。阳极氧化膜厚度检测需达到AA15级以上,盐雾试验480小时后腐蚀面积不超过5%。
五、焊接接头性能验证
对MIG/TIG焊接试样进行X射线探伤,依据ISO 10042标准评定焊缝质量等级。微观硬度测试焊缝区域与母材的硬度差应小于15HV,弯曲试验焊缝部位不得出现开裂现象。
六、无损检测与疲劳试验
采用超声波探伤检测内部缺陷,当量直径超过2mm的夹杂物需判定不合格。高频疲劳试验机模拟轨道车辆振动载荷,型材需通过200万次循环载荷测试无裂纹扩展。
通过上述多维度的检测体系,可有效保障铝合金挤压型材在复杂工况下的结构稳定性。检测机构需配备符合ISO/IEC 17025标准的实验室,结合数字孪生技术建立材料性能数据库,为轨道车辆的全生命周期管理提供技术支撑。
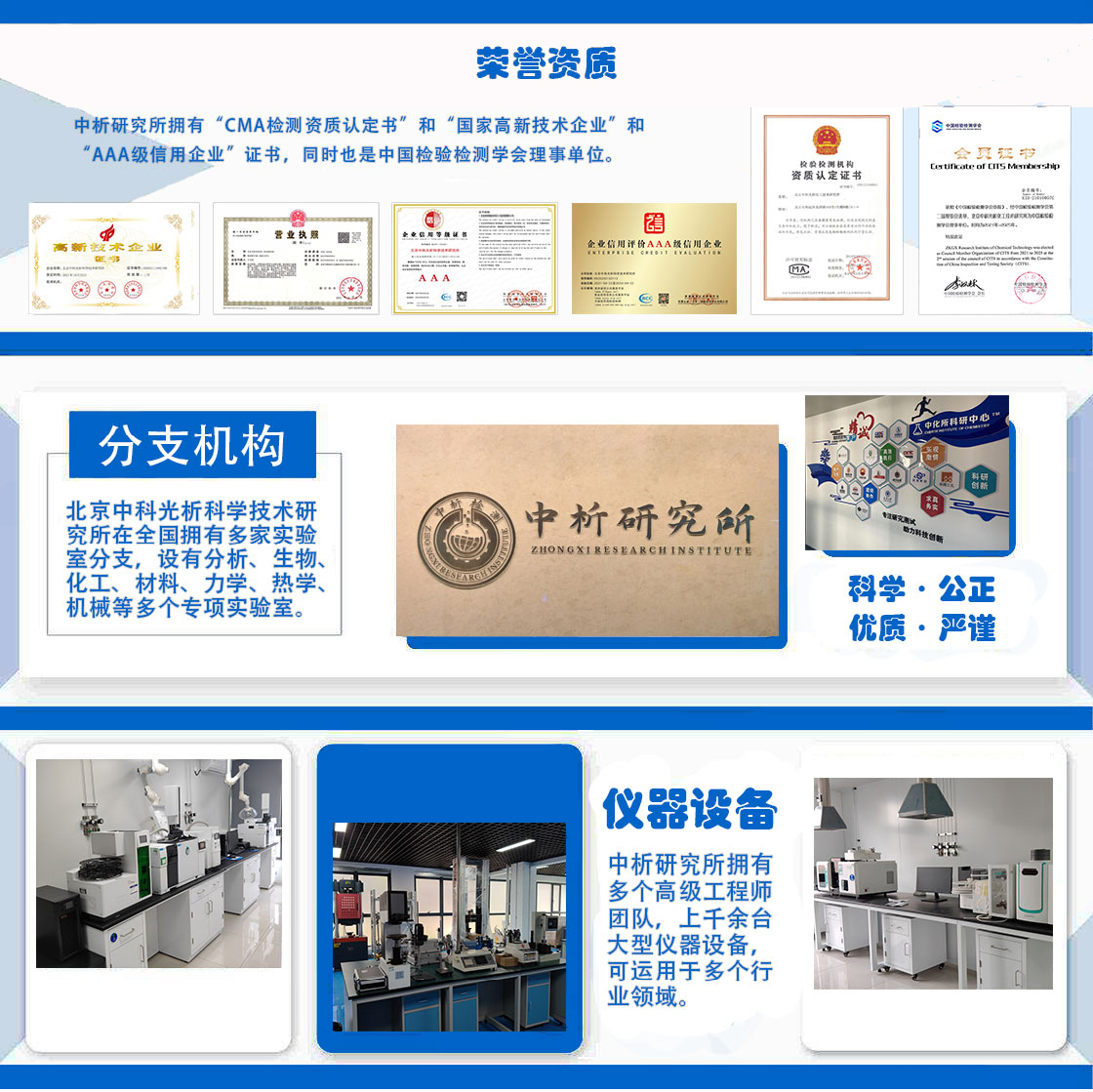
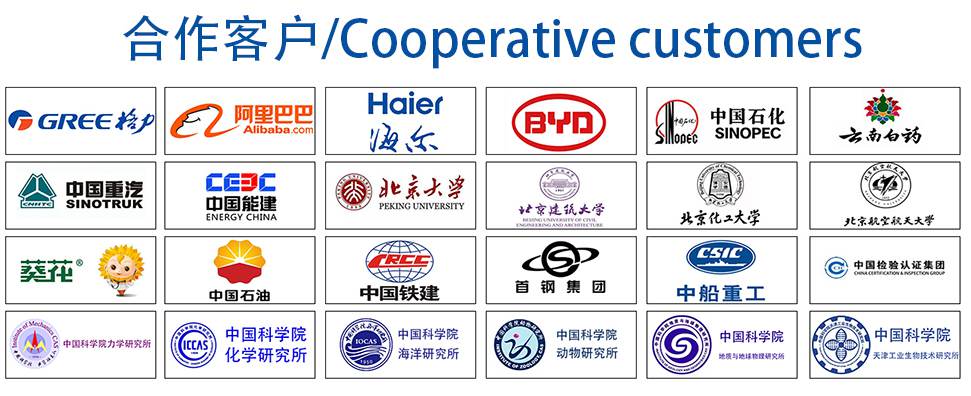