超温保护检测:保障设备安全的核心技术
在电子设备、工业机械、家用电器以及新能源汽车等领域,超温保护机制是确保设备安全运行的关键防线。当设备因过载、散热不良或环境温度异常导致内部温度升高时,超温保护系统通过传感器实时监测温度变化,并在达到预设阈值时触发保护动作(如断电、降频或报警),从而避免元器件烧毁、火灾甚至爆炸等严重后果。超温保护检测项目通过模拟极端工况、验证保护逻辑的可靠性和响应速度,确保这一安全机制在实际应用中能有效发挥作用。
核心检测项目及实施要点
1. 温度阈值准确性测试
通过高精度恒温箱或热成像仪模拟设备工作环境,逐步升高温度至预设保护点(如80℃±2℃),验证保护装置是否在设定范围内触发动作。需重复测试10次以上,统计触发温度的标准差,确保误差不超过行业标准(如IEC 60730-1规定的±3%)。
2. 响应时间与恢复性能验证
使用快速温度冲击试验设备,记录从温度超限到保护生效的时间(通常要求≤5秒),并检测温度回落后系统能否自动复位。对于新能源汽车电池管理系统(BMS),还需测试多次循环触发后保护功能的稳定性。
3. 多工况适应性测试
涵盖以下典型场景:
- 突发热冲击(如电机堵转瞬间温升)
- 缓慢温升(如散热器积灰导致的渐进过热)
- 局部热点检测(通过分布20+热电偶定位保护盲区)
- 电磁干扰下的误触发率(满足ISO 11452抗扰度标准)
4. 硬件冗余与软件容错检测
对双传感器备份系统进行单点失效测试,模拟主传感器故障时备份系统能否及时接管。同时通过注入故障代码,验证软件算法对异常温度数据的过滤能力和异常处理机制。
检测标准与设备要求
检测需符合GB 4706.1(家用电器)、UL 1998(工业控制)等标准,采用Class A级温度记录仪(精度±0.1℃)、可编程负载模拟器及符合ISO 17025认证的测试环境。对于智能硬件,还需通过CAN/LIN总线监测保护指令与设备状态的同步性。
检测结果分析与改进方向
典型不合格案例包括:
- 温度迟滞导致保护延迟(可通过优化传感器布局改善)
- 电磁噪声引发的误触发(需增加硬件滤波器)
- 高温老化后阈值漂移(建议选用抗老化NTC元件)
通过检测数据建立设备热模型,可进一步优化散热设计与保护参数,使安全性与设备性能达到最佳平衡。
超温保护检测不仅是产品认证的强制要求,更是预防重大事故的技术保障。随着智能物联网设备普及,融合AI算法的动态温度预测保护模式正在成为检测领域的新焦点。
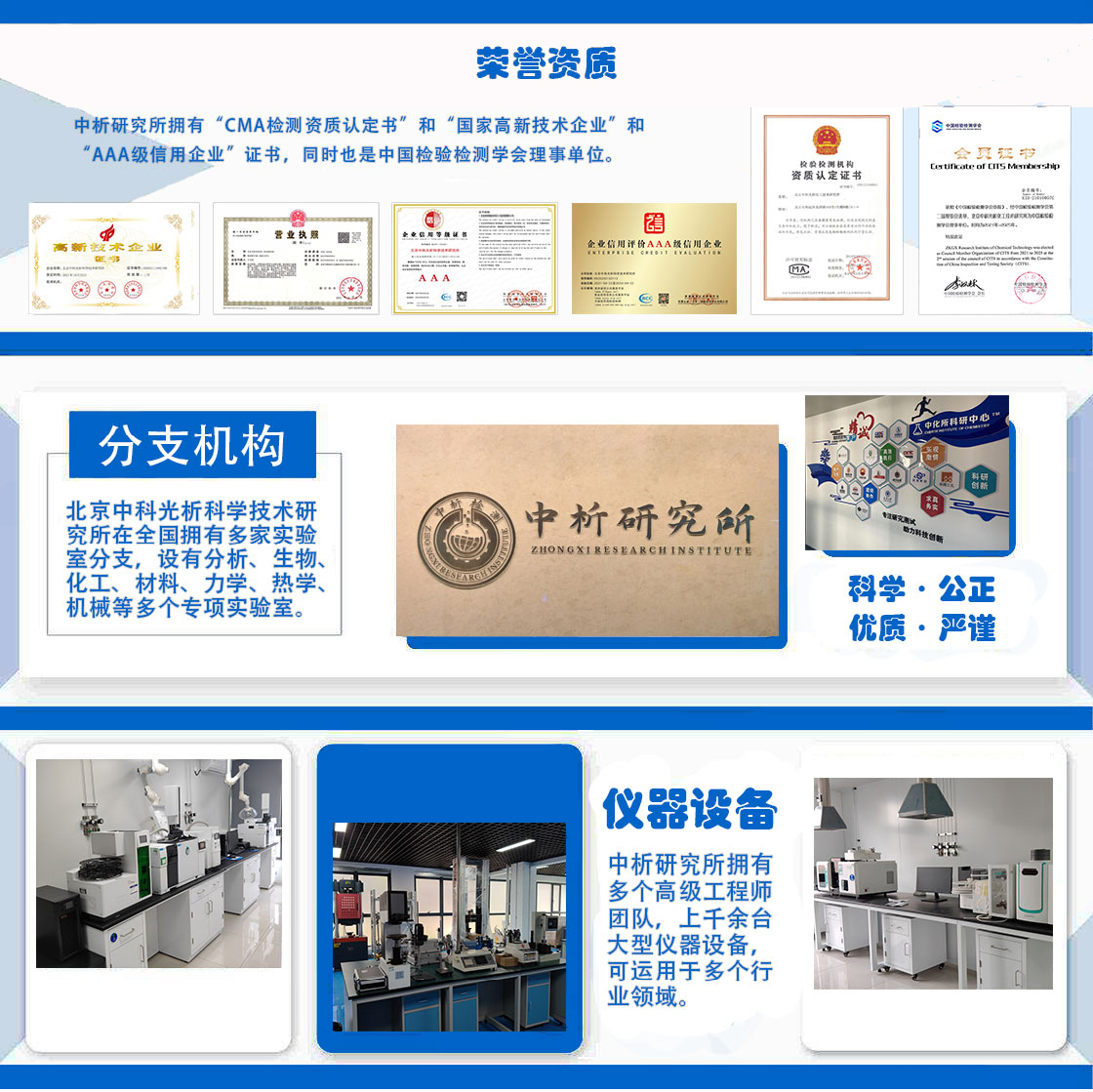
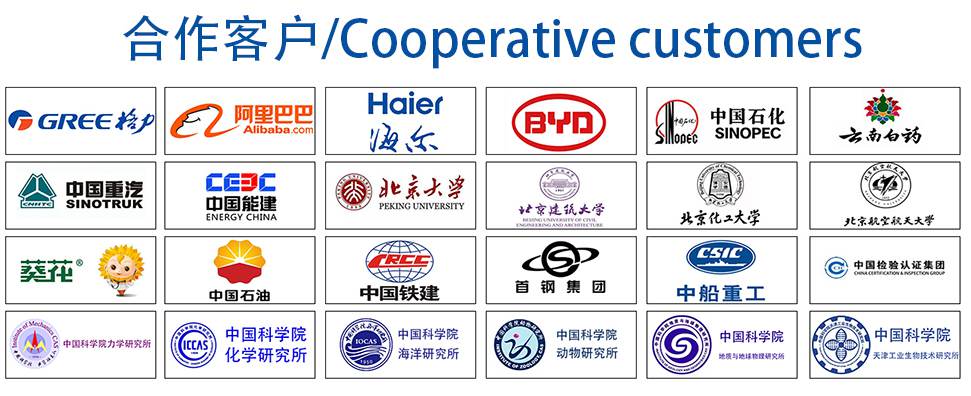