钢铁材料及制品化学成分分析检测的意义
钢铁作为现代工业的基础材料,其性能直接取决于化学成分的配比及杂质含量。化学成分分析检测是钢铁材料质量控制的核心环节,贯穿于原材料筛选、生产加工、成品检验及失效分析的全过程。通过精准测定钢铁中的碳、硅、锰、硫、磷等主量元素及铬、镍、钼等合金元素的含量,可确保材料满足强度、韧性、耐腐蚀性等关键指标要求。同时,该检测对优化生产工艺、降低能耗、提高产品附加值具有重要意义,尤其在高端装备制造、航空航天、新能源等领域,化学成分的严格管控已成为保障安全性和可靠性的必要手段。
主要检测项目及技术指标
1. 主量元素检测
碳(C):决定钢铁的硬度与强度,含量范围通常为0.02%-2.1%,低碳钢和高碳钢的性能差异显著;硅(Si)和锰(Mn):作为脱氧剂和强化元素,可提升材料的抗拉强度和耐磨性;硫(S)和磷(P):需严格控制的有害杂质,硫易导致热脆性,磷会增加冷脆风险。
2. 合金元素分析
铬(Cr)、镍(Ni)、钼(Mo):不锈钢及耐热钢的关键成分,铬含量超过10.5%时形成钝化膜,显著提升耐腐蚀性;镍可改善低温韧性,钼则增强高温强度。此类元素的检测精度需达到±0.01%级别。
3. 痕量元素检测
氧(O)、氮(N)、氢(H):气体元素含量直接影响材料内部缺陷,如氢含量过高可能引发氢脆断裂。现代检测技术需实现ppm(百万分之一)级灵敏度。
核心检测方法及标准
火花直读光谱法(OES)因快速高效(3分钟内完成多元素分析)成为主流方法;电感耦合等离子体发射光谱法(ICP-OES)适用于痕量元素检测;化学滴定法则用于仲裁性检测。国际标准(如ASTM E415、ISO 17025)与国家标准(GB/T 223系列)共同规范检测流程,确保结果可比性和溯源性。
应用场景与行业需求
从汽车发动机曲轴到核电站压力容器,化学成分检测报告是材料入厂的通行证。在风电叶片用钢中,硫含量需≤0.005%以避免疲劳失效;轨道交通用轴承钢的氧含量需控制在15ppm以下。第三方检测机构通过CMA/ 资质认证,为产业链提供从熔炼分析到成品验证的全链条服务。
技术发展趋势
随着激光诱导击穿光谱(LIBS)和人工智能算法的应用,现场快速检测与大数据驱动的成分预测成为新方向。未来,检测技术将向更高精度、更低检出限及智能化方向发展,为钢铁材料的绿色化、高端化转型提供支撑。
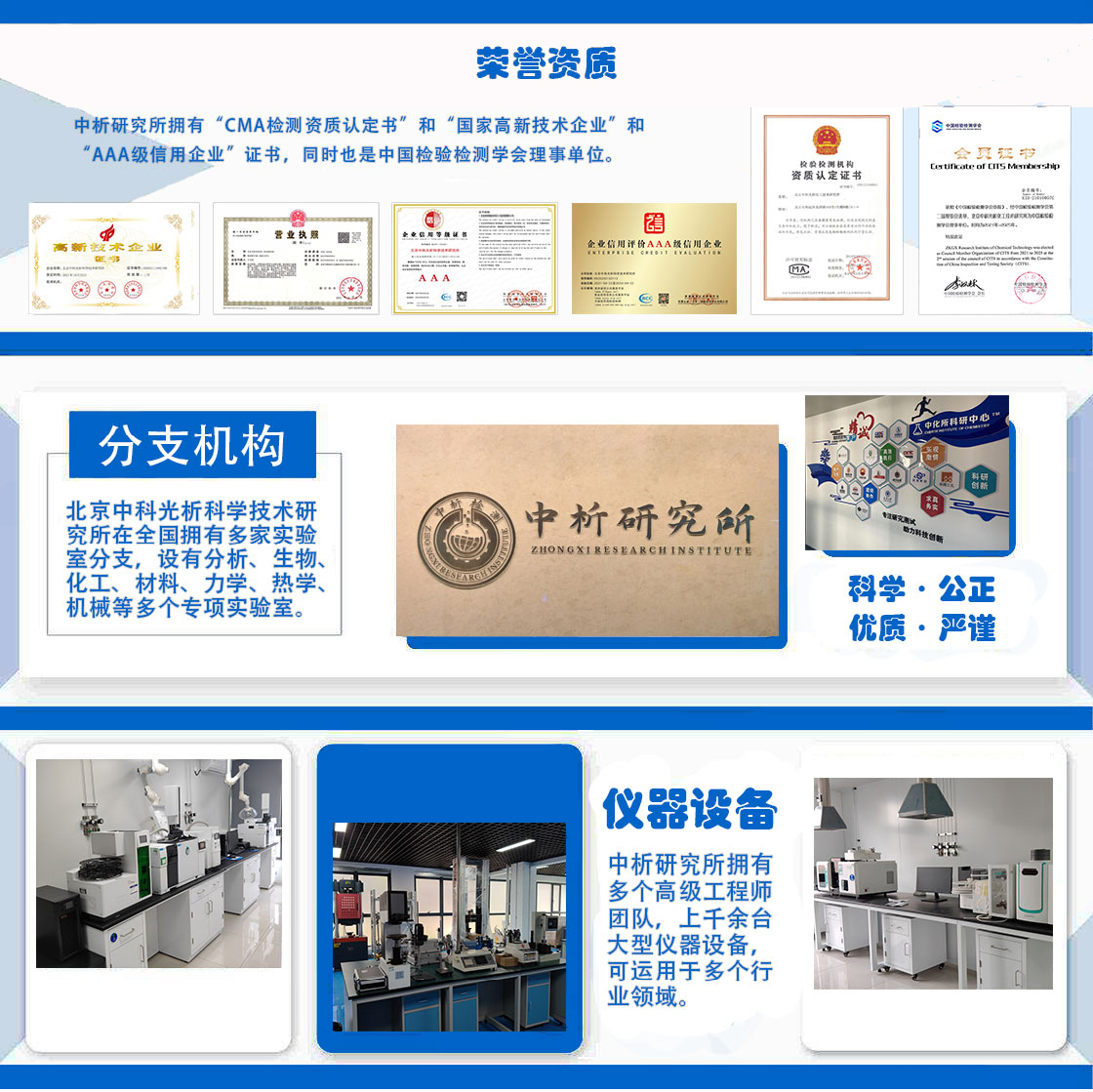
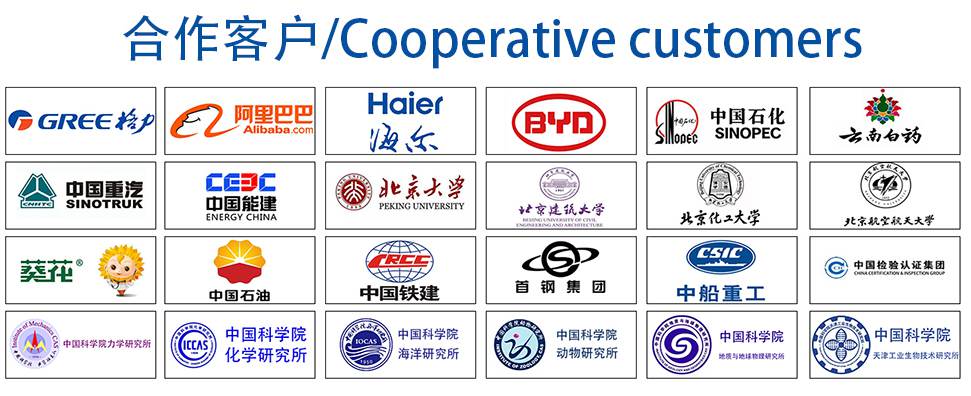