表面处理溶液检测的重要性
表面处理溶液广泛应用于电镀、阳极氧化、磷化、化学镀等工业领域,其质量直接影响金属基材的防腐性、耐磨性及涂层附着力等关键性能。溶液成分的稳定性、浓度配比以及污染物含量等因素,直接决定了表面处理工艺的成败。通过科学系统的检测手段,能够及时发现溶液老化、成分失衡或杂质超标等问题,从而避免因溶液失效导致的工件报废、能源浪费和生产停滞风险。表面处理溶液检测不仅是质量控制的关键环节,更是优化工艺参数、降低生产成本的重要依据。
核心检测项目及方法
1. pH值检测
pH值是衡量溶液酸碱性的核心指标。例如,酸性脱脂液pH需控制在1.5-3.0,碱性除油液则为10-12。检测时需使用经过校准的pH计,测试前需充分搅拌溶液以消除局部浓度差异。pH值异常会导致金属腐蚀速率失控或清洗效果下降。
2. 主盐浓度测定
采用化学滴定法(如EDTA络合滴定)或光谱分析法(ICP-OES)测定溶液中主盐(如硫酸铜、氯化镍)的浓度。例如,电镀铜液中Cu²⁺浓度需保持在15-25g/L范围,浓度过低会导致镀层孔隙率增加,过高则易产生粗糙镀层。
3. 添加剂含量分析
通过高效液相色谱(HPLC)或紫外分光光度法检测光亮剂、整平剂等有机添加剂的浓度。某锌酸盐镀锌液中DPE-III添加剂含量需维持在80-120mL/L,超出范围会导致镀层脆性增大或分散能力恶化。
4. 杂质离子检测
使用离子色谱仪(IC)或原子吸收光谱(AAS)检测Fe³⁺、Cr⁶⁺、Cl⁻等有害杂质。例如,镍镀液中Fe³⁺含量超过50ppm会引起镀层发黑,需通过电解处理或化学沉淀法进行净化。
5. 溶液电导率测试
采用电导率仪实时监测溶液导电性能,电导率值可间接反映总离子浓度。铝阳极氧化溶液电导率一般控制在12-18mS/cm,异常波动可能预示槽液污染或成分比例失调。
6. 有机污染物检测
通过总有机碳(TOC)分析仪测定溶液中有机物总量,配合红外光谱(FTIR)进行定性分析。磷化液中油脂残留超过0.5g/L时,将显著降低磷化膜致密性。
7. 温度与比重关联检测
使用比重计结合温度补偿功能,监控溶液比重变化。例如,化学镀镍液在30℃时标准比重为1.21-1.23g/cm³,比重下降0.02即需补充还原剂与稳定剂。
检测周期与标准规范
建议建立三级检测体系:在线监测(每2小时pH/温度)、日常检测(每班次主盐浓度)、全面分析(每周杂质与添加剂)。检测过程需严格遵循ISO 4527(化学镀镍)、ASTM B117(盐雾试验)等行业标准,确保检测数据的可比性和权威性。
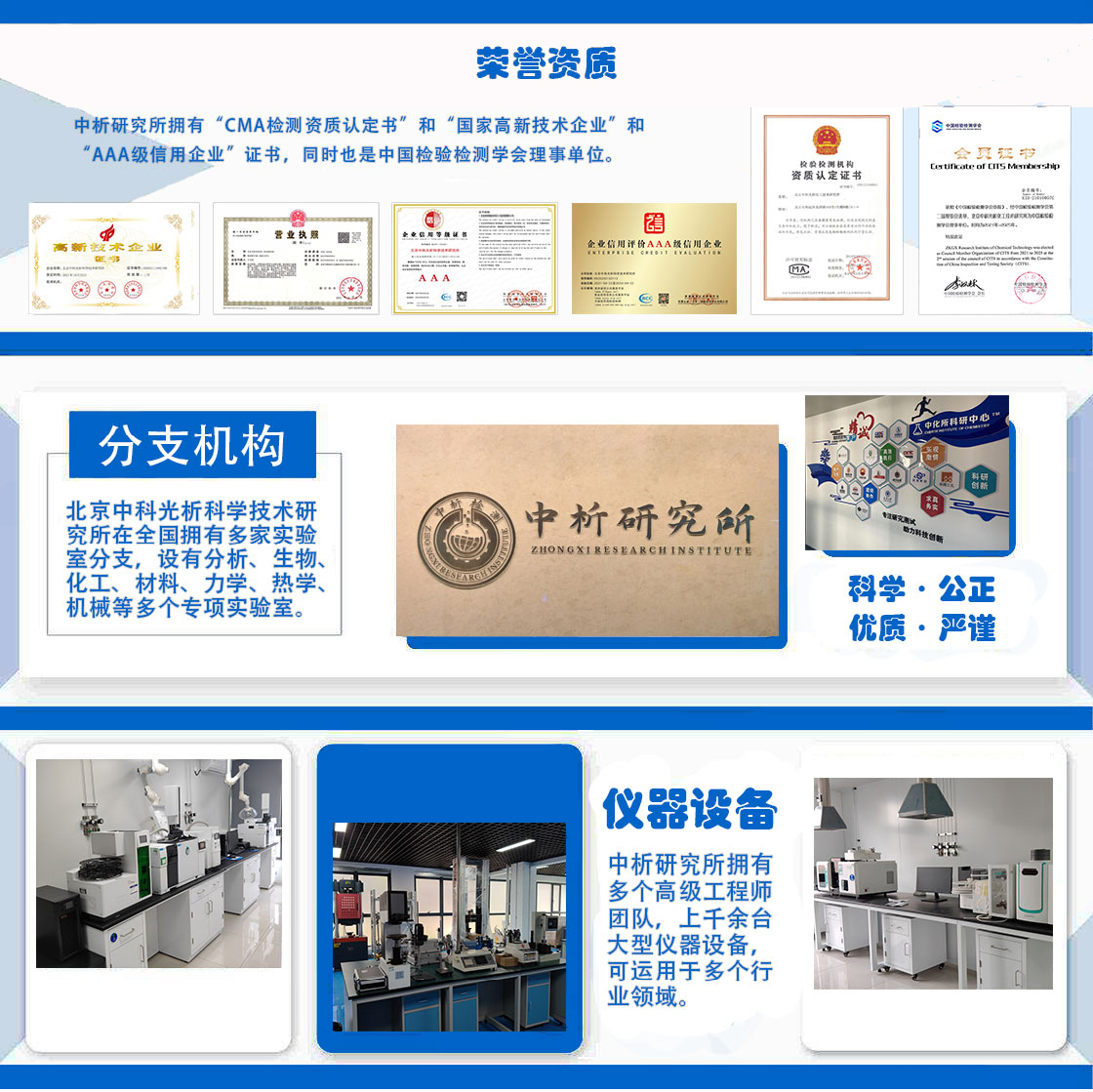
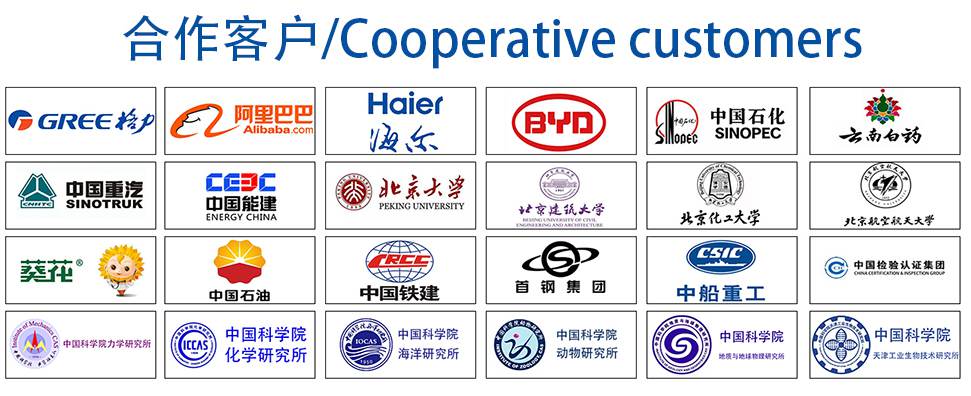