冷镦钢丝检测:确保材料性能与工艺适配性的关键环节
冷镦钢丝作为制造紧固件(如螺栓、螺母、螺钉)的核心原材料,其质量直接影响产品的机械性能和加工效率。随着汽车工业、机械制造及建筑工程领域对高强度紧固件需求的持续增长,冷镦钢丝检测已成为生产链中不可或缺的质量控制环节。通过系统化的检测流程,不仅可以验证材料是否符合国标(GB/T 6478)或国际标准(如ISO 4954),更能提前发现潜在缺陷,避免冷镦成型过程中的开裂、变形异常等问题,从而降低生产成本并保障终端产品的可靠性。
核心检测项目详解
1. 化学成分分析
采用直读光谱仪对C、Si、Mn、P、S等元素进行定量检测,确保符合牌号要求。例如SWRCH35K碳含量需控制在0.32%-0.38%,硫磷杂质需≤0.035%以保障冷镦性能。尤其关注残余元素(Cu、Cr等)对表面氧化皮形成的影响。
2. 力学性能测试
通过万能试验机开展抗拉强度(通常300-1000MPa)、断面收缩率(≥50%)、延伸率(≥15%)测试,配备引伸计获取精确应力-应变曲线。维氏硬度计检测HV硬度值,确保材料具备足够的塑性变形能力避免冷作硬化过度。
3. 表面质量检测
使用20倍放大镜目测检查划痕、折叠、裂纹等缺陷,配合涡流探伤仪检测皮下夹杂。表面粗糙度仪测量Ra值(应≤0.8μm),线材直径波动需控制±0.02mm以内。重点排查拉拔过程产生的螺旋纹与氧化铁皮残留。
4. 金相组织分析
制备纵向/横向试样,经4%硝酸酒精腐蚀后,通过金相显微镜观察铁素体-珠光体分布比例(理想比例为7:3),评估球化退火效果。检查脱碳层深度(全脱碳≤1.5%线径),晶粒度控制在6-8级以优化成型性。
5. 工艺适应性验证
进行实物镦粗试验(压缩比≥80%),模拟多工位冷镦过程。使用高速摄像机记录镦制过程中是否出现表面橘皮、微裂纹等异常,配合有限元分析软件评估材料流动均匀性,为模具设计提供数据支持。
检测技术新发展
智能化检测系统已实现在线直径测量(激光测径仪精度±0.001mm)、表面缺陷AI识别(深度学习算法识别率>98%)、超声波探伤(可检测Φ0.3mm以上夹杂物)等技术的集成应用。X射线荧光光谱仪(XRF)与直读光谱仪的联用,使元素分析效率提升60%以上。
结语
系统化的冷镦钢丝检测体系贯穿从原料入库到成品出厂的全流程,通过建立化学成分-力学性能-微观组织-表面质量的关联模型,可精准预测材料在高速冷成形中的表现。随着检测技术的智能化和标准体系的完善,冷镦钢丝质量控制正朝着更高效、更精准的方向持续演进。
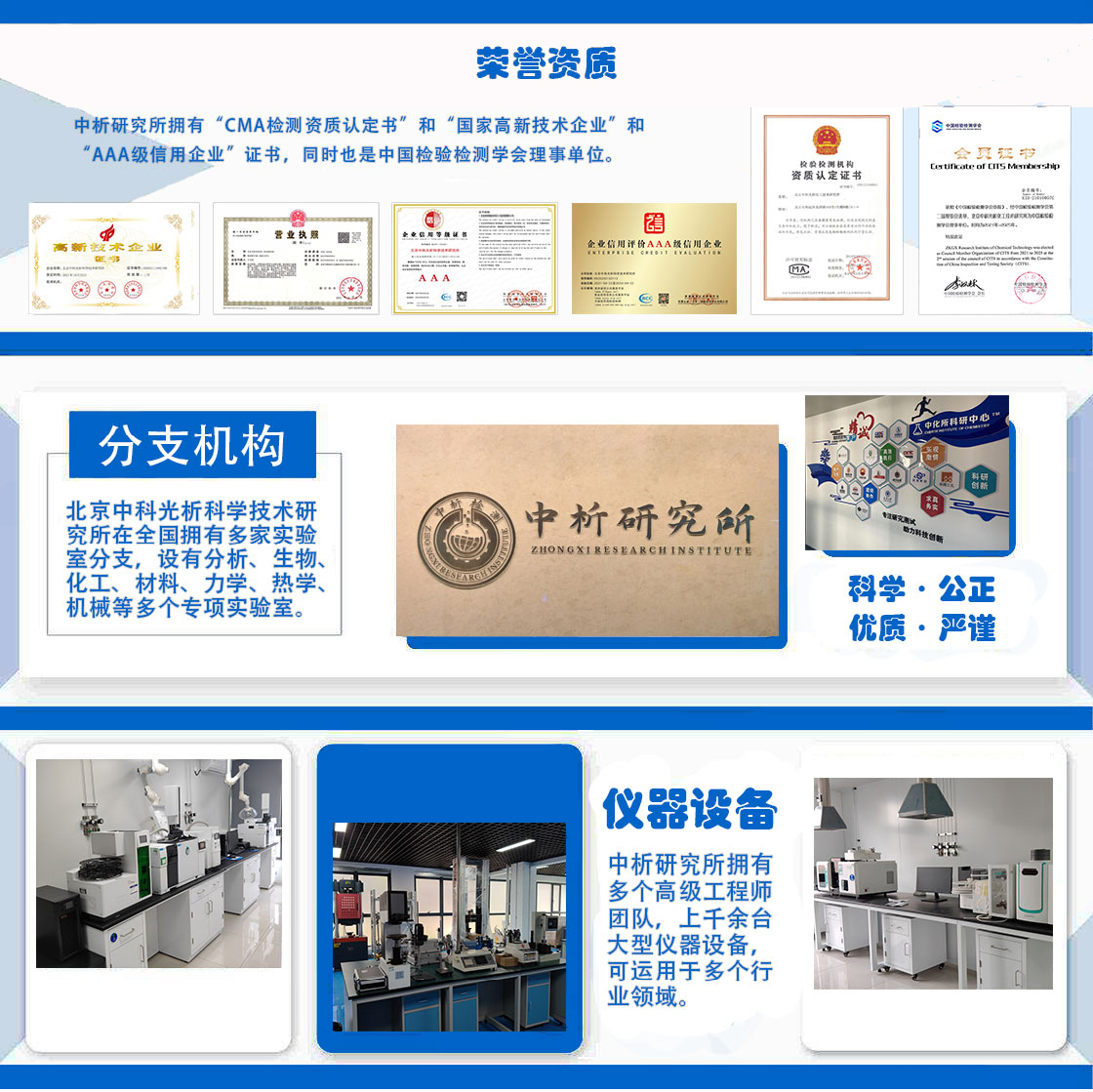
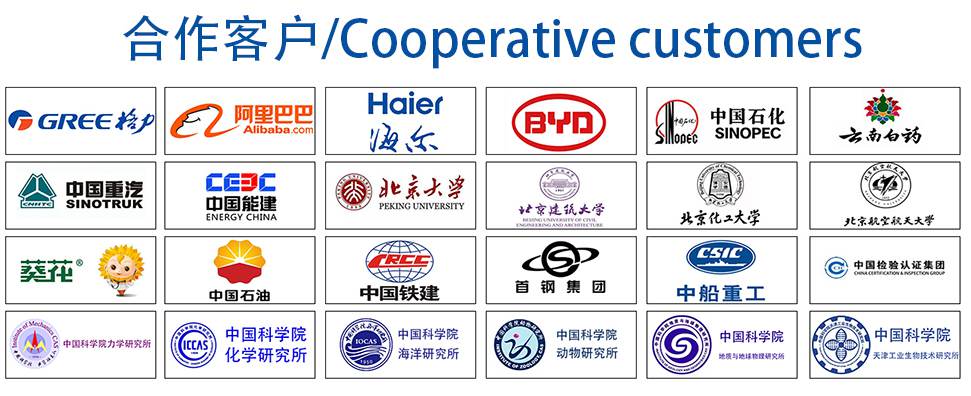